Market Overview
The Global Nitrile Butadiene Rubber Market size is expected to be valued at
USD 2.8 billion in 2025, and it is further anticipated to reach a market value of
USD 4.8 billion by 2034 at a
CAGR of 6.3%.
The Nitrile Butadiene Rubber (NBR) market refers to the global production, distribution, and consumption of Nitrile Butadiene Rubber elastomers produced from copolymerizing acrylonitrile and butadiene monomers. NBR is widely recognized for its excellent resistance to oils, fuels, and chemicals qualities which makes it indispensable in various industries such as automotive, healthcare, industrial manufacturing, and oil & gas.
As an extremely versatile polymer, NBR stands out with excellent mechanical properties, resilience, heat resistance, and overall durability that make it a preferred material for creating gaskets, seals, hoses, gloves, and various industrial components. Due to these properties, its market has expanded across various sectors where reliability and performance under extreme are valued.
Nitrile Butadiene Rubber (NBR) is one of the primary materials utilized by the automotive industry due to its versatility and resilience. As global automotive production grows in emerging economies the demand for electric vehicles (EVs) along with advancements in automotive technology has risen. Moreover, demand for components that improve performance efficiency or longevity within automotive applications requiring specialization using NBR components will drive the production requirements for these specialized components that enhance vehicle performance, efficiency, or longevity.
Healthcare facilities have seen an exponential surge in their need for NBR products, such as medical gloves. These material offers outstanding chemical and puncture resistance and flexibility, making them an excellent choice for disposable gloves used by medical professionals and laboratory workers. As public health awareness increases and healthcare regulations tighten its uses expand beyond gloves such as seals for syringes which enhances its role within healthcare production.
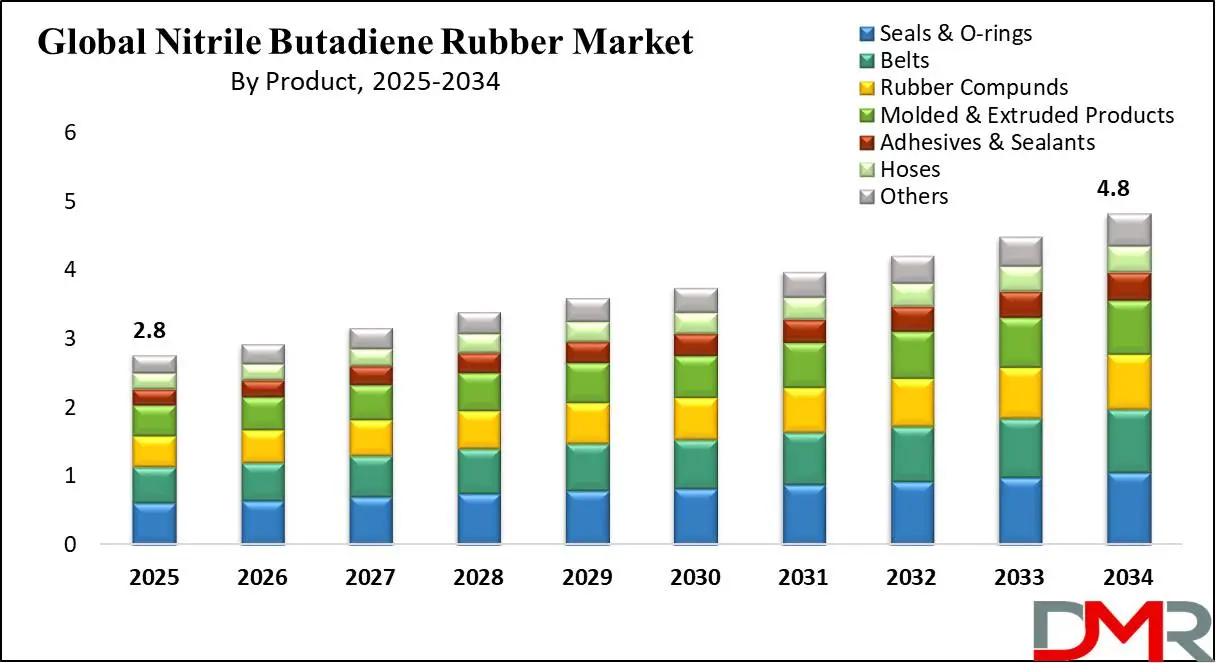
NBR is an invaluable material in this sector due to its resistance to oil, fuels, and harsh chemicals, it plays a pivotal role in seals, gaskets, and O-rings used in exploration, drilling, and refining processes. Due to the industry's dependence on machinery and equipment that can withstand extreme conditions, NBR-based products have seen steady demand.
