Market Overview
The Global Industrial Robotics Market is estimated to be valued at
USD 18.6 billion in 2025 and is further anticipated to reach
USD 51.4 billion by 2034 at a
CAGR of 11.9%.
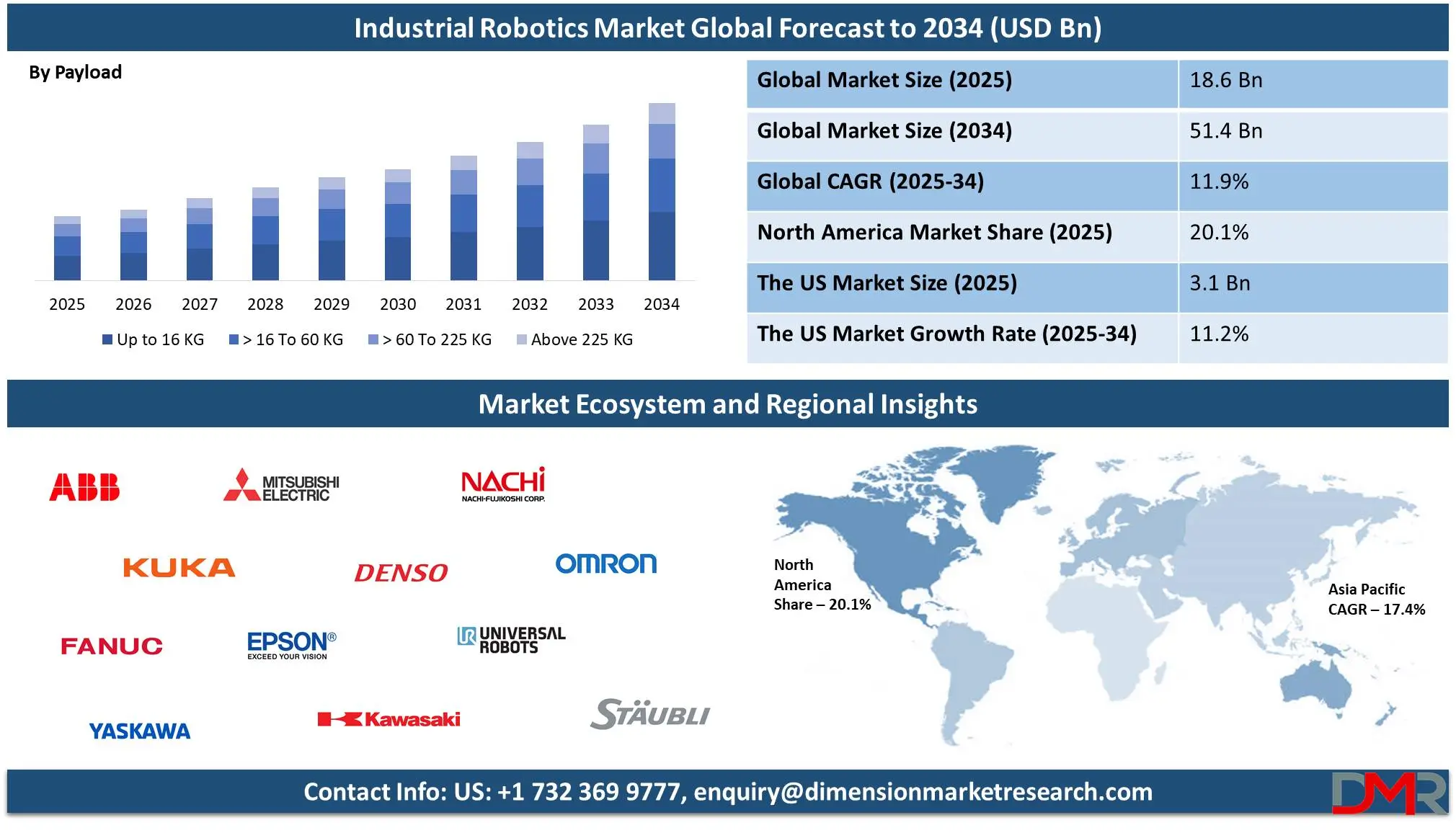
Industrial robotics refers to the branch of automation that involves designing, developing, and deploying programmable robotic systems to execute various manufacturing tasks with high efficiency and precision. These robots are commonly utilized in environments such as automotive assembly lines, electronics manufacturing, and food packaging plants, where repetitive tasks, heavy lifting, or hazardous conditions make manual labor less practical or safe.
Equipped with actuators, sensors, and advanced control algorithms, industrial robots can perform a wide array of functions, including welding, painting, assembling, picking and placing, and quality inspection. Their ability to operate continuously, minimize human error, and enhance productivity has made them a cornerstone of modern industrial processes.
The global industrial robotics market is experiencing rapid growth, fueled by a combination of labor shortages, demand for higher production efficiency, and the increasing complexity of manufacturing operations. As companies strive to remain competitive in a globalized economy, the adoption of robotics has become a key strategy for scaling operations without proportionately increasing costs. Emerging markets are also playing a significant role in this expansion, as manufacturers invest in automation to meet global quality standards and reduce dependence on manual labor.
Technological advancements have significantly reshaped the capabilities of industrial robots, making them smarter, more adaptable, and easier to integrate into existing workflows. The incorporation of artificial intelligence, machine learning, and advanced vision systems allows robots to perform tasks that previously required human dexterity and judgment. This evolution has expanded their use beyond traditional sectors like automotive and electronics into newer industries such as logistics, healthcare, and renewable energy, where customized and flexible automation solutions are in demand.
