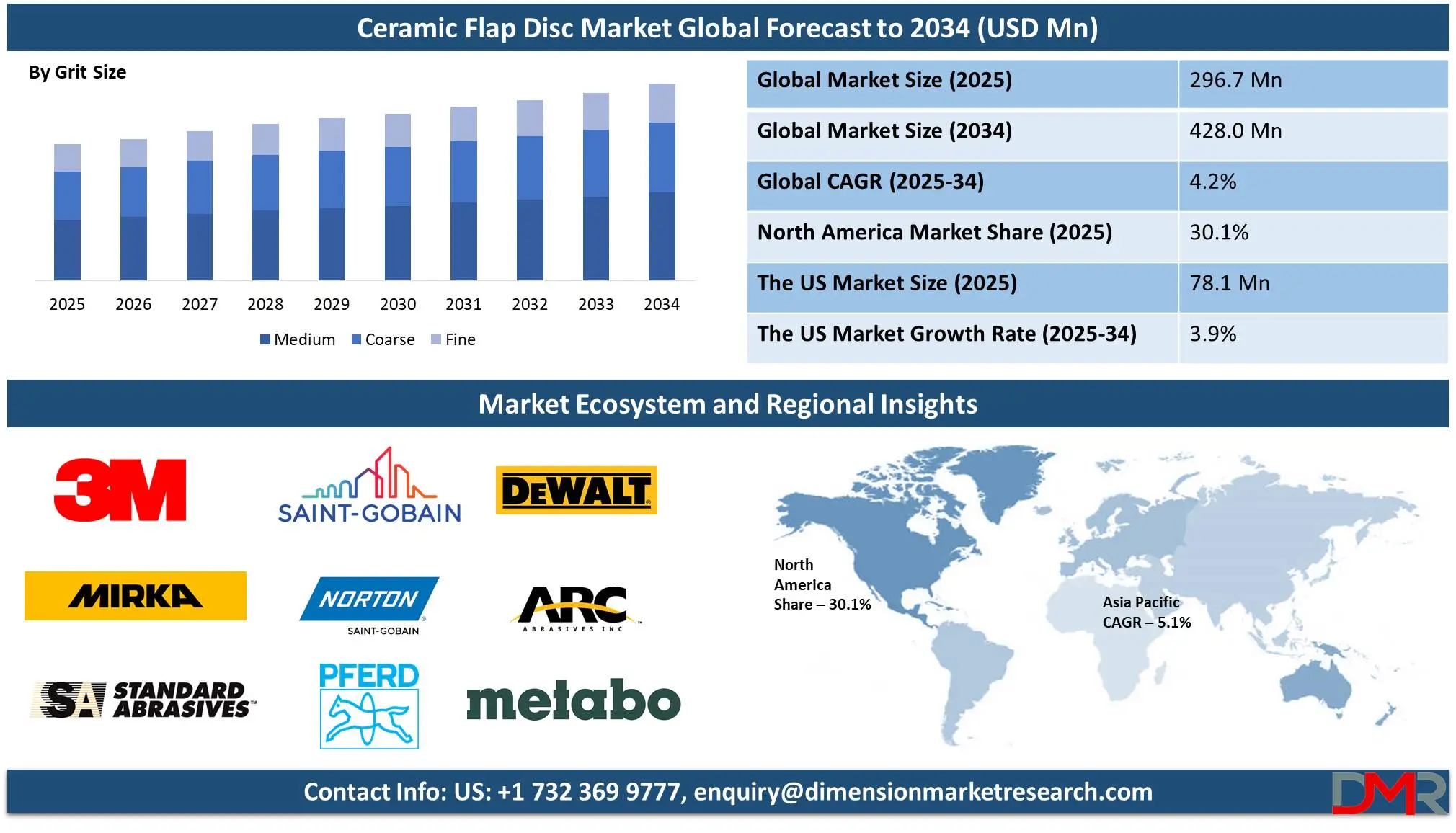
Ceramic flap discs are tools for grinding, sanding, and finishing metal and other materials. Consisting of overlapping abrasive flaps bonded to a backing plate made from fiberglass or plastic material, their main feature is their ceramic abrasive grains, which provide sharper cuts with a longer lifespan than traditional aluminum oxide products while producing less heat while creating smooth finishes more quickly while creating less heat than aluminum oxide products do, widely used across metalworking, welding and fabrication applications.
