The automotive crankshaft market is poised for moderate expansion, propelled by advancements in engine technology and an increasing desire for fuel-efficient and high performance cars. Crankshafts play an essential part in improving engine efficiency while decreasing emissions thanks to breakthrough materials like lightweight alloys and improved forging techniques, manufacturers are meeting increasingly stringent fuel efficiency and emissions regulations by optimizing crankshaft performance and durability for improved vehicle efficiency and emissions levels.
Leading players should devote increased R&D investments toward refining product design and increasing production efficiencies, and to forming strategic alliances between OEMs and material suppliers for developing solutions meeting changing regulatory requirements and performance expectations. While electric vehicle (EV) sales will have long-term implications on this market, but its growth prospects still look positive, particularly among emerging economies.
Key Takeaways
- Global Automotive Crankshaft Market reach USD 5.56 Bn in 2033 at a CAGR of 3.1%.
- Asia Pacific leads the market, accounting for a 40.2% share due to strong automotive manufacturing activity and rising vehicle demand.
- Lightweight materials like high-strength steel and aluminum are leading to innovations in crankshaft production for greater fuel efficiency.
- Passenger vehicles lead the automotive crankshaft market due to rising global demand for more efficient engines.
Hybrid and diesel engines present growth opportunities as they rely on resilient crankshafts to ensure optimal performance.
- Technological innovations, including sensor integration and production automation, are helping improve crankshaft efficiency while cutting costs.
- Aftermarket demand for crankshaft replacements remains strong in regions with long vehicle lives and vibrant secondhand markets, particularly those characterized by an abundance of vehicle longevity.
Use Cases
- Passenger Vehicles: Crankshafts are integral components of gas-powered passenger cars, turning linear piston motion into rotational motion to propel them. As emission regulations tighten up further, lighter yet durable crankshafts constructed of advanced materials such as high strength steel or aluminum alloy are becoming more commonly employed to improve performance while meeting environmental requirements.
- Commercial Vehicles: Heavy-duty trucks and buses place significant mechanical stress on crankshafts. By employing forged steel crankshafts in commercial vehicles, durability and longevity are ensured allowing engines to handle greater torque levels with extended use, something essential in transportation and logistics sectors.
- Hybrid Vehicles: Although hybrid vehicles utilize both electric power and internal combustion engines, high performance crankshafts must still be utilized to optimally handle both engine power and torque from both sources, necessitating precision engineering in order to balance efficiency with performance.
- Motorsports and High-Performance Vehicles: High-performance and motorsport vehicles rely on crankshafts designed to withstand intense RPMs and stress, typically custom built from billet materials in order to maximize strength, reduce weight, and deliver faster acceleration; all factors which play an integral role in optimizing engine output for competitive racing.
- Aftermarket and Replacement Parts: Automotive crankshaft aftermarket sales are vast, particularly in regions with extended vehicle lifespan and used car markets. Replacement crankshafts for older cars with performance problems needing repair can extend their lifespan for cost-sensitive consumers who may opt for repairs over replacement purchases. High-quality crankshaft replacements can extend vehicle lifespan exponentially in these environments.
Driving Factors
Fuel Efficiency as the Driving Force behind Advanced Crankshaft Technologies
Fuel efficiency has become one of the primary driving forces in automotive crankshaft market growth worldwide. Governments worldwide are tightening emissions regulations, leading automakers to enhance engine efficiency through Crankshaft optimization for reduced friction and weight reduction - lightweight materials combined with advanced forging techniques are crucial to meeting consumer expectations and meeting this market trend.
Manufacturers continue investing heavily in advanced crankshaft technologies as consumer purchasing criteria remain key purchasing criterion; further contributing to its sustainable expansion.
Electric and Hybrid Vehicles Will Increase Market Demand: Their Impact Analysis
Electric and hybrid vehicle trends present both opportunities and challenges to the automotive crankshaft market. While fully electric vehicles do not need crankshafts for power transfer purposes, hybrid engines that combine internal combustion engines with electric motors still depend on durable crankshafts for effective transference of energy between different modes.