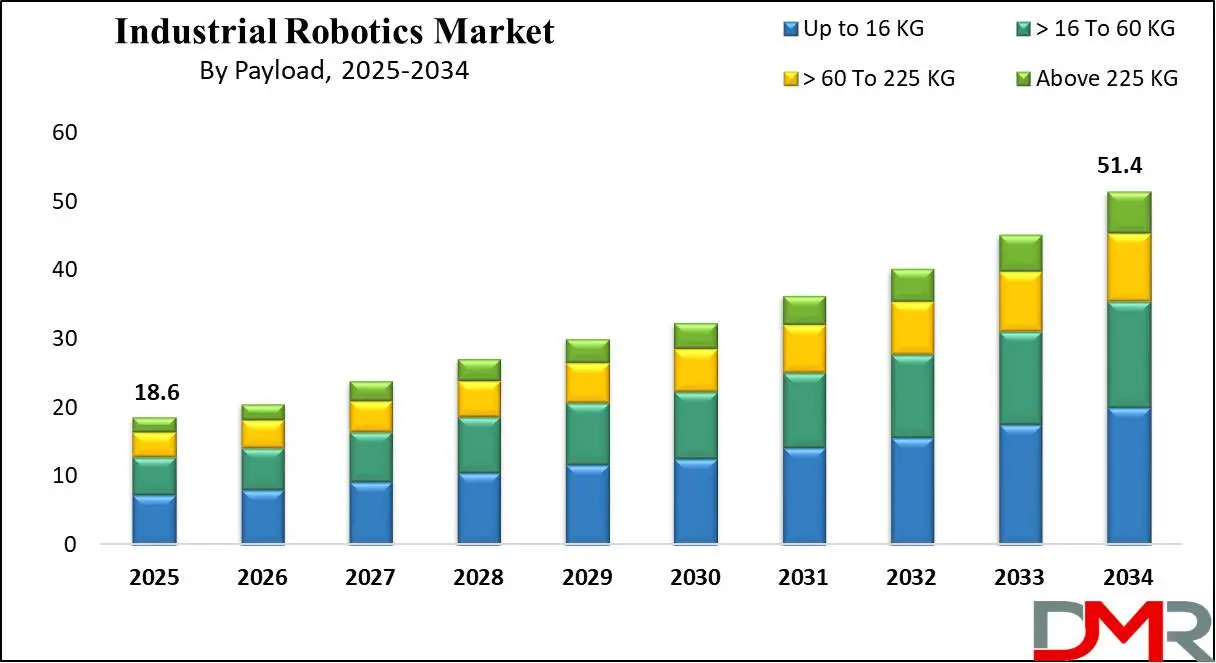
The market landscape is also being influenced by the growing popularity of collaborative robots, or cobots, which are designed to work safely alongside human operators. Unlike traditional robots that require isolated environments, cobots are equipped with safety features and user-friendly interfaces that allow for close interaction. Their rising adoption, especially among small and medium-sized enterprises, reflects a broader trend toward accessible and scalable automation. Furthermore, favorable government policies, investments in smart manufacturing, and a strong focus on industrial modernization are expected to sustain the market’s momentum in the years to come.
The US Industrial Robotics Market
The U.S. Industrial Robotics Market is projected to be valued at USD 3.1 billion in 2025. It is further expected to witness subsequent growth in the upcoming period, holding USD 8.2 billion in 2034 at a CAGR of 11.2%.
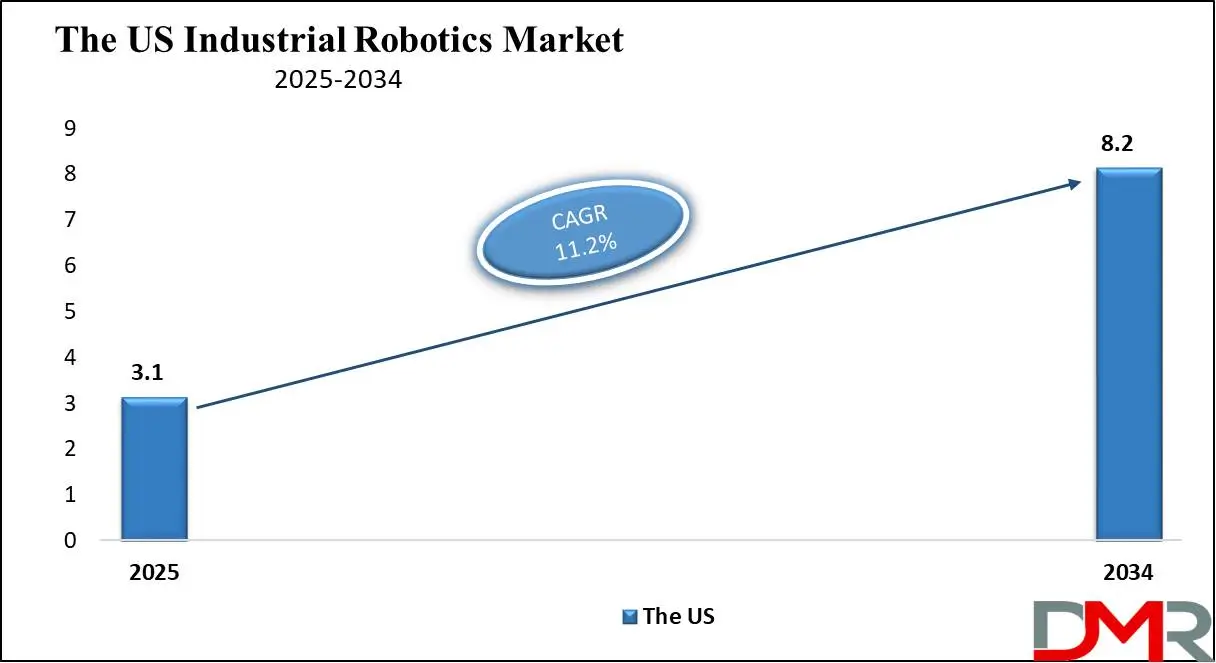
Industrial robotics in the U.S. has become a critical component of the country’s advanced manufacturing ecosystem, playing a key role in driving productivity, precision, and competitiveness. With a strong presence in industries such as automotive, aerospace, electronics, and pharmaceuticals, U.S. manufacturers are relying on robotic automation to maintain high-quality standards and optimize output.
American industrial robotics also benefits from a robust innovation infrastructure, supported by world-class research institutions, government-backed initiatives, and collaboration between technology developers and manufacturers. The integration of robotics has helped companies in the U.S. mitigate the effects of labor shortages, rising wages, and global supply chain disruptions by creating more resilient, localized production capabilities.