In addition, ceramic flap discs have seen higher demand recently due to industry demands for efficient and long-lasting grinding tools. Industries including automotive, aerospace, shipbuilding, and construction use them for precise metal shaping and finishing applications. Furthermore, automation and advanced manufacturing processes have led companies to look for high-performance abrasives that improve productivity while decreasing costs; additionally, the shift towards sustainable production encourages their use. Ceramic flap discs last longer than traditional grinding wheels while simultaneously decreasing waste.
One major development in the industry is self-sharpening ceramic grains. These abrasives break down to expose new sharp edges for consistent performance over an extended lifespan. Another trend involves noise and vibration-reducing designs for discs used over long periods by workers; manufacturers also increasingly focus on customized grit sizes and coatings tailored specifically for different applications (stainless steel, carbon steel and titanium grinding for instance).
Further, several notable events have shaped the ceramic flap disc market significantly. Firstly, the pandemic caused disruptions to supply chains, impacting raw material availability and production; as industries recovered, however, demand increased significantly due to infrastructure projects and industrial activities requiring high-grade abrasives. Technological developments also brought with them improved bonding materials and disc designs, enhancing durability and efficiency.
Companies also expanded their reach through online sales networks, making these tools accessible worldwide. Businesses are opting for ceramic flap discs over conventional grinding wheels owing to their long-term cost-effectiveness. Though initially more costly, their longer lifespan and superior performance reduce replacement frequency, saving money while improving workflow efficiency. Furthermore, being compatible with high-speed grinders without excess heat generation makes these discs ideal for modern manufacturing processes.
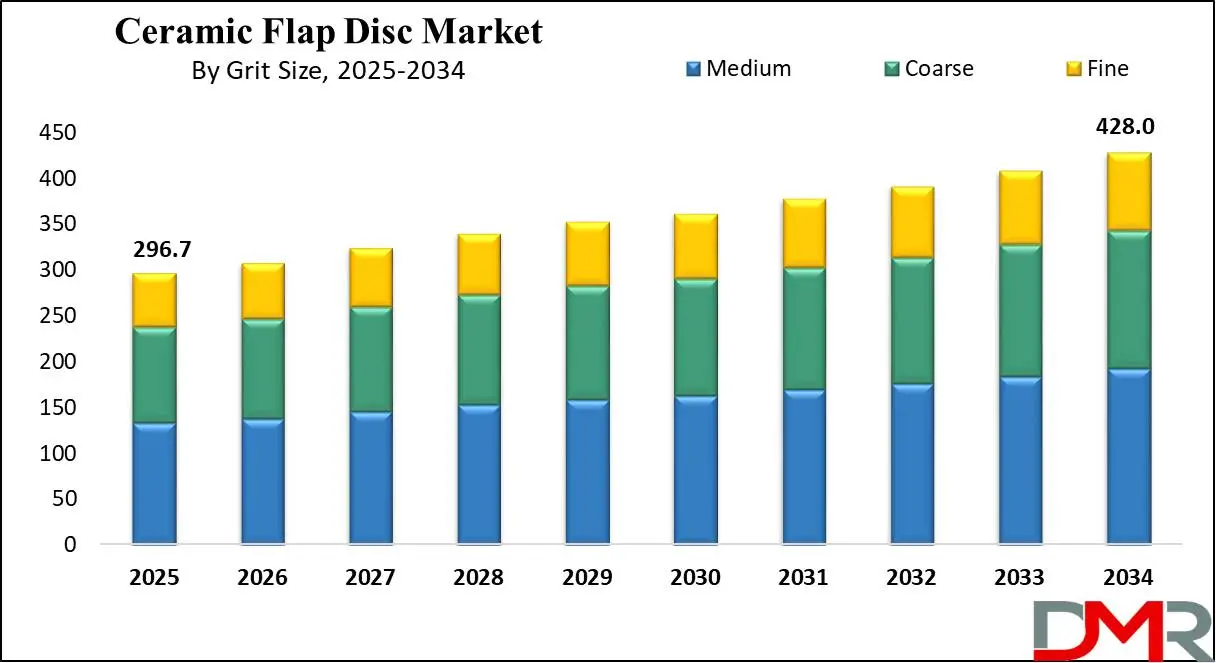
In the future, the ceramic flap disc market is projected to experience steady expansion as industries demand better, longer-lasting abrasives. Advancements in material science, automation, and sustainability will likely make ceramic flap discs even more effective and widespread; as manufacturers create eco-friendly variants that meet high-performance criteria, ceramic flap discs will continue to serve professionals involved with metalworking and fabrication as a valuable resource.