The US Nitrile Butadiene Rubber Market
The US Nitrile Butadiene Rubber Market is projected to be valued at USD 0.7 billion in 2025. It is further expected to witness subsequent growth in the upcoming period, holding USD 1.2 billion in 2034 at a CAGR of 5.9%.
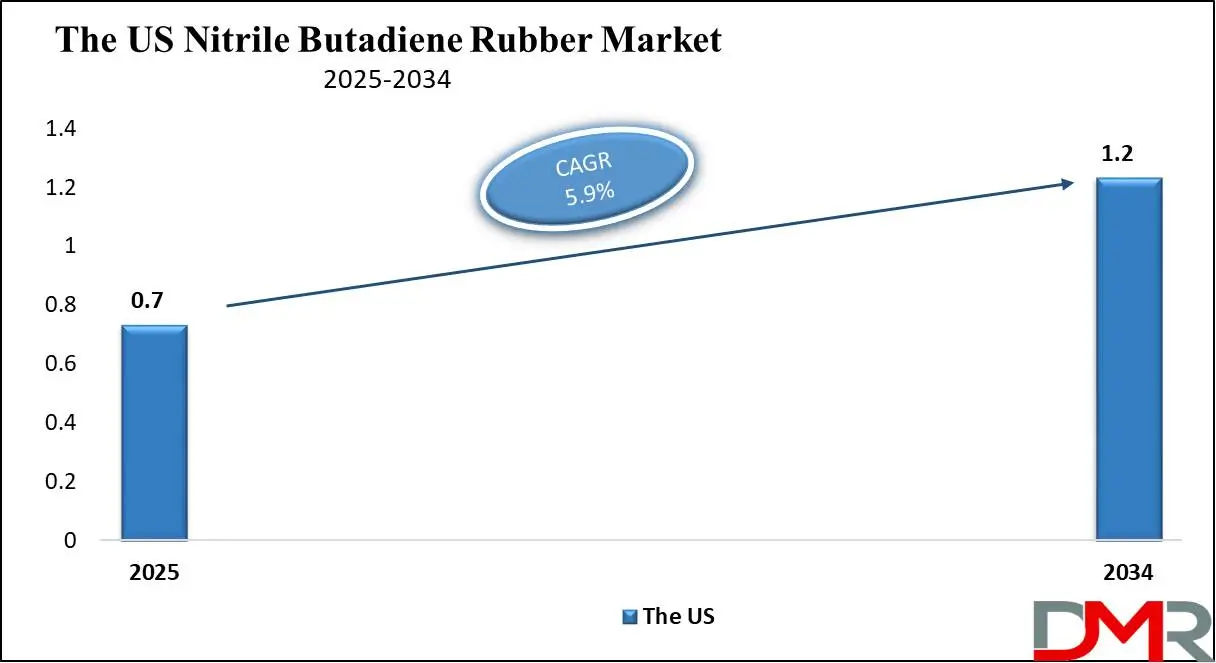
The US Nitrile Butadiene Rubber (NBR) market is an integral component of the global NBR industry, driven by robust industrial, automotive, healthcare, and manufacturing sectors. As an oil, fuel, and chemical resistant synthetic elastomer compound material known for durability in demanding industrial settings, NBR plays an essential role across multiple industries that require durable yet flexible materials suitable for demanding industrial settings applications. Within the automotive sector, the US market is one of the primary consumers of NBR. NBR can be found in components such as fuel hoses, seals, gaskets, vibration dampers, and vibration absorbers.
The US automotive industry continues its steady expansion with the arrival of electric vehicles (EVs) as well as advancements in safety and fuel efficiency technologies. Major players include General Motors, Ford, and Chrysler. Healthcare sectors in the US have made major contributions to NBR demand, especially through nitrile glove use.