The U.S. industrial robotics market is among the largest in the world, driven by a high demand for automation and the early adoption of cutting-edge technologies. According to industry estimates, the country consistently ranks as one of the top consumers of industrial robots globally, with installations largely concentrated in automotive and electronics manufacturing.
However, recent trends show an increasing deployment of robots in non-traditional sectors such as food and beverage, logistics, and life sciences, reflecting a broader shift toward diversification of automation. Additionally, the expansion of e-commerce has fueled the demand for robotics in warehousing and distribution centers, where speed, accuracy, and operational efficiency are paramount.
Global Industrial Robotics Market: Key Takeaways
- Market Value: The global industrial robotics market size is expected to reach a value of USD 51.4 billion by 2034 from a base value of USD 18.6 billion in 2025 at a CAGR of 11.9%.
- By Type Segment Analysis: Traditional Robots are poised to consolidate their dominance in the type segment, capturing 88.4% of the total market share in 2025.
- By Payload Type Segment Analysis: Up to 16 kg payload type is anticipated to maintain its dominance in the payload type segment, capturing 38.9% of the total market share in 2025.
- By Offering Segment Analysis: Industrial Robots are poised to consolidate their market position in the offering type segment, capturing 57.3% of the total market share in 2025.
- By Application Segment Analysis: Handling applications are expected to maintain their dominance in the application segment, capturing 37.5% of the total market share in 2025.
- By End-Use Type Segment Analysis: The Automotive industry is expected to maintain its dominance in the end-use type segment, capturing 31.3% of the total market share in 2025.
- Regional Analysis: Asia Pacific is anticipated to lead the global industrial robotics market landscape with 66.4% of total global market revenue in 2025.
- Key Players: Some key players in the global industrial robotics market are ABB, FANUC Corporation, Yaskawa Electric Corporation, KUKA AG, Mitsubishi Electric Corporation, Kawasaki Heavy Industries, Epson Robotics, Denso Corporation, Nachi-Fujikoshi Corp, Universal Robots, Omron Corporation, Staubli International AG, Comau S.p.A., Techman Robot Inc., Siasun Robot & Automation, Hyundai Robotics, Delta Electronics, Toshiba Machine Co., Ltd., IAI Corporation, Doosan Robotics, and Other Key Players.
Global Industrial Robotics Market: Use Cases
- Automated Welding in Automotive Assembly Lines: Automotive manufacturers like Toyota, BMW, and General Motors heavily rely on robotic welding systems for both spot and arc welding processes. These robots improve precision, reduce welding defects, and increase the speed of production lines. With multi-axis movement and vision systems, they can weld complex body structures with minimal human intervention.
- Precision Assembly in Electronics Manufacturing: Companies such as Foxconn and Samsung deploy SCARA and delta robots in the assembly of smartphones, circuit boards, and consumer electronics. These robots handle ultra-small components with sub-millimeter accuracy, performing tasks such as screw fastening, soldering, and PCB placement. Cleanroom-compatible models are used for chip fabrication and camera module assembly, ensuring contamination-free environments and boosting product reliability.
- Robotic Palletizing and Packaging in Food & Beverage: Food and beverage companies like Nestlé and PepsiCo utilize robotic arms for high-speed palletizing, sorting, and packaging. These robots can quickly adapt to varying package sizes and formats, optimizing end-of-line operations. Equipped with hygienic designs and washdown capabilities, they also meet food safety regulations.
- Sterile Material Handling in Pharmaceutical Production: Pharmaceutical giants such as Pfizer and Roche use cleanroom-classified robotic systems to handle sterile vials, syringes, and test kits. Robots manage tasks such as filling, capping, labelling, and inspecting medicinal products in highly controlled environments. By minimizing human contact, these systems significantly reduce the risk of contamination and help meet stringent regulatory standards such as GMP (Good Manufacturing Practices).
Global Industrial Robotics Market: Stats & Facts
- According to the International Federation of Robotics (IFR):
- As of the end of 2023, around 4.28 million industrial robots were operating worldwide.
- In 2022, global supply reached 553,052 industrial robots.
- The automotive industry holds about one-third of all installed industrial robots globally.
- China had the highest number of industrial robot installations in 2018, totaling 154,032 units.
- Robot density in India’s automotive sector reached 148 units per 10,000 employees in 2021.
- According to the Association for Advancing Automation (A3):
- In 2022, North American companies ordered 44,196 industrial robots, an 11% increase over 2021.
- According to the European Commission:
- The EU continues to lead in robotics adoption, driven by its Industry 4.0 initiatives to enhance manufacturing competitiveness.
- According to the U.S. Department of Labor:
- The U.S. manufacturing sector increasingly relies on industrial robotics to address skilled labor shortages and improve efficiency.
- According to the Japan Robot Association (JARA):
- Japan remains a leading producer and user of industrial robots, particularly in automotive and electronics manufacturing.
- According to the German Federal Ministry for Economic Affairs and Energy:
- Germany has integrated robotics heavily within its manufacturing sector under the "Industrie 4.0" framework.
- According to the South Korean Ministry of Trade, Industry and Energy:
- South Korea has the world’s highest robot density in manufacturing, with significant usage in the electronics and automotive sectors.
- According to the Chinese Ministry of Industry and Information Technology:
- China has made industrial automation a core part of its "Made in China 2025" strategy, driving massive investments in robotics.
- According to the U.K. Department for Business and Trade:
- The UK government supports robotics in advanced manufacturing to modernize its industrial base and stay globally competitive.
- According to the Canadian Ministry of Innovation, Science and Economic Development:
- Canada is scaling industrial automation to drive economic growth and reduce reliance on foreign supply chains.
- According to the Singapore Economic Development Board:
- Singapore is using robotics as part of its Smart Industry initiative to enhance productivity in precision engineering and electronics.
- According to the Indian Ministry of Heavy Industries:
- India is promoting robotics and automation through Production-Linked Incentive (PLI) schemes to boost domestic manufacturing.