The US Ceramic Flap Disc Market
The US Ceramic Flap Disc Market is projected to reach USD 78.1 million in 2025 at a compound annual growth rate of 3.9% over its forecast period.
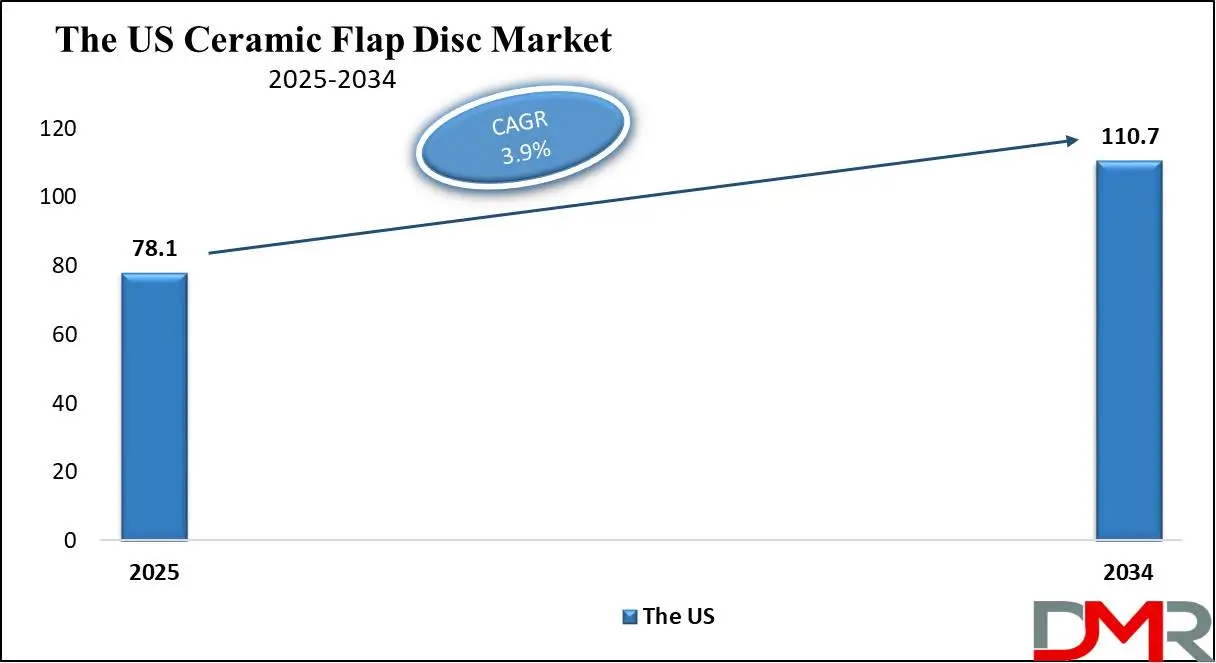
In the US, growth opportunities in the ceramic flap disc market depend on expanding automation in industries like automotive, aerospace, and metal fabrication. The increasing demand for high-performance abrasives in infrastructure projects and advanced manufacturing presents potential. Additionally, the shift towards eco-friendly products and sustainable practices offers opportunities for innovation and market expansion.
Further, there is increasing demand for high-performance abrasives in industries like automotive and manufacturing. However, a restraint is the high cost of ceramic flap discs compared to alternatives, which may limit adoption, especially for small businesses. Sustainability trends also influence the market's growth potential.
Ceramic Flap Disc Market: Key Takeaways
- Market Growth: The Ceramic Flap Disc Market size is expected to grow by 120.3 million, at a CAGR of 4.2% during the forecasted period of 2026 to 2034.
- By Grit Size: The medium segment is anticipated to get the majority share of the Ceramic Flap Disc Market in 2025.
- By Diameter: The 4 to 8-inch is expected to be leading the market in 2025
- By End User Vertical: The metal fabrication segment is expected to get the largest revenue share in 2025 in the Ceramic Flap Disc Market.
- Regional Insight: APAC is expected to hold a 37.8% share of revenue in the Global Ceramic Flap Disc Market in 2025.
- Use Cases: Some of the use cases of ceramic flap discs include welding & metal fabrication, automotive repair, and more.
Ceramic Flap Disc Market: Use Cases:
- Welding and Metal Fabrication: Ceramic flap discs are mainly used in welding to smooth weld seams, remove excess material, and prepare surfaces for further processing like painting or coating, providing a high-quality finish.