NBR medical gloves are highly sought out due to their exceptional chemical and puncture resistance, providing enhanced protection from hazardous substances, viruses, and bacteria. As health and safety regulations tighten in medical and laboratory environments, demand for nitrile gloves in the US should remain robust. NBR gloves can also be used as seals on syringes, blood bags, and catheter components, further increasing their importance within healthcare industries.
Global Nitrile Butadiene Rubber: Key Takeaways
- Market Value: The global nitrile butadiene rubber market size is expected to reach a value of USD 4.8 billion by 2034 from a base value of USD 2.8 billion in 2025 at a CAGR of 6.3%.
- By Application Type Segment Analysis: Automotive application is anticipated to lead in the application type segment, capturing 40.0% of the market share in 2025.
- By Product Segment Analysis: Seals & O-rings is poised to consolidate its market position in the product segment capturing 22.0% of the total market share in 2025.
- Regional Analysis: Asia Pacific is anticipated to lead the global nitrile butadiene rubber landscape with 35.8% of total global market revenue in 2025.
- Key Players: Some major key players in the global nitrile butadiene rubber market are Arlanxeo, Zeon Chemicals L.P., Nitriflex, Sibur, PetroChina Company Limited, Dynasol Group, and Other Key Players.
Global Nitrile Butadiene Rubber Market: Use Cases
- Automotive Industry: NBR is extensively used in the automotive sector for manufacturing components that require resistance to oils, fuels, and high temperatures. Common applications include fuel hoses, seals, gaskets, and vibration dampers. The material’s durability, combined with its ability to withstand extreme conditions, makes it essential for ensuring vehicle safety, longevity, and performance. As automotive technologies evolve, particularly with the rise of electric vehicles (EVs), the demand for NBR in-vehicle components is expected to continue growing.
- Medical and Healthcare Products: One of the fastest-growing applications of NBR is in the production of medical gloves. NBR’s resistance to chemicals, oils, and punctures makes it ideal for disposable gloves used in healthcare and laboratory environments. Additionally, NBR is used in other medical devices, such as seals for syringes, blood bags, catheters, and other diagnostic and therapeutic tools.
- Oil & Gas Industry: NBR is widely used in the oil and gas sector due to its excellent resistance to oil, fuels, and harsh chemicals. It is essential for manufacturing components like seals, gaskets, O-rings, and hoses used in machinery and equipment involved in exploration, drilling, and refining processes. As oil extraction activities move into more extreme environments (e.g., deep-sea drilling), NBR’s ability to withstand high temperatures and pressure continue to make it an invaluable material for ensuring the reliability and performance of equipment in the oil and gas industry.
- Industrial Manufacturing: In the industrial sector, NBR is used for various machinery components, seals, and gaskets that need to operate in environments where they are exposed to oils, greases, and chemicals. NBR’s mechanical strength and ability to endure harsh working conditions make it ideal for industrial applications such as hydraulic systems, conveyor belts, and vibration dampers. It is also used in the production of automated equipment and heavy machinery components where reliability and durability are critical. The expansion of manufacturing sectors in emerging economies continues to drive the demand for NBR in industrial applications.
Global Nitrile Butadiene Rubber Market: Stats & Facts
- According to the Ministry of Chemicals and Fertilizers (Government of India), the production of nitrile butadiene rubber has risen from 11.9 thousand MT (Metric Tons) in 2020-2021 to 14.5 MT in 2023-2024.
- In addition, the CAGR for production from 2016-2024 was 69.9.
- Further, the utilization of nitrile butadiene rubber was 83.1% in 2023-2024.
- Furthermore, the installed capacity has risen from 13.7 MT in 2021- 2022 to 17.4 MT in 2023-2024.
Global Nitrile Butadiene Rubber Market: Market Dynamic
Global Nitrile Butadiene Rubber Market: Driving Factors
Growing Demand for Nitrile Gloves in the Healthcare Sector
One of the primary factors contributing to the growth of the global Nitrile Butadiene Rubber (NBR) market is the increased demand for disposable gloves made of NBR in healthcare applications. Nitrile gloves made of NBR are widely utilized due to their excellent protective qualities in hospitals, laboratories, and other environments.
They're resistant to oils, chemicals, and punctures making them an excellent choice for professionals in hospitals, labs, and other areas where infection control concerns are high. As regulations regarding health and safety within healthcare facilities become stricter along with infection control measures the demand for disposable gloves has increased exponentially, driving demand from healthcare applications.