- According to the UAE Ministry of Industry and Advanced Technology:
- The UAE has prioritized robotics within its Operation 300bn industrial strategy to diversify its economy.
- According to the Mexican Ministry of Economy:
- Mexico is expanding industrial robotics usage to strengthen its position in global automotive and electronics supply chains.
- According to the Indonesian Ministry of Industry:
- Indonesia is encouraging robotics adoption in its roadmap to become a top global manufacturing hub by 2030.
- According to the Turkish Ministry of Industry and Technology:
- Turkey aims to increase industrial automation to reduce import dependency and improve export competitiveness.
- According to the Brazilian Ministry of Science, Technology, and Innovation:
- Brazil is fostering robotics use in manufacturing to improve productivity and reduce industrial costs.
- According to the Russian Ministry of Industry and Trade:
- Russia is investing in domestic robotic technologies to modernize its industrial base and reduce foreign reliance.
- According to the Australian Department of Industry, Science and Resources:
- Australia is focusing on advanced robotics in mining, food processing, and logistics to tackle labor and efficiency challenges.
- According to the South African Department of Trade, Industry and Competition:
- South Africa has included industrial robotics in its industrial policy to support automation in the automotive and metals sectors.
Global Industrial Robotics Market: Market Dynamics
Global Industrial Robotics Market: Driving Factors
Rising Demand for Automation amid Global Labor Shortages
As the workforce ages in developed countries and younger generations shift away from factory-based careers, manufacturers are facing significant gaps in skilled and unskilled labor. At the same time, developing nations are experiencing rising labor costs and volatility in workforce availability, making long-term human resource planning more complex.
Industrial robots offer a sustainable solution by ensuring uninterrupted production with consistent quality and output. They're being adopted not just to replace human workers, but to fill essential gaps in repetitive, dangerous, or ergonomically challenging tasks that are difficult to staff. This labor-driven demand is pushing companies to accelerate investments in robotic automation, particularly in sectors like logistics, electronics, food processing, and metalworking, where high throughput and precision are critical.
Integration of AI, Vision Systems, and IoT in Robotics
These advancements are turning traditional industrial robots into intelligent, adaptive, and data-driven systems. AI-powered robots can now learn from patterns, adjust to new workflows, and make real-time decisions without reprogramming, which significantly boosts flexibility in dynamic manufacturing environments.
Vision systems allow robots to identify, inspect, and sort complex items with a level of nuance previously achievable only by humans. Meanwhile, IoT connectivity enables predictive maintenance, remote monitoring, and cloud-based performance analytics, reducing downtime and operational costs. These technological synergies are not only improving robot capabilities but are also redefining the ROI equation for businesses, making advanced robotics a viable investment even for small and medium enterprises.
Global Industrial Robotics Market: Restraints
High Initial Investment and Integration Complexity
Despite long-term cost savings, the upfront investment required for industrial robotics remains a significant barrier, especially for small and mid-sized enterprises (SMEs). Beyond the purchase of robots themselves, companies must invest in infrastructure upgrades, system integration, employee training, safety enclosures, and maintenance contracts.
For many manufacturers, particularly in emerging markets, this capital expenditure is hard to justify without guaranteed short-term ROI. Moreover, integration is not plug-and-play; aligning robots with legacy systems, customizing workflows, and programming for specific tasks requires time, technical expertise, and sometimes expensive third-party support.
Workforce Displacement Concerns and Resistance to Change
As robots take over repetitive and low-skill tasks, there is a genuine fear among workers about job losses, reduced career opportunities, and wage stagnation. This anxiety is often amplified by a lack of clear retraining pathways or upskilling initiatives, especially in regions where vocational education is underfunded.
Additionally, internal resistance from management or labor unions can slow down deployment, particularly in organizations with a long-standing reliance on manual labor. Companies must not only manage the technical shift but also invest in change management, communication, and workforce transition programs, without which adoption can face significant pushback and social friction.
Global Industrial Robotics Market: Opportunities
Expansion of Robotics in Non-Traditional Industries
While automotive and electronics have historically dominated industrial robotics, there's a growing opportunity in non-traditional sectors such as agriculture, construction, textiles, and waste management. These industries are now turning to automation to solve sector-specific challenges like labor shortages, safety risks, and efficiency gaps. For instance, robots are being deployed in agriculture for tasks like fruit picking, weeding, and crop monitoring, jobs that are seasonal, physically demanding, and labor-intensive.
In construction, autonomous robots are being used for bricklaying, 3D printing of structures, and inspection of hazardous sites. These industries represent largely untapped markets with unique needs, paving the way for specialized robotic solutions and driving diversified growth for manufacturers and integrators.
Rise of Modular, Scalable, and Subscription-Based Robotics
Rather than committing to heavy capital expenditure, companies, especially SMEs, can now adopt robots through subscription models that include hardware, software, maintenance, and analytics in a bundled monthly fee. This shift lowers entry barriers and allows for incremental scaling as business needs evolve.
Additionally, the development of modular robotic systems, where components like arms, sensors, or grippers can be swapped or upgraded, offers greater customization and lifecycle value. These innovations not only democratize access to automation but also unlock recurring revenue streams for vendors, signaling a shift from one-time sales to long-term robotic partnerships.
Global Industrial Robotics Market: Trends
Integration of Generative AI in Robotics
The incorporation of generative AI into industrial robotics is revolutionizing automation by enabling robots to adapt to complex, variable tasks with minimal human intervention. Startups like Chef Robotics are at the forefront, developing AI-powered robots capable of handling diverse food preparation tasks, such as assembling meals and packaging, by learning from vast datasets.
This advancement allows robots to operate in unstructured environments, making them suitable for industries like food processing, where variability is high. The adaptability and learning capabilities of generative AI-driven robots are expanding the scope of automation beyond repetitive tasks, facilitating their deployment in sectors previously considered too dynamic for traditional robotics.
Deployment of Humanoid Robots in Logistics
The logistics sector is witnessing the introduction of humanoid robots designed to perform tasks traditionally handled by humans. Companies like GXO Logistics are piloting humanoid robots from firms such as Agility Robotics and Apptronik to carry out functions like moving containers and recycling materials within warehouses.