- Surface Grinding and Smoothing: These discs are ideal for grinding metal surfaces to remove rust, paint, or other contaminants, providing precise and even finishes on steel, aluminum, and other metals.
- Deburring and Edge Finishing: Ceramic flap discs are effective for deburring sharp edges and smoothing rough surfaces, mainly in metalworking applications, improving the appearance and safety of finished products.
- Automotive Repair: In automotive industries, they are used to remove imperfections, smooth body panels, and prepare surfaces for painting or refinishing, providing faster and more efficient results.
Stats & Facts
- According to the U.S. Geological Survey Publications Warehouse, in 2023, garnet for industrial use was mined by three companies, one in Montana and two in New York, with processing facilities in Oregon and Pennsylvania. The estimated value of crude garnet production was about USD 15 million, while refined garnet sold or used had an estimated value of USD 52 million.
- Further, the major end uses of garnet, in descending order, included abrasive blasting, water-filtration media, water-jet-assisted cutting, and other applications like abrasive powders, nonslip coatings, and sandpaper. Also, domestic industries that consume garnet include aircraft and motor vehicle manufacturers, ceramics and glass producers, electronic component manufacturers, filtration plants, the petroleum industry, shipbuilders, textile stonewashing, and wood furniture finishing.
- In addition, in 2023, U.S. domestic production of crude garnet decreased by 11% compared to 2022, mainly due to the closure of the Emerald Creek Garnet Mine in Idaho in July 2022. The U.S. accounted for about 7% of total global garnet production, while the refined garnet sold or used remained nearly the same as in 2022.
- According to the U.S. Geological Survey Publications Warehouse, Garnet imports in 2023 fell by 40% compared to 2022, mainly due to decreased imports from Canada, China, and India. The average unit value of imported garnet was USD 190 per ton, slightly lower than in 2022, while domestically produced crude garnet concentrate was priced at about USD 220 per ton. Additionally, U.S. exports of garnet declined by 18%, and total domestic consumption fell by 35%, reaching an estimated 210,000 tons.
- Further, the U.S. natural gas and petroleum industry is a major consumer of garnet, using it for cleaning drill pipes and well casings and as a reservoir-fracturing proppant. In early 2023, 772 drill rigs were operating in the U.S., but by October 2023, the number had dropped to 622, likely reducing garnet consumption in well drilling. The garnet market is highly competitive, with companies focusing on high-grade garnet ores or producing garnet as a byproduct of other minerals like kyanite, marble, mica, and metallic ore minerals
- According to Volza's Global Export data, from March 2023 to February 2024, there were 2,777 shipments of Flap Disc And HSN Code 6804 worldwide, with 701 exporters supplying 862 buyers. This marked a 20% growth in exports compared to the previous 12 months, showing increasing global demand. However, between January and February 2024, exports declined by 21%, despite a 6% year-on-year increase compared to February 2023.
- Also, the top destinations for Flap Disc And HSN Code 6804 exports were India, Peru, and Indonesia, highlighting strong demand in these markets. China, Turkey, and India were the top three global exporters, with China leading with 8,811 shipments, followed by Turkey (896 shipments) and India (640 shipments). The data is updated until June 27, 2024, and paid subscribers can access full details of Volza's export-import database for deeper insights.
Market Dynamic
Driving Factors in the Ceramic Flap Disc Market
Ceramic Flap Discs Are Expanding Demand in Industrial Applications
Ceramic flap discs have become an essential asset to various industrial applications like metal fabrication, automotive repair, and construction. Their versatility and effectiveness have driven their demand from industries like metal fabrication, automotive repair, and construction, especially as the likes of aerospace, shipbuilding, and manufacturing expand their need for high-performance abrasives like ceramic flap discs, which provide durability, heat resistance, and consistent performance perfect for heavy-duty grinding, finishing, and deburring tasks as the global industrial sector grows. The ceramic flap disc market should experience sustained growth, especially from emerging economies where manufacturing activities are increasing significantly
Advancements in Abrasive Technology
As technology evolves, advancements in abrasive technology are increasing ceramic flap disc performance to become more cost-effective and efficient, increasing their performance and adoption across global markets. Such advancements allow for faster material removal, smoother finishes, and extended tool life for greater productivity in various industries, such as automotive and aerospace manufacturing processes and robotics that use ceramic flap discs. With technological innovations continuing, ceramic flap discs will continue playing an ever more crucial role in modernizing industries worldwide and will continue to gain adoption globally.