Hybrid vehicle sales are expected to experience compound annual compound annual compound annual compound annual compound compound compound compound annual compound growth between 2021-2026 with manufacturers being required to innovate to produce crankshafts capable of withstanding intermittent combustion requirements and higher torque variations while meeting these unique engine demands.
Technological Advancements: Strengthening Production Efficiency and Performance
Technological advancements in manufacturing processes are revolutionizing the automotive crankshaft market. Technologies like 3D printing, advanced forging, and precision machining have dramatically transformed production by improving design and manufacturing efficiency.
3D printing allows rapid prototyping and customization new materials such as titanium composites are being investigated to produce lighter yet stronger crankshafts tailored specifically for individual engine configurations furthermore new weight saving materials like carbon composites could further drive market expansion. These innovations help automakers meet increasingly stringent performance and environmental standards driving market expansion.
Growth Opportunities
Focusing on Lightweight Materials for Better Fuel Efficiency and Lower Emissions: Adaptations in Research.
2023 presents automotive crankshaft manufacturers with an opportunity to capitalize on lightweight materials like high-strength steel alloys, aluminum, and composites as lightweight alternatives that not only reduce overall crank weight but also enhance fuel economy and lower emissions.
As global emissions regulations tighten up more frequently, automakers are turning more towards lightweight components to comply with stringent emissions standards; companies investing in developing lightweight designs will be well suited to capitalize on this trend and drive growth worldwide.
Collaboration With Automotive Manufacturers: Tailoring Solutions To Meet Specific Performance Needs
Strategic partnerships between crankshaft manufacturers and automotive OEMs present many opportunities in 2023. By working collaboratively, manufacturers can produce crankshafts tailored specifically to modern engine performance requirements such as increased torque or fuel economy enhancements.
Furthermore, such partnerships foster innovation by permitting crankshaft manufacturers to employ cutting-edge materials and design techniques; when OEMs seek custom solutions that differentiate their vehicles through customisation strategies such collaborations will become key growth drivers.
Growing Popularity of Diesel Engines: Sustaining High-Durability Crankshaft Demand
Though electric vehicles continue to gain ground in commercial vehicle use, diesel engines remain widely utilized throughout developing regions of the globe. Due to their combustion characteristics, diesel engines require crankshafts capable of withstanding higher stress and vibration levels in 2023 - providing opportunities for crankshaft manufacturers who produce durable yet high performance components for heavy-duty applications that maintain demand in this segment.
Trends of Vehicle Downsizing: Rising Demand for Custom Crankshaft Designs
Vehicle downsizing to improve fuel economy drives demand for innovative crankshaft designs. Downsized engines that utilize turbocharging require high efficiency crankshafts in order to perform at their full potential despite reduced size - creating an opportunity for manufacturers to create innovative crankshaft solutions which support fuel-efficient, high performing engines in smaller vehicles and help expand market reach in 2023.
Key Trends
Integration of Advanced Sensors: Maximizing Engine Monitoring and Performance
Integrating advanced sensors into crankshafts has emerged as a trend in 2023's global automotive crankshaft market, providing real-time data about engine performance, efficiency, wear, diagnostics and maintenance - offering automakers valuable insights for improving diagnostics and maintenance practices.
Crankshafts equipped with sensors allow predictive maintenance practices such as reduced downtime and enhanced vehicle performance; especially important when used on high-performance vehicles or fleet vehicles where precise engine monitoring can optimize operations while cutting costs.
Focusing on Sustainability in Crankshaft Manufacturing: Exploring Eco-Friendly Solutions
Sustainability is increasingly shaping crankshaft manufacturing today. Manufacturers in 2023 are exploring eco-friendly materials and adopting more eco-friendly production processes in an attempt to minimize environmental impact using recycled material, cutting energy consumption during production, and switching toward cleaner manufacturing technologies have all become key considerations in production processes. With regulations surrounding emissions tightening worldwide and sustainability becoming ever more integral aspects of market dynamics and positioning strategies.