These robots are equipped with advanced AI and mobility features, enabling them to navigate complex environments and interact safely with human workers. While still in the early stages, the deployment of humanoid robots aims to address labor shortages and enhance operational efficiency in logistics, indicating a significant shift towards more versatile and human-like automation solutions.
Global Industrial Robotics Market: Research Scope and Analysis
By Type Analysis
In the type segment of the global industrial robotics market, traditional robots are expected to maintain a commanding lead, projected to capture approximately 88.4% of the total market share in 2025. This dominance is largely attributed to their widespread deployment in high-throughput and precision-oriented manufacturing environments such as automotive, electronics, and heavy machinery. Traditional industrial robots, including articulated, SCARA, and Cartesian variants, are engineered for speed, durability, and repeatability.
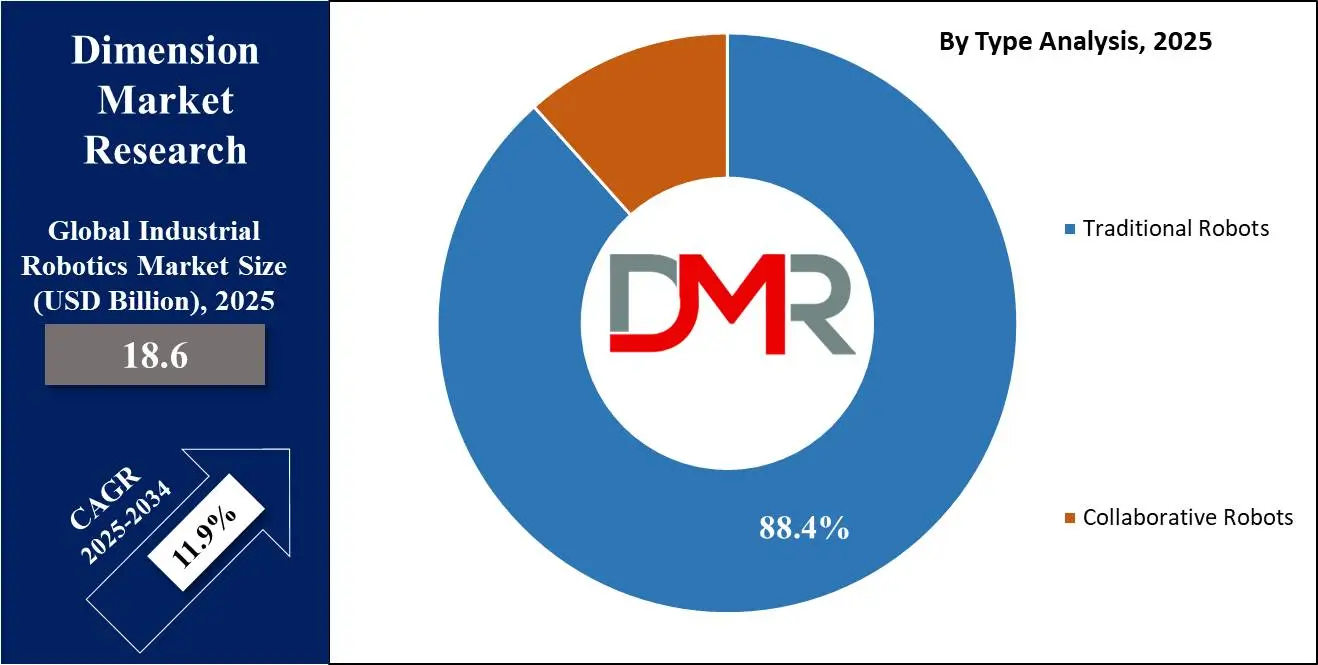
Their capacity to operate continuously in hazardous and demanding conditions without compromising output quality makes them essential in tasks such as welding, painting, stamping, and large-scale assembly. These robots thrive in structured environments where operations demand volume, reliability, and consistency. Their extensive global deployment, proven performance, and long operational lifespans further strengthen their stronghold across core industrial sectors.
Collaborative robots, on the other hand, are emerging as a fast-growing niche within the industrial robotics ecosystem. While their current market share remains modest, their value proposition lies in their flexibility, ease of integration, and ability to work safely alongside human workers without physical barriers. Cobots are particularly well-suited for small and medium enterprises, as they do not require major infrastructure changes and can be easily reprogrammed for multiple tasks.
Their application is expanding in areas such as light assembly, quality inspection, and packaging, where human-robot collaboration enhances productivity without displacing human labor. As manufacturers prioritize agility and workforce safety, the adoption of collaborative robots is expected to accelerate, contributing significantly to the diversification of robotic solutions across industries.
By Payload Analysis
In the payload type segment of the global industrial robotics market, the up to 16 kg category is anticipated to maintain its dominant position, capturing approximately 38.9% of the total market share in 2025. This segment benefits from the rapid growth of industries that demand precision, speed, and compact automation solutions, such as electronics, consumer goods, food processing, and pharmaceuticals. Robots in this payload range are typically lightweight, energy-efficient, and highly adaptable, making them ideal for delicate and repetitive tasks like pick and place, inspection, packaging, and small parts assembly.
Their compact footprint allows them to be integrated easily into existing production lines without requiring major layout changes. Additionally, this category is closely linked to the increasing adoption of collaborative robots, many of which fall under this weight class and are being deployed by small and medium-sized enterprises due to their cost-efficiency and operational flexibility.
The segment comprising robots with a payload range of more than 16 to 60 kg also plays a critical role in the industrial robotics landscape. These robots are designed to handle heavier components with greater force and stability, making them essential in applications that require both power and precision. Industries such as automotive, metal fabrication, and machinery manufacturing utilize this class of robots for tasks including material handling, medium-duty welding, palletizing, and complex assembly operations. They serve as a bridge between lightweight, high-speed robots and heavy-duty systems, offering a balance between performance and versatility.