NBR gloves are preferred over latex gloves due to being hypoallergenic, eliminating the risk of allergic reactions among healthcare workers and patients, an essential consideration in environments that prioritize patient safety and wellbeing. Furthermore, NBR gloves provide great comfort, flexibility, and durability, making them suitable for procedures requiring precision dexterity while offering maximum protection. With such qualities, nitrile gloves are popular among not only healthcare providers but also workers in industries like pharmaceuticals, food processing, and sanitation.
Increasing Automotive Production and Demand for Durable Components
Nitrile Butadiene Rubber (NBR) market growth can be attributed to increasing automotive production and rising demands for durable yet high-performing materials in vehicle manufacturing. NBR is widely utilized in this sector for producing essential automotive components such as fuel hoses, seals, gaskets, and vibration dampers.
As automotive manufacturers strive to meet stringent performance and safety standards, they increasingly rely on NBR components that can withstand modern vehicles' rigorous requirements for battery seals, cable insulations, and other critical parts that need to withstand oils, chemicals, and high temperatures. NBR materials offer manufacturers an edge when designing components suitable for electric and hybrid vehicles such as battery seals that resist oils, chemicals, and high temperatures as well as their tough environmental conditions.
NBR is an indispensable material that plays a key role in optimizing vehicle performance by offering applications ranging from sealing to noise reduction. As more advanced technologies, such as autonomous driving and electric drivetrains, become mainstream, the need for high-performance and durable materials like NBR will increase. The expansion of global automobile production integrated with technological innovations positions NBR as an essential material in ensuring future market expansion for this sector.
Restraints
Fluctuating Raw Material Prices
One key restraint on the global Nitrile Butadiene Rubber (NBR) market is fluctuating raw material prices, particularly in acrylonitrile and butadiene, two essential components used to manufacture NBR. Their prices can be strongly affected by supply or demand dynamics, geopolitical factors, and crude oil price changes. As both components originate in petrochemical processes any volatility directly affects production costs for NBR production.
Price fluctuations can lead to unstable production costs, making it challenging for manufacturers to maintain stable pricing for NBR-based products. When raw material costs increase, pressure may arise on manufacturers either to absorb those costs themselves and reduce margins or pass along increased expenses to customers which could reduce competitiveness in the market.
Furthermore, supply chain disruptions or an increase in petrochemical product demand could limit availability resulting in limited production capacity and market expansion. Unpredictability in raw material costs poses a unique set of challenges to both NBR producers and consumers, especially industries with stringent cost control such as automotive and healthcare. While demand for NBR continues to rise, its cost volatility of raw materials remains a key restraint on market stability and growth.
Competition from Alternative Materials
Nitrile Butadiene Rubber (NBR) faces intense competition from various alternative materials that offer comparable or even superior properties in certain applications. Notable alternatives to NBR include the
Ethylene Propylene Diene Monomer (EPDM) Market, silicone rubber, and hydrogenated nitrile rubber (HNBR). These materials have become popular choices among industries that demand high-performance polymers to withstand environmental factors like heat exposure, UV rays, or weathering conditions. The Ethylene Propylene Diene Monomer (EPDM) Market is often preferred over NBR for outdoor and automotive applications due to its superior resistance to ozone, UV rays, and extreme temperatures. Silicone rubber has long been considered biocompatible with food processing equipment due to its superior heat resistance.
HNBR, an advanced form of NBR with enhanced chemical resistance provides additional durability under high-temperature environments making it a good option in automotive, oil & gas, and other industrial applications. As these alternative materials continue to advance, they present challenges to the NBR market. While NBR remains popular in sectors like automotive, healthcare, and industrial manufacturing due to its oil, fuel, and chemical resistance properties, expanded use of alternatives is cutting into its market share in certain fields, particularly automotive.
Opportunities
Expanding Demand for Electric Vehicles (EVs)
Nitrile Butadiene Rubber (NBR) manufacturers see electric vehicles (EVs) as an invaluable opportunity in terms of market expansion. As automotive industries embrace more eco-friendly technologies and components for the production of EVs, NBR serves as an important application in this industry, necessary for their safe performance and use. The surge in electric vehicle (EV) adoption is driven by stringent government regulations designed to lower carbon emissions, as well as consumer preference for cleaner and more energy-efficient transportation options.