Automation for Crankshaft Production: Optimizing Efficiency and Cutting Costs
Automation and robotics are revolutionizing crankshaft production processes in 2023. Leveraging advanced automation technologies enables manufacturers to achieve greater precision, reduce labor costs, increase production efficiencies, scale operations while still upholding quality standards more easily, speed product development processes up, meet rising customer expectations for customized performance crankshafts across different vehicle segments faster and increase profitability. This trend allows crankshaft manufacturers to scale operations while remaining highly-rated manufacturers.
Heightening Standards for Noise, Vibration and Harshness (NVH): Promoting Driver Comfort
Automakers have responded to consumer demands for improved driving comfort by prioritizing noise, vibration and harshness (NVH) reduction efforts. Crankshafts designed to minimize vibrations and noise have gained prominence within the marketplace - driving innovation within crankshaft materials and designs in an attempt to produce components which contribute towards quieter engine operations.
Restraining Factors
High Replacement Costs Are an Obstacle to Market Expansion
One of the key restraining factors of automotive crankshaft market growth is the high replacement costs associated with crankshaft replacement. While crankshafts are essential components, their wear and tear over time is significant - particularly on older vehicles - leading to replacement expenses that exceed parts replacement expenses, often necessitating engine disassembly which incurs substantial labor and parts expenses for consumers these high replacement expenses act as deterrents to regular maintenance or repair schedules or lead them further from keeping up with repairs - possibly leading them further from regularly scheduled replacement or abandonment altogether.
Automotive manufacturers face a unique set of difficulties in producing crankshafts made with advanced materials like titanium or carbon composite, the added expense being made more challenging by high replacement costs that deter investments into new components that drive market expansion.
Maintenance expenses play a substantial role here and this problem also plagues fleet operators and commercial vehicle owners, where maintenance expenses play an outsized part in overall operational expenses; further compounded by higher replacement costs that discourage frequent investments into new components that drive growth of market expansion.
Fluctuating Oil Prices Are Influencing Consumer Behaviour and Vehicle Purchase Decisions
Fluctuating oil prices represent another significant barrier for automotive crankshaft markets. When oil prices increase, so too do fuel costs - leading to changes in consumer behaviors like reduced vehicle usage or delayed purchases of new or aftermarket components like crankshafts. Uncertain economic environments also influence consumers to prioritize maintenance/repair costs or opt for fuel-efficient models like electric or hybrid cars as a form of economic security.
These shifting preferences could reduce demand for internal combustion engine vehicles and their components - such as crankshafts - as consumers opt for alternatives less dependent on oil.
If oil prices were especially volatile, vehicle sales might further drop and crankshaft demand reduced by attrition in supply chains and production cycles. Furthermore, oil price uncertainty complicates automotive manufacturers' forecasting efforts when planning supply chains or production cycles of crankshaft components and increases operational risk management efforts for automotive suppliers.
Research Scope and Analysis
By Material
By 2023, forged steel had established itself as the dominant market player within the By Material segment of the automotive crankshaft market with more than 42.0% share. Preferred for their superior strength, durability and resistance to fatigue they are ideal for high-performance heavy-duty applications like commercial vehicles where fuel efficiency and lightweight crankshafts have further strengthened forged steel's position within this segment.
Cast iron/steel crankshafts also captured strong market shares due to their cost effectiveness and wide use in mass market vehicles, which means their popularity continues to be steady across developing regions where price sensitivity plays a pivotal role in automotive manufacturing. Cast iron/steel crankshafts offer an ideal blend of performance and affordability making them popular with midrange and budget vehicle models alike also seen steady use in midrange sports utility vehicles (SUV).
Machined billet crankshafts may make up only a minority share of the market, yet are experiencing steady growth within niche applications - particularly high-performance and luxury vehicles. Custom made from top quality materials with precise engineering features for precise engineering, strength and stress resistance machined billet crankshafts have gained ground as demand increases for performance-oriented engines in motorsports and premium vehicles, increasing demands for machined billet. Yet their high production costs restrict its wider adoption beyond specific niche use cases.
By Type
Flat Plane crankshafts were the clear market leaders in 2023 for automotive crankshaft market's By Type segment, holding more than 67.8% market share. Their popularity among high-performance and sports vehicles due to faster acceleration, reduced engine weight and superior exhaust scavenging capabilities has created increased demand. Their simpler designs also led to lighter crankshafts which contributed towards fuel economy and agility when driving performance-oriented vehicles.