By Offering Analysis
In the offering segment of the global industrial robotics market, industrial robots are expected to consolidate their market position strongly, projected to account for 57.3% of the total market share in 2025. This reflects the sustained global demand for core robotic systems that serve as the foundation of industrial automation across various manufacturing sectors. Industrial robots, which include articulated, SCARA, delta, and Cartesian types, are critical for executing essential tasks such as welding, painting, assembly, and packaging with precision and speed. Their scalability and application versatility enable manufacturers to automate workflows, reduce operational costs, and enhance production consistency.
As global industries strive to remain competitive in the face of fluctuating labor markets and rising production demands, investment in complete robotic units remains a top priority. Moreover, advancements in robotics design, durability, and sensor integration are further enhancing the functionality of industrial robots, making them the central element in modern smart factories.
While industrial robots form the core, robot accessories play a crucial role in enhancing the overall efficiency, customization, and capability of robotic systems.
Accessories such as end-effectors, sensors, grippers, tool changers, vision systems, and safety devices enable robots to perform specialized tasks tailored to specific industrial needs. The growing trend toward modular robotics is increasing demand for these add-ons, as manufacturers seek adaptable solutions that can evolve with changing production lines. For instance, a robotic arm fitted with interchangeable grippers and advanced vision sensors can switch between product lines with minimal downtime, maximizing asset utilization. Robot accessories are also key to improving safety and collaborative functionality, particularly in human-robot workspaces.
By Application Analysis
In the application segment of the global industrial robotics market, handling applications are projected to retain their dominant position, accounting for approximately 37.5% of the total market share in 2025. Handling tasks include a broad spectrum of activities such as material transfer, loading and unloading, sorting, packaging, and palletizing. These operations are critical across almost every manufacturing industry and are among the most frequently automated due to their repetitive nature and demand for precision and speed.
Robots deployed for handling help reduce cycle times, minimize errors, and ensure workplace safety by performing tasks that may be ergonomically challenging or hazardous for human workers. The increasing emphasis on streamlining supply chain operations, especially in logistics and e-commerce, has further accelerated the deployment of robots for handling purposes. Additionally, their scalability and ability to operate around the clock make them indispensable for high-volume production environments.
Assembling and disassembling applications form another vital part of the industrial robotics landscape, playing a central role in industries such as automotive, electronics, appliances, and medical device manufacturing. Robots performing assembly tasks are designed to join components with high accuracy and repeatability, ensuring product consistency and reducing defects. Disassembling, though less common, is gaining importance in the context of sustainability and circular manufacturing, where robots are used to dismantle products for repair, refurbishment, or recycling.
These applications often require greater dexterity and adaptability than basic handling tasks, prompting the integration of advanced features such as force sensors and machine vision systems. The demand for miniaturization in products, particularly in electronics, is pushing the development of robots capable of precise micro-assembly.
By End-Use Analysis
In the end-use type segment of the global industrial robotics market, the automotive industry is expected to maintain its dominant position, capturing approximately 31.3% of the total market share in 2025. This dominance is rooted in the automotive sector’s early and extensive adoption of industrial robotics, particularly for tasks such as welding, painting, assembly, and material handling. The high-volume and high-precision nature of automotive manufacturing makes it an ideal environment for automation. Robots are widely used across production lines for repetitive and physically demanding tasks that demand consistency and speed.
With the ongoing shift toward electric vehicles and increasing demand for model diversification, automotive manufacturers are further investing in robotics to streamline production flexibility and meet evolving consumer needs. The integration of robotics into smart factory environments, including collaborative and AI-enhanced robots, is also enhancing productivity and enabling real-time quality control in vehicle assembly processes.
The electrical and electronics industry also plays a significant and growing role in the industrial robotics market. This sector requires robots that can handle delicate components with extreme precision, making it one of the most robotics-intensive industries in terms of unit installations. Applications such as soldering, surface-mounting, micro-assembly, and testing demand a high degree of accuracy and speed, which industrial robots can consistently deliver.
The increasing miniaturization of electronic devices and the complexity of components have further amplified the need for advanced robotic systems capable of performing intricate tasks. Furthermore, the rapid innovation cycles and global demand for consumer electronics, semiconductors, and electronic control units in various devices have made flexible automation a strategic necessity.
The Industrial Robotics Market Report is segmented based on the following
By Type
- Traditional Robots
- Articulated Robots
- Scara Robots
- Parallel Robots
- Cartesian Robots
- Cylindrical Robots
- Other Traditional Robots
- Collaborative Robots
By Payload
- Up to 16 KG
- > 16 To 60 KG
- > 60 To 225 KG
- Above 225 KG
By Offering
- Industrial Robots
- Robot Accessories
- End Effectors
- Welding Guns
- Grippers
- Tool Changers
- Clamps
- Suction Cups
- Other end effectors
- Controllers
- Drive Units
- Hydraulic Drives
- Electric Drives
- Pneumatic Drives
- Vision Systems
- Sensors
- Power Supply Accessories
- Other Robot Accessories
- Other Robotic Hardware
- Safety Fencing Hardware
- Fixture Tools
- Conveyors Hardware
- System Engineering
- Software & Programming
By Application
- Handling
- Pick & Place
- Material Handling
- Packaging & Palletizing
- Assembling & Disassembling
- Wielding & Soldering
- Dispensing
- Gluing
- Painting
- Food Dispensing
- Processing
- Grinding & Polishing
- Milling
- Cutting
- Cleanroom
- Other Applications
By End-Use Industry
- Automotive
- Electrical & Electronics
- Metals & Machinery
- Plastics, Rubber & Chemicals
- Food & Beverages
- Precision Engineering & Optics
- Pharmaceuticals & Cosmetics
- Oil & Gas
- Other End-Use Industries
Global Industrial Robotics Market: Regional Analysis
Region with the Largest Revenue Share
Asia Pacific is anticipated to dominate the global industrial robotics market in 2025, accounting for approximately
66.4% of total global market revenue. This leadership position is driven by a powerful combination of manufacturing scale, technological advancement, and rising industrial automation across key economies in the region. Countries like China, Japan, South Korea, and India have become central hubs for industrial robot deployment due to their strong presence in automotive, electronics, and heavy machinery production.
