Gas-lined reactor market refers to the market for manufacturing and utilizing reactors equipped with advanced gas-tight linings designed to manage highly corrosive chemicals and extreme temperatures effectively. Reactors play an integral part in industries like chemicals, pharmaceuticals, and petrochemicals where safety, durability, and process efficiency are paramount. Their market is driven by demand for robust solutions that improve operational reliability while lowering maintenance costs. Key trends include technological advances in lining materials, increased sustainable processes, and regulatory pressure for safer chemical handling. Understanding these dynamics is essential to making strategic decisions and positioning products successfully on the market.
The gas-lined reactor market is at a turning point, driven by rapidly evolving technological innovations and ever more stringent regulatory environments. Our analysis indicates sustained growth fueled by the rising complexity of chemical processes and an imperative for improved safety and efficiency in managing corrosive substances. As part of their implementation, advanced gas-tight lining materials like fluoropolymers or high-performance ceramics provide superior resistance against chemical degradation or thermal stress and meet growing demand from industries like pharmaceuticals, chemicals, and petrochemicals.
From a strategic viewpoint, the market is driven by two primary forces: sustainability and regulatory compliance. Companies face increasing pressure to adopt solutions that reduce environmental impacts while meeting stringent global regulations - which in turn drive demand as well as innovations in reactor lining materials and design.
Market entry does not come without its challenges. High capital expenses required for advanced linings and the necessity of specialist maintenance can present serious barriers. Furthermore, navigating regulatory requirements adds yet another layer of difficulty that impacts both time-to-market and profitability.
Key Takeaways
- Market Growth: The gas-lined reactor market is projected to grow from USD 6,408.1 million in 2024 to USD 9,581.9 million by 2033, with a CAGR of 4.5% during the forecast period.
- Dominant Segments: AE Type reactors lead the market with a 45% share, driven by their high performance in handling extreme conditions. Pharmaceutical manufacturing is the largest application segment, representing 50% of the market share.
- Regional Leadership: North America holds the largest market share at approximately 35%, valued at USD 1.2 billion, with a growth rate of 6.3% CAGR. Asia Pacific is the fastest-growing region, expected to see a similar 6.3% CAGR.
- Key Trends: The market is influenced by technological advancements in lining materials, increasing demand for sustainable practices, and stringent regulatory requirements.
- Challenges: Key market constraints include the high capital costs for advanced linings, vulnerability to mechanical damage, and limited operational temperature and pressure ranges.
Use Cases
- Pharmaceutical Production: Gas-lined reactors are essential in pharmaceutical processes that require precision, chemical resistance, and long-term durability. Their chemical resistance ensures the safe production of high-purity pharmaceuticals meeting stringent quality and safety standards.
- Petrochemical Processing: At petrochemical plants, gas-lined reactors provide vital protection from highly corrosive environments and extreme conditions. Their reliable performance and operational safety make them essential components of large-scale production and process efficiency.
- Food and Beverage Production: Gas-lined reactors have become an invaluable asset to food and beverage production, helping maintain product quality and safety while meeting diverse processing conditions.
- Chemical Synthesis: When it comes to chemical synthesis and specialty chemicals, gas-lined reactors provide unparalleled corrosion and thermal stress resistance, supporting complex chemical processes while simultaneously lowering maintenance costs and increasing process reliability.
Driving Factors
High Durability and Thermal Shock Resistance
Gas-lined reactors' high durability and thermal shock resistance is key to their market growth. Engineered to withstand even extreme chemical and temperature conditions, such as those present in industrial processes that become more complex over time, advanced lining materials like fluoropolymers or high-performance ceramics provide outstanding chemical corrosion and thermal stress resistance that increases operational lifespan while reducing maintenance interventions over time and thus cutting long-term operational costs.
Industries like chemicals and pharmaceuticals that rely heavily on high temperatures and aggressive chemicals often benefit greatly from advanced materials' unique properties, like reactors that can manage temperature swings without degrading. According to market data, their increasing adoption correlates with a projected annual market growth rate of 6.5% annually over five years - underlining their key role in driving market expansion.