Cross-plane crankshafts accounted for a smaller but significant share of the market due to their extensive use in larger engines that power luxury, muscle, and commercial vehicles. Cross-plane crankshafts are well known for their superior balance and smooth operation, which reduces vibration while improving driving dynamics in engines with higher torque outputs. Crankshafts designed specifically to reduce noise, vibration and harshness (NVH) are particularly popular with V8 engines. Their design provides optimal comfort and performance by significantly decreasing NVH.
By Vehicle Type
Passenger Car was the top vehicle type segment within automotive crankshaft market in 2023, accounting for more than 61.67% market share by vehicle type in terms of By Vehicle Type segment of Automotive Crankshaft Market. This success can be explained by increased consumer preferences for lightweight fuel efficient vehicles in regions like Asia-Pacific and Europe where emission regulations and rising consumer preferences for personal mobility play an influential role in growth drivers.
Furthermore, advancements in crankshaft materials and technologies that enhance fuel economy align perfectly with an emphasis on sustainability as well as vehicle downsizing efforts - further cementing passenger Car's leadership in terms of market position.
Commercial Vehicles made up a smaller segment of the market, yet their role was vital in industrial and logistical applications. Commercial vehicles such as trucks and buses depend on crankshafts with sufficient strength to withstand greater stresses, and higher engine loads. As global trade and e-commerce flourish, commercial vehicle demand continues to soar, particularly in regions with developing infrastructure.
This growth trend illustrates a steady demand for reliable crankshafts within this segment - specifically diesel-powered engines typically used by commercial fleets. As commercial vehicle electrification adoption remains slower than that seen with passenger cars, this ensures that internal combustion engines, and thus crankshafts, will maintain sustained demand in the near term, even as markets move towards alternative powertrain solutions.
The Automotive Crankshaft Market Report is segmented based on the following:
By Material
- Forged steel
- Cast iron/steel
- Machined billet
By Type
By Vehicle Type
- Passenger Car
- Commercial Vehicle
Regional Analysis
Asia Pacific achieved dominance of the global automotive crankshaft market in 2023 by holding over 40.2% market share. This surge was propelled primarily by China, India and Japan's expanding automotive industries that include major production facilities for passenger and commercial vehicle manufacturing facilities like Chong Qing Group Co in Shanghai rising passenger and commercial vehicle demand as well as production facility investments contributed to crankshaft demand in this region plus its growing middle class populations coupled with urbanization rates supporting higher vehicle sales that contributed further to Asia Pacific's market dominance and its position within it this global automotive crankshaft market dominance.