Restraints in the Ceramic Flap Disc Market
High Cost of Ceramic Flap Discs
One major barrier to growth for the ceramic flap disc market is their higher cost relative to other forms of abrasives. While ceramic flap discs provide superior performance, their higher initial investment might dissuade some companies from selecting them when more budget-friendly options like aluminum oxide or zirconia discs exist; cost considerations could hinder adoption more in developing economies where financial limitations are prevalent.
Limited Availability of Raw Materials
Ceramic flap discs depend on specialty abrasive grains like ceramic alumina that may be difficult to source in large amounts, posing difficulties when manufacturing ceramic flap discs in larger batches. Supply chain disruptions or price fluctuations in raw materials could potentially alter production and increase costs for manufacturers; lack of high-quality raw materials could cause quality variation across batches, which compromises overall disc performance and hinders growth in regions with limited access to supplies of quality raw materials, which could threaten growth in regions where raw material acquisition poses difficulties.
Opportunities in the Ceramic Flap Disc Market
Rising Demand for Automation in Manufacturing
The rising trend of automation and robotics use across industries like metal fabrication, automotive, and aerospace offers ceramic flap disc manufacturers an incredible opportunity. Automated systems require high-performance abrasives such as ceramic flap discs to perform grinding, polishing, and finishing functions, which ceramic flap discs excel at performing. As more factories and manufacturing plants adopt automated processes, demand will only increase further for efficient yet durable abrasive tools which create opportunities to grow market share as well as develop innovative solutions tailored specifically towards automated systems.
Expansion in Emerging Markets
As emerging economies such as India, China, and Southeast Asia become industrialized and build infrastructure, demand for high-quality abrasives in construction, automotive, and metalworking fields increases significantly. Ceramic flap disc manufacturers can capitalize on this burgeoning manufacturing activity in these regions by offering cost-effective solutions while expanding local production facilities tapping into high-growth markets and meeting rising demands for durable, high-performance products that last.
Trends in the Ceramic Flap Disc Market
Shift to Eco-Friendly and Sustainable Materials
Ceramic flap disc manufacturers have increasingly focused on eco-friendly and sustainable manufacturing practices to reduce the environmental impact of their products by using recycled materials, and greener production methods that aim to minimize waste and energy usage during production. As industries become more environmentally conscious, there is increased demand for eco-abrasives which contribute towards sustainability goals, offering manufacturers opportunities to innovate while meeting rising preferences for green products in the market.
Integration of Advanced Coatings and Technology
The ceramic flap disc market has seen an increased use of innovative coatings and abrasive technologies that improve performance, including advanced coatings to increase durability, heat resistance, cutting efficiency and tool life span; leading to longer-term tools with faster material removal rates and shorter tool lifespan. As industries demand higher productivity and precision from their tools, manufacturers are turning towards technologies such as ceramic grain coatings and multi-layered abrasives in order to meet them - this trend propels ceramic flap disc market innovation by providing better performance at reduced cost for industrial applications.
Research Scope and Analysis
By Diameter
The 4 to 8-inch diameter segment is expected to play a critical role in driving market growth and is set to have a leading market share in 2025, due to its versatility and wide industrial application. These medium-sized discs are an ideal combination of efficiency and control for use in metal fabrication, welding, and automotive applications. Grinding wheels are important tools in industries like construction, shipbuilding, and aerospace for grinding, deburring and surface finishing operations.
Their size allows workers to cover larger surfaces more quickly while still maintaining precision while increasing productivity. As industries demand durable and high-performance abrasives for use in industry applications, this segment continues to experience tremendous growth. Driven by automation and advanced manufacturing techniques, 4 to 8-inch ceramic flap discs are expected to see even further demand in coming years.
Further, ceramic flap discs in diameters over 8 inches have become a crucial component of heavy-duty industrial applications in the coming years, particularly for applications beyond 8 inches in diameter. These larger discs are often employed in shipbuilding, steel manufacturing, and large-scale metal fabrication, where high material removal rates and efficiency are key factors. Their larger size enables faster grinding and finishing operations on large surfaces, reducing labor time while increasing productivity.
Industries needing high-performance abrasives for rough grinding and smoothing large welds often opt for these discs because of their durability and heat resistance. As demand for stronger and longer-lasting abrasives in large-scale manufacturing and infrastructure projects increases, this segment should expand. Furthermore, with automated metalworking processes becoming more widespread within industry settings, ceramic flap discs that exceed 8 inches may become even more necessary.