As automakers look to improve performance and reliability in electric cars, demand for durable materials like NBR is expected to increase, specifically for components able to withstand high voltage environments without leakage of fluids making NBR an integral component in battery systems and charging components used by electric vehicles.
NBR's flexibility and durability make it an essential material in developing effective seals and insulation systems for electric vehicles, which protect sensitive electronic parts from environmental elements or potential damage. As the global transition towards electric mobility accelerates, demand for high-performance elastomers such as NBR is anticipated to surge, offering manufacturers valuable growth opportunities.
Growth in Renewable Energy Applications
Nitrile Butadiene Rubber (NBR) stands to gain from renewable energy's growing prominence and the global shift towards sustainable power sources, offering promising prospects for its market. As more nations and industries invest in wind, solar, and other renewable energy infrastructures such as energy storage systems or wind turbine seals that withstand harsh environmental conditions and have long-term durability.
NBR boasts exceptional resistance against oils, fuels, and extreme temperatures making it perfect for use as wind turbine seals, solar panel components, or energy storage system components.
Wind energy applications often demand seals, gaskets, and hoses that can withstand UV radiation exposure, extreme weather conditions, and high-pressure environmental conditions. As wind turbine maintenance costs continue to escalate due to energy storage solutions such as batteries and capacitors becoming essential components for energy distribution, insulation from environmental factors poses a potential threat.
Trends
Shift Toward Sustainable and Eco-Friendly Materials
Nitrile Butadiene Rubber (NBR) compound customization has seen steady improvement to meet the specific and diverse demands of various industries, with manufacturers increasingly focused on optimizing properties by fine-tuning acrylonitrile content, crosslinking agents and adding specialty additives, which enables enhanced features like greater wear resistance, heat stability, and chemical resistance that meet different applications' specific requirements. This trend is most evident in industries such as automotive, healthcare, and oil & gas. For example, NBR compounds in automotive have been modified to withstand higher temperatures while still offering durable seals, gaskets, and hoses.
Similarly in healthcare, disposable gloves feature customized NBR formulations designed to provide optimal flexibility and tactile sensitivity that medical professionals require for effective grip.
As manufacturers seek to fulfill more demanding applications with customized NBR compounds, it has opened up new avenues of market growth. This ensures NBR remains cost-competitive across several sectors while meeting the changing needs of industries and communities. Customization will likely continue as an innovative catalyst that increases NBR's market presence over time.
Integration of NBR in Emerging Technologies
Nitrile Butadiene Rubber (NBR) has become increasingly prevalent in emerging technologies. Industries embracing innovative solutions have integrated NBR into sectors like electric vehicles (EVs), renewable energy, and smart manufacturing where high-performance materials are essential. NBR boasts exceptional resistance against heat, chemicals, and wear.
As such it serves as an essential material when producing components designed to withstand demanding environmental needs. NBR is frequently used within the electric vehicle industry for battery seals, charging cables, and insulating materials due to its durability and chemical resistance which is perfect for meeting the increasing demands of an ever-expanding EV market.
Furthermore, renewable energy applications like wind and solar use NBR in seals for turbines as well as gaskets for energy storage systems to withstand harsh weather and environmental factors. NBR usage has increased with the rise of smart manufacturing. Automation and robotics continue to revolutionize production processes, using NBR as precision components that require high resilience and stability in production processes. Due to its resilience against wear and harsh environments, this material makes an invaluable choice for robotic systems, actuators, and automated machinery.
Global Nitrile Butadiene Rubber Market: Research Scope and Analysis
By Product
Seals & O-rings is poised to consolidate its market position in the product segment capturing 22.0% of the total market share in 2025. This dominance can be attributed to a rising demand for sealing solutions across numerous industries, such as automotive, healthcare, oil & gas, and industrial manufacturing. Seals and O-rings play an integral role in ensuring the efficiency, safety, and performance of machinery, vehicles, and equipment by preventing fluid leakage, controlling pressure levels, and providing barriers against contaminants.
NBR, with its superior chemical resistance, durability, and ability to handle high-pressure conditions is an ideal material choice for these applications. NBR O-rings and seals have become indispensable components for engines, fuel systems, transmissions, and brake systems. As vehicles become more sophisticated, the need for high-performing seals that can withstand harsh environments has grown.