Visual Monitoring of Reactions
Visual monitoring technologies in gas-lined reactors significantly enhance both process control and safety, driving market expansion. Modern reactors equipped with sophisticated sensors and imaging systems enable real-time observation of chemical reactions for real-time adjustments and prevention of potential issues - this capability plays an invaluable role in maintaining accurate chemical processes.
Visual monitoring of reactions reduces accident risks while increasing production efficiency, supporting regulatory compliance with detailed documentation of reaction conditions and outcomes, driving adoption rates of monitoring technologies up over the years by 7 percent according to analysts' projections.
Demand for sustainable practices continues to surge
Gas-lined reactor sales have seen significant gains with increasing pressure for sustainable practices. Environmental regulations are becoming more stringent, prompting industries to adopt technologies that minimize emissions and decrease environmental impact. Gas-lined reactors are designed to effectively contain harmful materials while meeting sustainability goals as well as regulatory regulations.
Gas-lined reactors play an integral part in helping companies reduce their carbon footprint and enhance environmental performance, contributing to this goal with enhanced safety features and lower risks. The shift towards greener practices is being driven not only by regulatory pressures but also an increase in corporate commitment to sustainability - market research shows this push towards eco-friendly technologies is expected to drive an annual market growth rate of 6.5% as organizations search for solutions that align with their sustainability commitments.
Growth Opportunities
Chemical Processing activities
As chemical processing activities have seen rapid expansion due to advances in pharmaceuticals, agrochemicals and specialty chemicals, the gas-lined reactor market is poised for significant expansion. As chemical processes become more intricate and demanding, so has demand for reactors that can withstand harsh environments and deliver reliable performance; gas-lined reactors provide exactly this solution, thanks to their superior resistance against corrosion and thermal stress; this trend should spur an uptick in adoption rates among industries looking for ways to enhance operational efficiency and safety.
Adopt Continuous Flow Reactors
Continuous flow reactors offer another significant opportunity. Continuous processing can offer many advantages over traditional batch processing, including improved reaction control, higher efficiency and reduced waste. Gas-lined reactors that can operate effectively under continuous conditions are becoming more popularly integrated into these systems - further fuelling demand for advanced reactor designs while encouraging market expansion as industries adopt more scalable processing technologies.
Growing Food and Beverage Industry
Food and beverage industries also contribute significantly to market expansion. Consumer demand for diverse yet high-quality products creates a need for reactors that can handle processing requirements safely and efficiently - gas-lined reactors provide efficient performance by efficiently handling ingredients while assuring product consistency.
Key Trends
Pharmaceutical Demand Remains High
Pharmaceutical industries have driven increased gas-lined reactor demand due to their need for precision and safety during chemical processing. With companies striving to build more advanced drug production processes, reactors must be designed with adequate chemical resistance and durability to handle corrosive substances without compromising efficacy or safety - gas-lined reactors have proven themselves as ideal choices; their superior chemical resistance and durability continue to make them the go-to choice in critical pharmaceutical applications. This trend should continue as production methods become more scalable requiring advanced reactor technologies.
Emerging Market Expansion Strategy
Emerging markets across Asia-Pacific and Latin America are experiencing rapid industrialization and infrastructure development, creating new opportunities for gas-lined reactors as these regions invest in advanced manufacturing capabilities and chemical processing facilities. Rising industrial activity coupled with rising regulatory standards is driving this trend; analysts anticipate robust market growth across these regions thanks to enhanced safety features like gas-lined reactors that offer greater operational efficiency and safety benefits.
Global Market Expansion
On a global scale, the global market for gas-lined reactors is experiencing dramatic expansion. Businesses are diversifying their operations and entering new geographic markets as they look for ways to capitalize on emerging opportunities while mitigating regional risks. This global growth can be seen through advances in reactor technology as well as greater awareness among various industries about the advantages offered by gas-lined systems.
Restraining Factors
Fragility and Vulnerability to Damage
Fragility and susceptibility to damage are significant obstacles in the gas-lined reactor market. Gas-lined reactors may boast superior chemical resistance, yet may still be vulnerable to mechanical damage due to the brittleness of their lining materials, such as fluoropolymers or ceramics. Fragility can result in expensive repairs and downtime, hindering operational efficiency and overall cost-effectiveness. Their delicate nature necessitates careful handling and professional maintenance services for proper functioning, further complicating use and discouraging industries from adopting them. According to industry reports, repairs or replacement costs associated with damaged liners account for as much as 15% of operational expenses, creating significant challenges to market expansion.