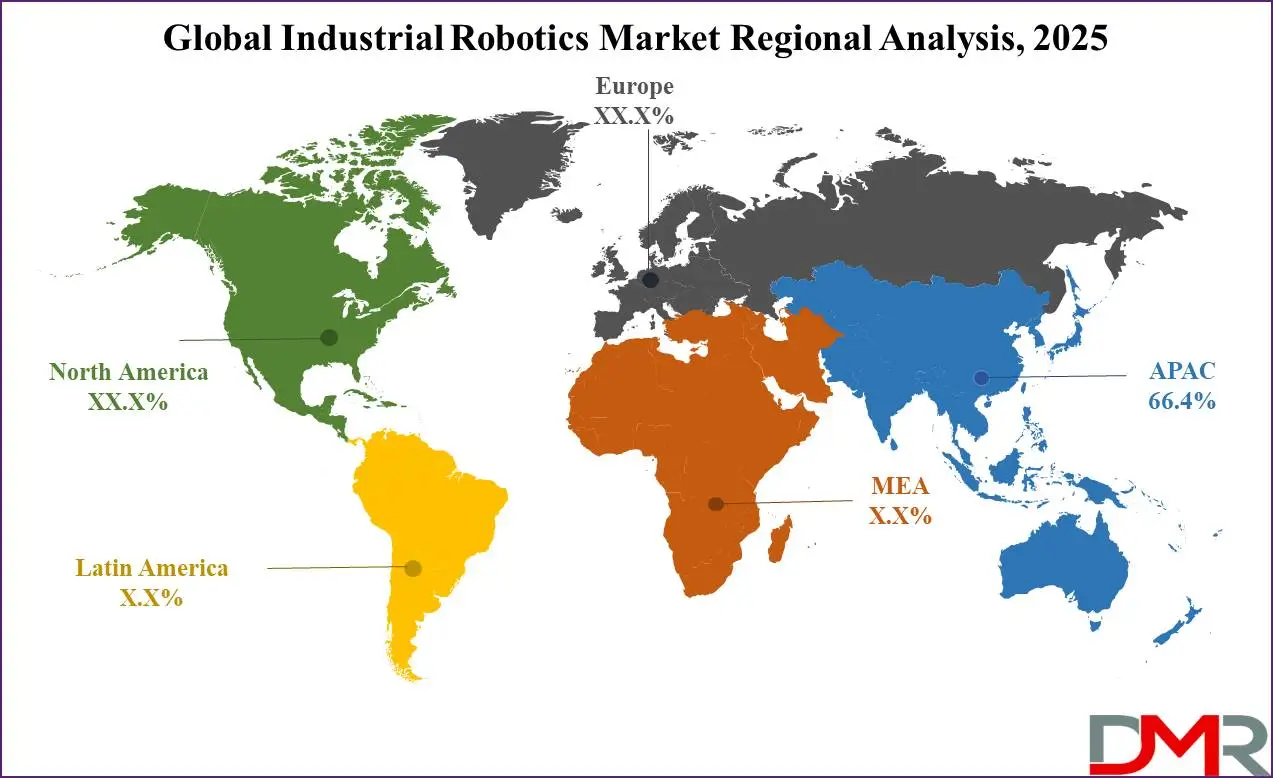
China, in particular, stands out as both the largest producer and consumer of industrial robots, heavily investing in factory automation as part of its Made in China 2025 strategy. The government’s push to move up the manufacturing value chain has led to aggressive adoption of robotics across a range of sectors, including semiconductors, energy equipment, and consumer goods.
Region with significant growth
North America is projected to register a significant annual growth in the global industrial robotics market through 2025, driven by a surge in automation adoption across a wide range of industries and a strong focus on technological innovation. The region’s manufacturing sector, particularly in the United States and Canada, is undergoing a significant transformation as companies strive to address labor shortages, enhance operational efficiency, and improve product quality through advanced robotics solutions.
With rising wage costs and a growing need for consistent output, industries such as automotive, aerospace, food and beverages, and electronics are turning to industrial robots to remain competitive on a global scale. One of the key factors propelling this growth is the rapid integration of cutting-edge technologies such as artificial intelligence, machine learning, vision systems, and cloud connectivity into industrial robots.
By Region
North America
Europe
- Germany
- The U.K.
- France
- Italy
- Russia
- Spain
- Benelux
- Nordic
- Rest of Europe
Asia-Pacific
- China
- Japan
- South Korea
- India
- ANZ
- ASEAN
- Rest of Asia-Pacific
Latin America
- Brazil
- Mexico
- Argentina
- Colombia
- Rest of Latin America
Middle East & Africa
- Saudi Arabia
- UAE
- South Africa
- Israel
- Egypt
- Rest of MEA
Global Industrial Robotics Market: Competitive Landscape
The global competitive landscape of the industrial robotics market is highly dynamic and characterized by the presence of both established players and emerging innovators competing across technology, geography, and vertical applications. Leading companies in this space are focused on expanding their global footprint, improving robot intelligence and flexibility, and offering customized automation solutions to cater to the evolving needs of manufacturers.
Key players such as ABB, FANUC, Yaskawa Electric, KUKA, and Mitsubishi Electric have built a robust foundation through decades of expertise, broad product portfolios, and strong customer relationships across diverse industries. These companies are continuously investing in R&D to enhance robot precision, speed, energy efficiency, and integration with digital systems such as IoT platforms and AI-based control systems.
Meanwhile, companies like Universal Robots, Techman Robot, and Doosan Robotics are driving competition in the collaborative robotics segment by developing lightweight, user-friendly robots that cater to the needs of small and medium enterprises. These cobot manufacturers are reshaping how automation is perceived and adopted in sectors that traditionally relied on manual labor due to budget constraints or space limitations. Their competitive advantage lies in ease of use, lower cost of ownership, and the ability to safely work alongside humans without the need for extensive safety barriers or complex programming.