Rubber is expected to gain prominence within this segment due to its extensive use in sealing applications. Rubber-based materials remain highly sought, after due to their elasticity, flexibility, cost-effectiveness, and long lifespan making them an attractive option for manufacturers looking for long-lasting with reliable performance across various industries. NBR rubber materials offer unparalleled solutions that meet these demands with its versatility of shapes and sizes that can meet most sealing needs across various sectors.
By Application
Automotive application is anticipated to lead in the application type segment, capturing 40.0% of the market share in 2025. This can be attributed to NBR's increasing use in vehicle components due to its excellent resistance against oils, fuels, and chemicals making it perfect for parts that come into direct contact with harsh substances or extreme conditions like gaskets, seals, fuel hoses, and vibration dampers that play key roles in modern vehicles.
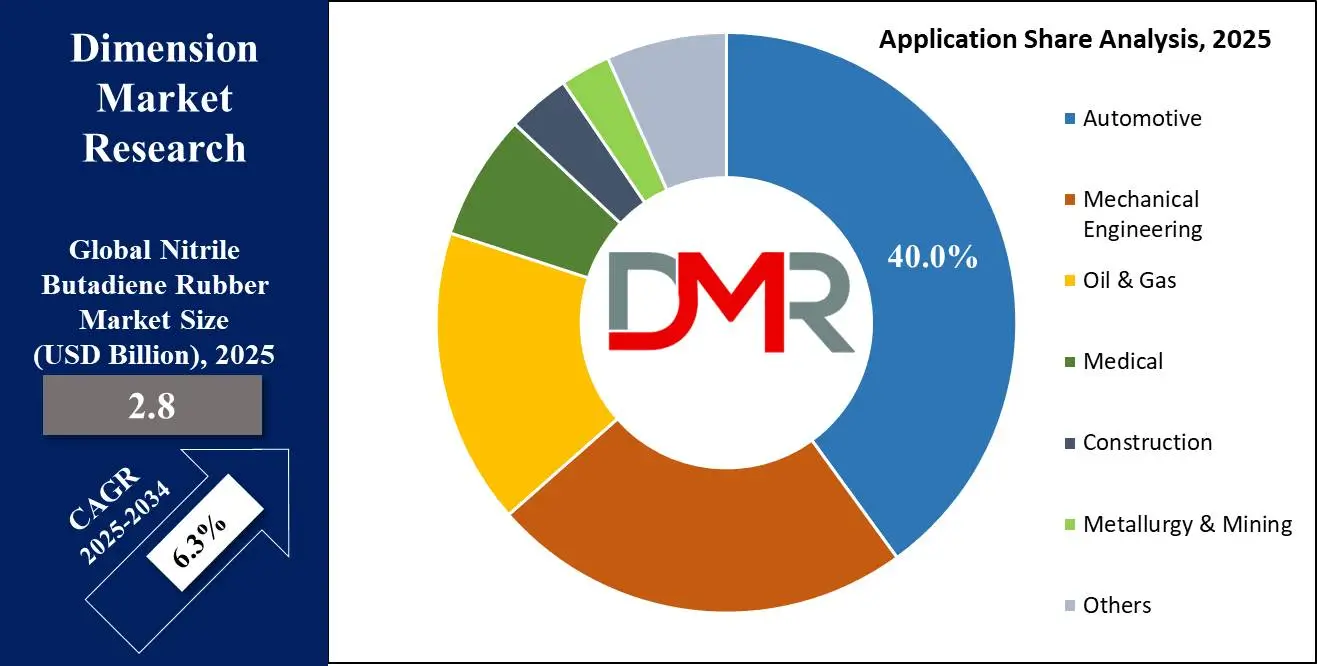
Manufacturers depend on NBR for increased performance longevity and vehicle durability as they seek durable materials that improve vehicle performance and longevity over time. As vehicle designs continue to prioritize efficiency, safety, and environmental sustainability, demand for high-performance materials such as NBR continues to increase. NBR is widely utilized in electric vehicles (EVs), where high-quality seals and gaskets shield sensitive components from environmental elements.