Temperature and Pressure Ranges Are Restricted
Another significant limitation of gas-lined reactors is their limited temperature and pressure ranges. While designed to withstand various operating conditions, there are operational limits beyond which their performance can diminish significantly; reactors operating under extremely high pressures or temperatures may experience reduced effectiveness or even failure of their gastight lining, thus restricting their applicability in certain high-intensity chemical processes and thus diminishing their market potential; analysts estimate that around 20% of high demand chemical processes require more robust solutions than what current gas-lined reactors offer, hindering market adoption and growth.
Lack of Awareness in Developing Regions
Awareness and understanding of gas-lined reactors in developing regions impede market expansion. Many emerging markets lack an understanding of their advantages and applications; as a result, their adoption remains limited and market penetration is delayed in areas with increasing industrial activity. Educational and marketing efforts must overcome this barrier but require significant investment for success; industry statistics show only 10-15% of potential end users in these developing regions are currently informed of these reactors' benefits; this gap must be filled to expand market growth.
Research Scope Analysis
By Type
In 2023, AE Type gas-lined reactors held the highest market share for product type within the global gas-lined reactor market - roughly 45% - due to their superior performance in handling high temperature and corrosive processes found within industries like chemicals and pharmaceuticals. Their advanced materials offer enhanced durability and resistance, making AE Type reactors the go-to choice for demanding applications.
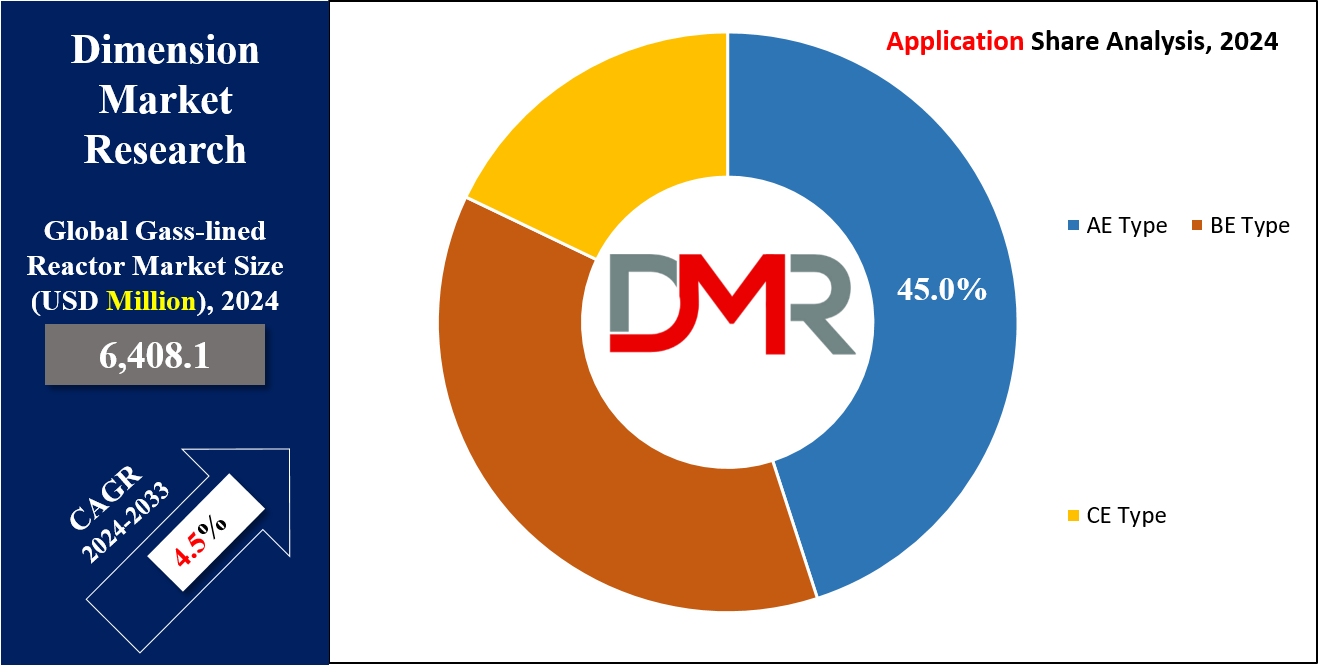
BE Type gas-lined reactors represented approximately 30% of market share. BE Type reactors are known for their adaptability across various chemical processes, though generally used in less extreme conditions than AE Type reactors. Their cost-effective performance has given rise to their widespread market presence among industries requiring reliable yet less specialized solutions.