By Grit Size
In 2025, medium grit size discs will play an integral part in driving the growth of the ceramic flap disc market as they offer an ideal combination of material removal and surface finish. These P60 to P120 grit discs are widely used for metal fabrication, automotive repair, and general-purpose grinding applications. They're ideal for smoothing rough edges, blending weld seams, and prepping surfaces for painting or coating, making them indispensable tools in industries like construction, shipbuilding, and machinery manufacturing. Medium-grit ceramic flap discs provide efficient cutting action while maintaining precision, removing the need for additional finishing steps.
As industries demand high-performance abrasives that increase productivity and durability, medium-grit ceramic flap discs continue to gain in popularity and support market expansion and technological advances. Further, Fine grit ceramic flap discs play an integral part in the ceramic flap disc market and are expected to have significant growth during the forecasted period by providing smooth finishing and precision work.
Commonly found at P150 or higher grit levels, fine-grit discs are frequently used in industries like automotive, aerospace, and stainless steel fabrication to polish, deburr, and finish surfaces; perfect for painting, coating, or welding prep applications. Due to their efficiency in providing superior finishes with minimal material removal required, their popularity increases as industries look for aesthetic enhancement, durability improvement, and increased performance from their metalworking applications.
By End User Vertical
Metal fabrication industries are among the primary drivers of growth for the ceramic flap disc market and are anticipated to dominate the market in 2025, due to high demands for cutting, grinding, and surface finishing applications. These discs are indispensable in welding, structural steelwork, and sheet metal processing; they help remove burrs, smooth welds and prepare surfaces for painting or coating. Ceramic flap discs have become an indispensable component in industries like automotive, aerospace, shipbuilding, and construction due to their superior durability, heat resistance, and long-term performance. Ceramic flap discs' ability to handle high-pressure applications while maintaining precision makes them an appealing alternative to traditional abrasives.
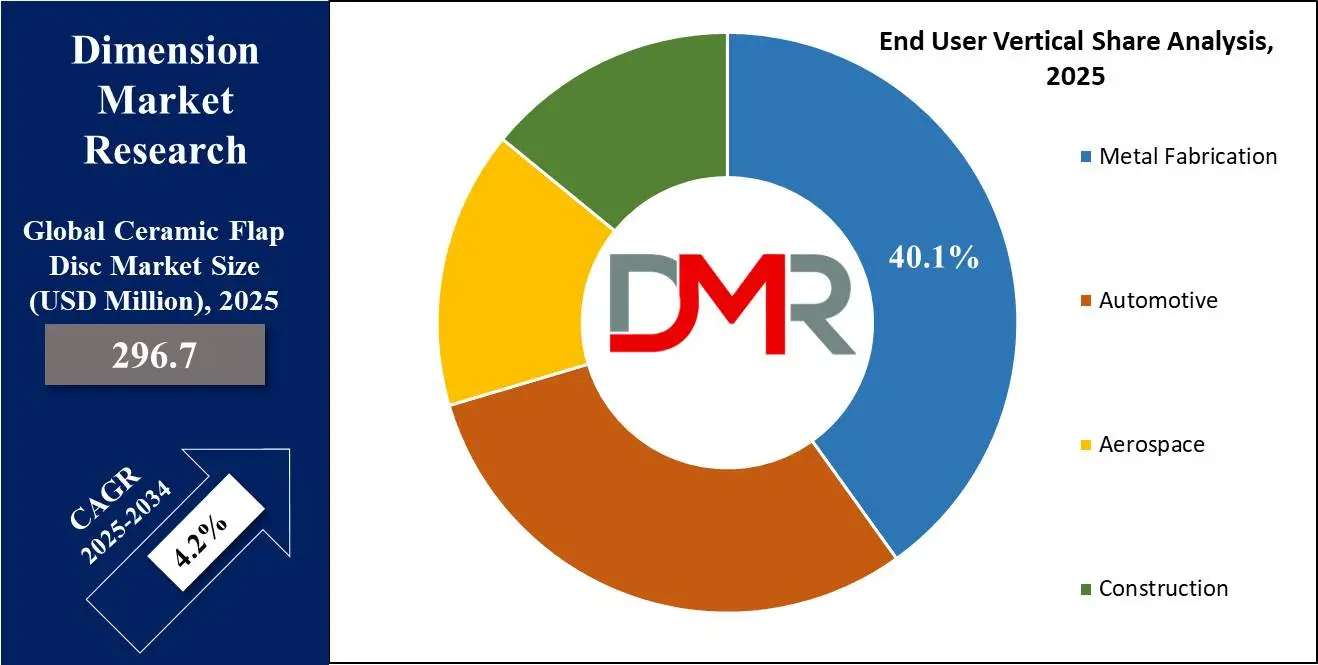
As automation & advanced manufacturing techniques continue to advance, the need for efficient grinding tools continues to increase. Furthermore, the demand for lightweight, corrosion-resistant metals in various industries further propels their adoption, solidifying metal fabrication as an invaluable contributor to market expansion.