Mechanical engineering applications of NBR should also experience substantial growth. NBR materials provide durable yet high-performance solutions for machinery and systems in industrial settings. NBR rubber is an indispensable material in mechanical engineering due to its robust nature and ability to withstand exposure to oils, greases, and industrial chemicals, making it indispensable in seals, gaskets, bearings, and hoses for heavy machinery, automation systems, and industrial manufacturing environments. As industries automation processes expands, their need for materials that can withstand high-pressure and high-temperature environments increases exponentially.
The Nitrile Butadiene Rubber Market Report is segmented on the basis of the following:
By Product
- Seals & O-rings
- Belts
- Rubber Compounds
- Molded & Extruded Products
- Adhesives & Sealants
- Hoses
- Others
By Application
- Automotive
- Mechanical Engineering
- Oil & Gas
- Medical
- Construction
- Metallurgy & Mining
- Others
Global Nitrile Butadiene Rubber Market: Regional Analysis
Asia Pacific is anticipated to lead the global nitrile butadiene rubber landscape with 35.8% of total global market revenue in 2025. This dominance can be explained by several factors including Asia Pacific's robust industrial base and rapid economic development, along with rising demand across multiple sectors like automotive production centers and healthcare production facilities. Automotive industries across Asia Pacific are a primary driver of NBR consumption, particularly in countries like China, India, and Japan.
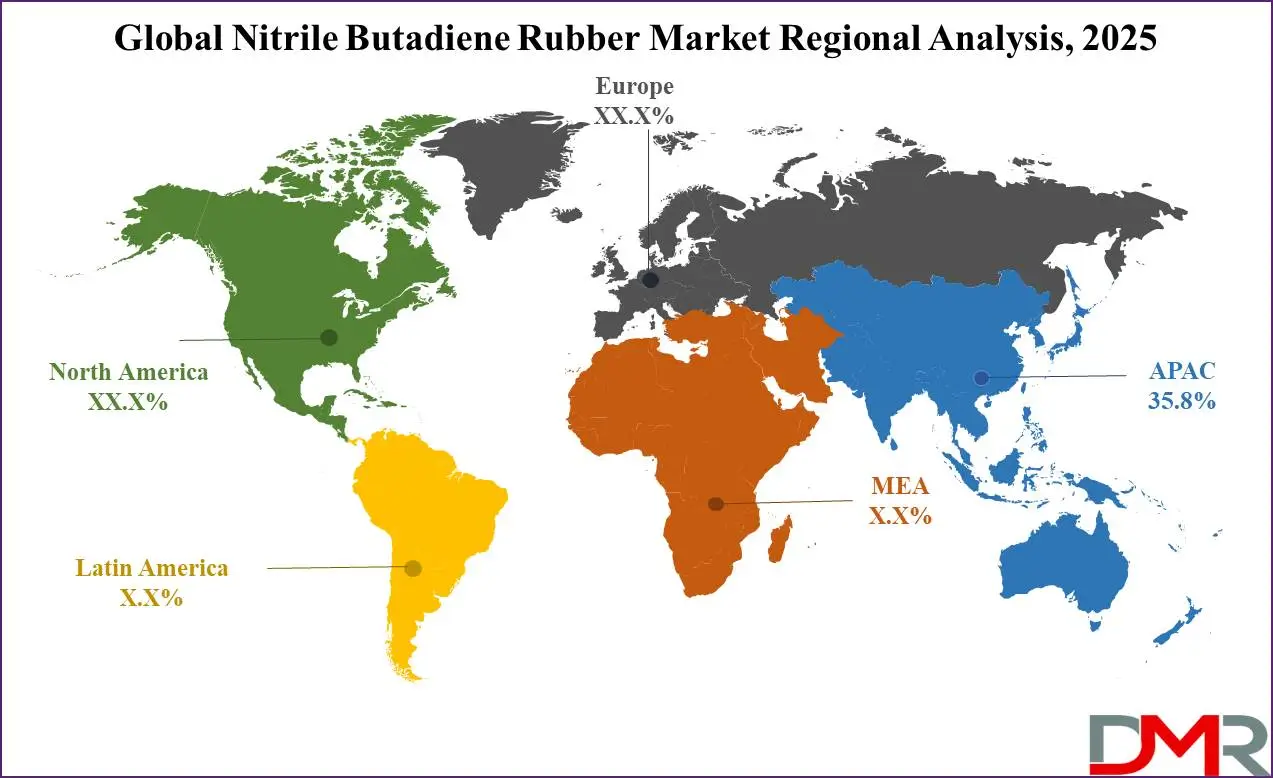
As these nations expand their automotive industries, demand for durable high-performance materials such as NBR is expected to increase accordingly. China is currently the world's largest automotive market and as it embraces electric vehicle (EV) adoption, their demand for NBR battery seals, gaskets, and charging systems is likely to rise.