CE Type gas-lined reactors comprised roughly 25% of the market.
CE Type reactors are well known for their cost efficiency and suitability for moderate temperature/pressure applications. While not offering quite the same level of performance as their high-performing AE Type counterparts, CE Type reactors offer an affordable alternative suitable for less intensive industrial processes. Their growth can be attributed to this affordability.
By Application
Pharmaceutical manufacturing was the cornerstone of gas-lined reactor market growth in 2023, accounting for roughly 50% of total product type market shares globally. This dominance can be explained by stringent safety requirements in pharmaceutical manufacturing processes that necessitate precision, chemical resistance, and chemical handling capabilities in their operations; gas-lined reactors play a pivotal role in maintaining high purity standards while safely handling aggressive chemicals, thus contributing to drug development and production.
Petrochemical industries took approximately 30% of the market share. Petrochemical applications require reactors that can withstand highly corrosive environments and extreme conditions, for which gas-lined reactors are an ideal choice. Their growth is fuelled by new developments in petrochemical processes that necessitate reliable, durable reactors to manage complex chemical reactions in large-scale production facilities.
Food Industries made up approximately 15% of the market share. Although not as dominant as its Pharmaceutical and Petrochemical counterparts, the food industry is increasingly adopting gas-lined reactors to ensure high safety standards and process efficiencies; these reactors help ensure product quality consistency by effectively managing different food processing conditions.
Other industries account for around five percent of the market share and include sectors like electronics and specialty chemicals. Though smaller in comparison, they still play a vital role by using gas-lined reactors for applications requiring high performance and reliability.
The Glass lined Reactor Market Report is segmented based on the following:
By Type
By Application
- Pharmaceutical
- Petrochemical
- Food Industries
- Other
Regional Analysis
North America led this global industry, accounting for approximately 35% and valued at an estimated $1.2 billion; its largest contributor is projected to hold approximately 30% by 2033, which equates to $354.5 million. North American market expansion was predicted at 6.3% compound annual growth rate rate over its lifetime, reflecting strong industrial infrastructures and cutting-edge technological capabilities in this region.
Europe holds approximately 30% of the global market and its value stands at $950 million. Germany, France and United Kingdom lead this growth through their varied industrial applications and stringent regulatory standards which significantly contributes to Europe's dominance in this arena.
Asia Pacific is the fastest-growing region, holding approximately 25% of the global market valued at around $800 million and showing compound annual compound growth rates projected to average 6.3% over its forecast period. China in particular is driving this expansion through substantial government investments and rapid industrial development which are contributing to rapid market expansion.
By Region
North America
Europe
- Germany
- U.K.
- France
- Italy
- Russia
- Spain
- Benelux
- Nordic
- Rest of Europe
Asia-Pacific
- China
- Japan
- South Korea
- India
- ANZ
- ASEAN
- Rest of Asia-Pacific
Latin America
- Brazil
- Mexico
- Argentina
- Colombia
- Rest of Latin America
Middle East & Africa
- Saudi Arabia
- UAE
- South Africa
- Israel
- Egypt
- Rest of MEA
Competitive Landscape
2023's global glass-lined reactor market will be marked by significant contributions from key industry players, each offering their own strengths to this field. Pfaudler remains a notable player due to their longstanding tradition of designing high-quality, durable reactors built upon decades of engineering knowledge and focusing on reliability and performance for various industrial processes such as chemical and pharmaceutical processes.