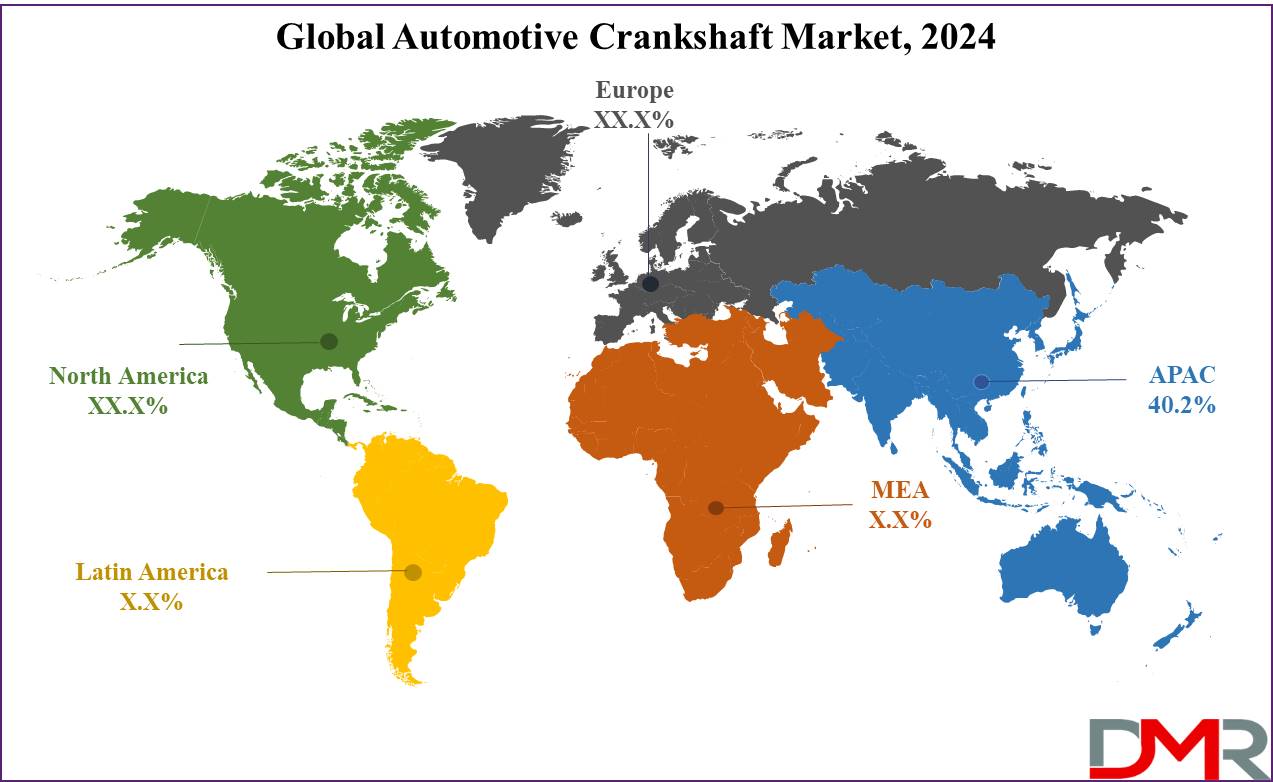
North America holds an expansive share in the crankshaft market due to the presence of key automotive manufacturers and an established aftermarket sector. Demand for high-performance crankshafts remains strong among commercial vehicle owners in North America; more specifically in the US where emissions-reduction initiatives and increasing vehicle performance boost adoption of advanced crankshaft technologies.
Europe is marked by stringent environmental regulations and leading automotive OEMs from countries like Germany, France and Italy which demand lightweight yet fuel efficient crankshafts. Although electrification poses significant challenges in Europe's automotive sector, hybrid vehicles continue to drive demand in the short to medium term for such crankshafts.
Latin America and Middle East/Africa account for smaller shares of global vehicle sales but are experiencing steady expansion thanks to increasing vehicle ownership rates and infrastructure development initiatives. Latin America specifically is experiencing rising commercial vehicle demand while Middle East/Africa countries benefit from growing investments in transport infrastructure projects.
By Region
North America
Europe
- Germany
- U.K.
- France
- Italy
- Russia
- Spain
- Benelux
- Nordic
- Rest of Europe
Asia-Pacific
- China
- Japan
- South Korea
- India
- ANZ
- ASEAN
- Rest of Asia-Pacific
Latin America
- Brazil
- Mexico
- Argentina
- Colombia
- Rest of Latin America
Middle East & Africa
- Saudi Arabia
- UAE
- South Africa
- Israel
- Egypt
- Rest of MEA
Competitive Landscape
In 2023 key players of the global automotive crankshaft market continue to shape industry dynamics through innovation, strategic collaborations and expansion into global markets. Companies like Maschinenfabrik ALFING Kessler and TIANRUN CRANKSHAFT remain market leaders by emphasizing precision engineering to produce high-performance crankshafts for both passenger and commercial vehicles Rheinmetall and Thyssenkrupp stand out due to advances in lightweight materials as well as their commitments towards sustainability that allow them to meet stringent fuel efficiency regulations as well as emissions requirements Rheinmetall and Thyssenkrupp stand out due to advancements made possible thanks to forging expertise combined with material science in order to meet stringent fuel efficiency regulations while meeting stringent fuel efficiency/emission regulations respectively.