In addition, the construction sector also plays an integral role in driving the growth of the ceramic flap disc market during the forecast period, as these discs are mainly used for grinding, cutting, and surface preparation of metal and concrete structures. Their wide use also includes smoothing welds, shaping metal beams, and finishing surfaces on projects like bridges, buildings, and infrastructure development, along with smoothing welds on weld seams, smoothing weld seams on bridges and shaping metal beams for projects like bridges buildings and infrastructure development projects. Their durability, heat resistance, and efficiency make them ideal for heavy-duty applications, while their wide use also ensures market expansion worldwide driving market growth forward.
The Ceramic Flap Disc Market Report is segmented on the basis of the following
By Diameter
- Less than 4 Inch.
- 4 to 8 Inches
- Above 8 Inches
By Grit Size
By End User Vertical
- Material Fabrication
- Automotive
- Aerospace
- Construction
Regional Analysis
Asia Pacific is expected to lead the ceramic flap disc market in 2025 with an anticipated
share of 37.8% due to rapid industrialization, advanced construction sector growth, and expanding metal fabrication industry. Countries like China, India, Japan, and South Korea experience high demands for abrasives across various industries like automotive manufacturing, shipbuilding, and infrastructure development. Their large manufacturing bases & increasing investments in smart cities and industrial projects help in the expansion of market growth. Automation & advanced metalworking techniques have increased demand for durable and high-performing grinding tools, with Asia Pacific emerging as an attractive market due to the availability of low-cost raw materials and labor. Furthermore, Asia Pacific remains a crucial producer and exporter of ceramic flap discs, thus continuing to establish itself as an increasingly prominent producer and market for such discs in coming years.
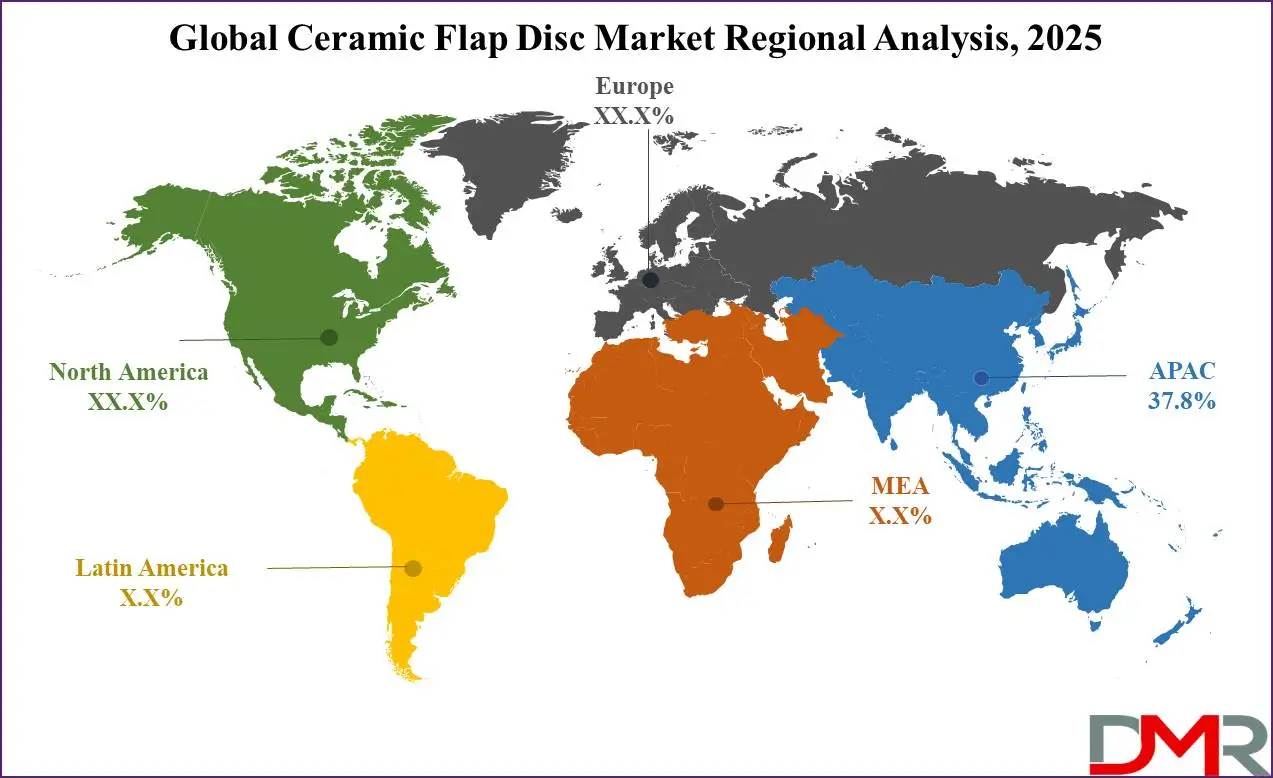
Also, North America plays an important role in driving the growth of the ceramic flap disc market, owing to industries like automotive production, aerospace engineering, metal fabrication, and construction. The need for high-quality and long-wearing abrasives used in welding, surface finishing, and metal grinding applications is growing. Both the U.S. and Canada, known for their advanced manufacturing capabilities, are major users of ceramic flap discs used for heavy industrial processes. North America's commitment to innovation, automation, and infrastructure development fuels the demand for efficient yet long-lasting grinding tools. As investments in high-performance equipment and technologies increase in North America, the ceramic flap disc market should experience exponential expansion supporting its continued growth within North America.