Some of the prominent players in the Global Industrial Robotics industry are
- ABB
- FANUC Corporation
- Yaskawa Electric Corporation
- KUKA AG
- Mitsubishi Electric Corporation
- Kawasaki Heavy Industries
- Epson Robotics
- Denso Corporation
- Nachi-Fujikoshi Corp
- Universal Robots
- Omron Corporation
- Staubli International AG
- Comau S.p.A.
- Techman Robot Inc.
- Siasun Robot & Automation
- Hyundai Robotics
- Delta Electronics
- Toshiba Machine Co., Ltd.
- IAI Corporation
- Doosan Robotics
- Other Key Players
Global Industrial Robotics Market: Recent Developments
- January 2024: Yaskawa Electric acquired a majority stake in German robotics integrator RobShare GmbH, boosting its integration capabilities and service offering in the European industrial automation market.
- October 2023: FANUC partnered with and later acquired specific IP from Deep Learning Robotics Ltd., aiming to enhance its robotic vision systems with AI-powered visual learning technologies.
- August 2023: Rockwell Automation acquired Clearpath Robotics, a Canadian leader in autonomous mobile robots and software, to strengthen its portfolio in intelligent logistics and industrial automation.
- June 2023: Omron Corporation acquired a controlling interest in Techman Robot, a Taiwanese collaborative robot manufacturer, to jointly expand global cobot deployments across industries like electronics and automotive.
- March 2023: Siemens acquired a minority stake in Energy Robotics, a German startup developing AI-powered software for mobile inspection robots, marking its entry into intelligent robotic systems for industrial use.
- October 2022: Zebra Technologies acquired Matrox Imaging, a move designed to bolster its machine vision capabilities within robotics used in manufacturing, logistics, and automation sectors.
- July 2022: AMETEK Inc. acquired Alphasense, a specialist in sensor technologies that are integrated into industrial robotics for advanced motion and environmental awareness.
- May 2022: Hyundai Motor Group completed the acquisition of Boston Dynamics from SoftBank, aiming to accelerate its smart mobility and robotics capabilities with a focus on AI-driven humanoid and industrial robots.
- February 2022: Teradyne, the parent company of Universal Robots, acquired AutoGuide Mobile Robots to complement its collaborative robot offerings with autonomous mobile robots for flexible material handling.
- January 2022: ABB acquired ASTI Mobile Robotics Group, a leading provider of autonomous mobile robots (AMRs), to strengthen its automation portfolio and expand its presence in the logistics and warehousing sectors.
Report Details
Report Characteristics |
Market Size (2025) |
USD 18.6 Bn |
Forecast Value (2034) |
USD 51.4 Bn |
CAGR (2025-2034) |
11.9% |
Historical Data |
2019 – 2024 |
The US Market Size (2025) |
USD 3.1 Bn |
Forecast Data |
2025 – 2033 |
Base Year |
2024 |
Estimate Year |
2025 |
Report Coverage |
Market Revenue Estimation, Market Dynamics, Competitive Landscape, Growth Factors and etc. |
Segments Covered |
By Type (Traditional Robots and Collaborative Robots), By Payload (Up to 16 kg, > 16 To 60 KG, > 60 To 225 KG, and Above 225 KG), By Offering (Industrial Robots, Robot Accessories, Other Robotic Hardware, System Engineering, and Software & Programming), By Application (Handling, Assembling & Disassembling, Wielding & Soldering, Dispensing, Processing, Cleanroom, and Other Applications), and By End-Use Industry (Automotive, Electric & Electronics, Metals & Machinery, Plastics, Rubber & Chemicals, Food & Beverages, Precision Engineering & Optics, Pharmaceuticals & Cosmetics, Oil & Gas, and Other End-Use Industries) |
Regional Coverage |
North America – The US and Canada; Europe – Germany, The UK, France, Russia, Spain, Italy, Benelux, Nordic, & Rest of Europe; Asia- Pacific– China, Japan, South Korea, India, ANZ, ASEAN, Rest of APAC; Latin America – Brazil, Mexico, Argentina, Colombia, Rest of Latin America; Middle East & Africa – Saudi Arabia, UAE, South Africa, Turkey, Egypt, Israel, & Rest of MEA
|
Prominent Players |
ABB, FANUC Corporation, Yaskawa Electric Corporation, KUKA AG, Mitsubishi Electric Corporation, Kawasaki Heavy Industries, Epson Robotics, Denso Corporation, Nachi-Fujikoshi Corp, Universal Robots, Omron Corporation, Staubli International AG, Comau S.p.A., Techman Robot Inc., Siasun Robot & Automation, Hyundai Robotics, Delta Electronics, Toshiba Machine Co., Ltd., IAI Corporation, Doosan Robotics, and Other Key Players |
Purchase Options |
We have three licenses to opt for: Single User License (Limited to 1 user), Multi-User License (Up to 5 Users) and Corporate Use License (Unlimited User) along with free report customization equivalent to 0 analyst working days, 3 analysts working days and 5 analysts working days respectively. |
Frequently Asked Questions
The global industrial robotics market size is estimated to have a value of USD 18.6 billion in 2025 and is expected to reach USD 51.4 billion by the end of 2034.
The US industrial robotics market is projected to be valued at USD 3.1 billion in 2025. It is expected to witness subsequent growth in the upcoming period as it holds USD 8.2 billion in 2034 at a CAGR of 11.2%.
Asia Pacific is expected to have the largest market share in the global industrial robotics market, with a share of about 66.4% in 2025.
Some of the major key players in the global industrial robotics market are ABB, FANUC Corporation, Yaskawa Electric Corporation, KUKA AG, Mitsubishi Electric Corporation, Kawasaki Heavy Industries, Epson Robotics, Denso Corporation, Nachi-Fujikoshi Corp, Universal Robots, Omron Corporation, Staubli International AG, Comau S.p.A., Techman Robot Inc., Siasun Robot & Automation, Hyundai Robotics, Delta Electronics, Toshiba Machine Co., Ltd., IAI Corporation, Doosan Robotics, and Other Key Players.
The market is growing at a CAGR of 11.9 percent over the forecasted period.