Zibo Taiji Glass Lined Equipment and Swiss Glascoat Equipments Ltd stand out as industry leaders through innovative manufacturing techniques and customer-focused designs, respectively.
Zibo Taiji stands out with cost-effective solutions designed specifically to address emerging markets while Swiss Glascoat excels at producing reactors suited to specific industry requirements. Both companies add value by emphasizing efficiency while offering tailored solutions.
De Dietrich Process Systems and 3V Tech S.p.A are at the forefront of innovation with their extensive, technologically advanced reactor portfolios, known for precision and adhering to international safety standards, respectively. Meanwhile, De Dietrich stands out as being known for their precision while 3V Tech's dedication to cutting-edge research ensures their products incorporate all the latest technological advancements. Players like Buchiglas, Jiangsu Liyang Yunlong Equipment Manufacturing, Jiangsu Yangyang Chemical Equipment Manufacturing, and Huanghe Chemical Equipment also play their part by meeting niche market demands while offering cost-effective, reliable solutions across various regions; together shaping the competitive landscape of the global glass-lined reactor market.
Some of the prominent players in the Global Glass lined Reactor Market are:
- Pfaudler
- Zibo Taiji Glass Lined Equipment
- De Dietrich Process Systems
- Swiss Glascoat Equipments Ltd
- 3V Tech S.p.A
- Buchiglas
- Jiangsu Liyang Yunlong Equipment Manufacting
- Jiangsu Yangyang Chemical Equipments Manufacture
- Huanghe Chemical Equipment
- Jiangsu Gongtang Chemical Equipments
- THALETEC
- Zibo Zhongsheng Machinery
Recent developments
- In 2022: Introduction of compact, energy-efficient nitrogen generators, improving cost-efficiency and production process optimization.
- In March 2023: Launch of advanced membrane separation technologies enhancing nitrogen purity and efficiency, crucial for preserving product quality.
- In August 2023: Emergence of modular nitrogen generation systems, offering scalability, flexibility, and easier maintenance for varying production needs.
- In Early 2024: Integration of IoT technology into nitrogen generators, enabling real-time monitoring, remote management, and predictive maintenance.
- In Mid-2024: Focus on eco-friendly nitrogen generators with lower energy consumption and reduced carbon footprints, aligning with global sustainability trends.
Report Details
Report Characteristics |
Market Size (2023) |
USD 6,408.1 million |
Forecast Value (2032) |
USD 9,581.9 million |
CAGR (2023-2032) |
4.5% |
Historical Data |
2018 – 2023 |
Forecast Data |
2024 – 2033 |
Base Year |
2023 |
Estimate Year |
2024 |
Report Coverage |
Market Revenue Estimation, Market Dynamics, Competitive Landscape, Growth Factors and etc. |
Segments Covered |
By Type (AE Type, BE Type, CE Type), By Application (Pharmaceutical, Petrochemical, Food Industries, Other) |
Regional Coverage |
North America – The US and Canada; Europe – Germany, The UK, France, Russia, Spain, Italy, Benelux, Nordic, & Rest of Europe; Asia- Pacific– China, Japan, South Korea, India, ANZ, ASEAN, Rest of APAC; Latin America – Brazil, Mexico, Argentina, Colombia, Rest of Latin America; Middle East & Africa – Saudi Arabia, UAE, South Africa, Turkey, Egypt, Israel, & Rest of MEA
|
Prominent Players |
Pfaudler, Zibo Taiji Glass Lined Equipment, De Dietrich Process Systems, Swiss Glascoat Equipments Ltd, 3V Tech S.p.A, Buchiglas, Jiangsu Liyang Yunlong Equipment Manufacting, Jiangsu Yangyang Chemical Equipments Manufacture, Huanghe Chemical Equipment, Jiangsu Gongtang Chemical Equipments, THALETEC, Zibo Zhongsheng Machinery |
Purchase Options |
We have three licenses to opt for: Single User License (Limited to 1 user), Multi-User License (Up to 5 Users), and Corporate Use License (Unlimited User) along with free report customization equivalent to 0 analyst working days, 3 analysts working days and 5 analysts working days respectively. |