By Region
North America
Europe
- Germany
- The U.K.
- France
- Italy
- Russia
- Spain
- Benelux
- Nordic
- Rest of Europe
Asia-Pacific
- China
- Japan
- South Korea
- India
- ANZ
- ASEAN
- Rest of Asia-Pacific
Latin America
- Brazil
- Mexico
- Argentina
- Colombia
- Rest of Latin America
Middle East & Africa
- Saudi Arabia
- UAE
- South Africa
- Israel
- Egypt
- Rest of MEA
Competitive Landscape
The ceramic flap disc market is highly competitive, with numerous global and regional players com to meet the growing demand for high-performance abrasives. Manufacturers are focusing on product innovation, such as advanced coatings and improved durability, to differentiate themselves in the market. Companies are also expanding their production capabilities to cater to industries like metal fabrication, automotive, and construction. Price sensitivity remains a challenge, especially with lower-cost alternatives. As the demand for eco-friendly and sustainable products rises, companies are investing in green manufacturing practices to stay competitive and capture market share.
Some of the prominent players in the Global Ceramic Flap Disc are
- 3M Company
- Saint-Gobain Abrasives
- DEWALT
- Mirka Ltd
- Norton Abrasives
- ARC Abrasives
- Standard Abrasives
- Saint-Gobain Abrasives
- Metabo Corporation
- Pferd Inc
- Other Key Players
Recent Developments
- In January 2025, Weldcote launched its line of Z-Cotton zirconia flap discs with a flexible cotton backing suitable for fine finishing work on detailed contours. Designed for applications on carbon-based steels and stainless steel that require high conformability and a softer feel, the discs are constructed of zirconia aluminum oxide grains.
- In January 2025, Weiler Abrasives introduced a new lineup of non-woven cleaning and stripping products designed to remove coatings and rust in preparation for welding and manufacturing operations. New Tiger Ceramic and Tiger Silicon Carbide non-woven strip discs deliver superior cleaning power and extended product life for applications in metal fabrication, shipbuilding, automotive, and other industries.
- In July 2024, MSC Industrial Supply acquired ApTex Inc. and Premier Tool Grinding Inc. as the purchase agreements, both companies will continue to operate under their current names as MSC companies. Combined, the two companies had estimated revenues of slightly over USD 20 million in 2023 and have 58 associates. Both acquisitions are expected to be net neutral to MSC's fiscal year 2024 net income.
- In April 2024, Henan DOMILL Abrasive Technology Co., Ltd and Qingdao ROY Material Technology Co., Ltd. held the signing ceremony of a strategic cooperation agreement on ceramic corundum abrasive in DOMILL Factory. In the future, the two parties will conduct in-depth cooperation on the ceramic corundum market collaboration, application and post-processing technology in terms.