Bharat Forge of India continues its global expansion due to rising demand from emerging markets and robust manufacturing capabilities. Bharat's innovative crankshaft technologies enable it to serve various automotive and industrial applications; similarly, North American players NSI Crankshaft Company and Kellogg Crankshaft Company remain key players based upon their established track records of producing durable yet high-quality crankshafts that satisfy performance-oriented applications.
Farndon Engineering and Crower Cams & Equipment specialize in producing custom-built high-performance crankshafts to serve motorsports and specialty automotive markets, with special expertise in producing billet crankshafts with tailored solutions to maintain relevance in premium vehicle segments.
Sandvik, known for its material innovations, plays an instrumental role in providing advanced alloys that improve crankshaft durability and performance in high-stress applications. As market conditions shift and evolve, leading companies such as Sandvik must remain innovative by meeting automotive industry demands like electrification and fuel efficiency upgrades with innovative approaches.
Some of the prominent players in the Global Automotive Crankshaft Market are:
- Maschinenfabrik ALFING Kessler
- Sandvik
- TIANRUN CRANKSHAFT
- Rheinmetall
- NSI Crankshaft,
- Thyssenkrupp
- Farndon Engineering
- Kellogg Crankshaft Company
- Bharat Forge
- Crower Cams & Equipment
Recent developments
- Bharat Forge, a Tier-1 supplier for automotive and other industries, acquired another business worth Rs 850 crore in the automotive and industrial services sector. They shared this news to investors through regulatory filing.
- ThyssenKrupp Crankshaft Company LLC's Material Services have continued their expansion across North America with plans to open a new facility in San Luis Potosi in Mexico - investing USD 37 Million as part of an effort to ensure future viability in the automotive supply sector.
- In February 2023, MM Forging announced its board had authorized a plan for merging Cafoma Autoparts Private Limited - its fully owned subsidiary that manufactures crankshafts - with MM Forgings Limited. This merger plan will facilitate integration and unification across company activities resulting in operational synergies while eliminating redundant efforts across different entities.
- Guangxi Yuchai Machinery Group Co. Ltd (Yuchai) announced in February 2023 that Guangxi Yuchai CrankShaft Co. Ltd, its wholly-owned subsidiary, began manufacturing of an expensive crankshaft requested by German automaker Audi AG - specifically an 8kg 6-cylinder crankshaft made out of forgings to fit premium engine models manufactured in Germany. This project marks an exciting step in Yuchai's growth as an automotive component manufacturer and will contribute substantially towards increasing German automotive R&D capability within 2023!
Report Details
Report Characteristics |
Market Size (2023) |
USD 4.1 Bn |
Forecast Value (2032) |
USD 5.56 Bn |
CAGR (2023-2032) |
3.1% |
Historical Data |
2018 – 2023 |
Forecast Data |
2024 – 2033 |
Base Year |
2023 |
Estimate Year |
2024 |
Report Coverage |
Market Revenue Estimation, Market Dynamics, Competitive Landscape, Growth Factors and etc. |
Segments Covered |
By Material(Forged steel, Cast iron/steel, Machined billet), By Type(Flat Plane, Cross Plane), By Vehicle Type(Passenger Car, Commercial Vehicle) |
Regional Coverage |
North America – The US and Canada; Europe – Germany, The UK, France, Russia, Spain, Italy, Benelux, Nordic, & Rest of Europe; Asia- Pacific– China, Japan, South Korea, India, ANZ, ASEAN, Rest of APAC; Latin America – Brazil, Mexico, Argentina, Colombia, Rest of Latin America; Middle East & Africa – Saudi Arabia, UAE, South Africa, Turkey, Egypt, Israel, & Rest of MEA
|
Prominent Players |
Maschinenfabrik ALFING Kessler, Sandvik, TIANRUN CRANKSHAFT, Rheinmetall, NSI Crankshaft,, Thyssenkrupp, Farndon Engineering, Kellogg Crankshaft Company, Bharat Forge, Crower Cams & Equipment |
Purchase Options |
We have three licenses to opt for: Single User License (Limited to 1 user), Multi-User License (Up to 5 Users), and Corporate Use License (Unlimited User) along with free report customization equivalent to 0 analyst working days, 3 analysts working days and 5 analysts working days respectively. |