North America, however, is expected to demonstrate steady performance in the NBR market with strong contributions coming from both US and Canada. North America's market share is projected to remain strong due to rising demand for high-performance seals and O-rings from various sectors such as automotive, aerospace, oil & gas, and healthcare.
U.S. technological innovation continues to lead the pack, fueling a need for more sophisticated and durable materials like NBR in electric vehicles (EVs), robotics, and medical device manufacturing. North America and particularly the US remain key players in shale oil extraction and offshore drilling operations, making NBR an indispensable material in these operations. Due to its ability to withstand exposure to extreme conditions such as temperatures, chemicals, pressure, and corrosion resistance.
By Region
North America
Europe
- Germany
- The U.K.
- France
- Italy
- Russia
- Spain
- Benelux
- Nordic
- Rest of Europe
Asia-Pacific
- China
- Japan
- South Korea
- India
- ANZ
- ASEAN
- Rest of Asia-Pacific
Latin America
- Brazil
- Mexico
- Argentina
- Colombia
- Rest of Latin America
Middle East & Africa
- Saudi Arabia
- UAE
- South Africa
- Israel
- Egypt
- Rest of MEA
Global Nitrile Butadiene Rubber Market: Competitive Landscape
Nitrile Butadiene Rubber (NBR) market competition is driven by numerous key players striving for market share through strategies like capacity expansions, technological upgrades, mergers & acquisitions, and product innovations. Companies operating in this sector focus on improving product quality while improving durability and sustainability to meet growing demands from industries like automotive, oil & gas, industrial manufacturing, healthcare, and aerospace. This creates an intensely competitive landscape consisting of both global and regional players trying to strengthen their positions through strategic investments and partnerships.
ARLANXEO, Kumho Petrochemical, JSR Corporation, Nantex Industry Co. Ltd., Zeon Corporation, LG Chem, Synthos S.A., Versalis S.p.A, and PetroChina Company Limited are among the key global players in the NBR market. These firms dominate this space by investing heavily in technological innovation, research & development (R&D), and expanding production capacities to meet rising global demand, as well as technological breakthroughs. One of the primary strategies used by leading players is expanding production facilities to meet growing industrial demand. Companies such as ARLANXEO and Kumho Petrochemical have invested in upgrading their manufacturing capabilities for producing NBR grades with superior heat and chemical resistance.
Some of the prominent players in the global nitrile butadiene rubber are:
- ARLANXEO
- Zeon Chemicals L.P.
- NITRIFLEX
- SIBUR
- PetroChina Company Limited
- Dynasol Group
- Synthos S.A.
- KUMHO PETROCHEMICAL
- LG Chem
- Versalis S.p.A.
- JSR Corporation
- AirBoss of America
- Atlantic Gasket Corporation
- Precision Associates, Inc.
- Anqing Hualan Technology Co., Ltd.
- NANTEX Industry Co., Ltd
- Apcotex Industries Limited
- Chang Rubber
- Hanna Rubber Company
- Other Key Players
Recent Developments
- October 2024: The Abu Dhabi National Oil Co. (ADNOC) acquired German polyurethane and polycarbonate material company Covestro A.G. for USD 12.9 billion. While primarily focused on polyurethanes and polycarbonates, this acquisition reflects the broader trend of consolidation in the chemical industry, which can have indirect effects on the NBR market.
- March 2024: Arlanxeo announced plans to construct a new hydrogenated nitrile butadiene rubber (HNBR) plant in China, with an annual production capacity of 30,000 tons. This initiative aims to expand Arlanxeo's presence in the Asia-Pacific region and meet the growing demand for HNBR, particularly in automotive and industrial applications.
- June 2023: Bridgestone entered into a long-term supply agreement with Kumho Petrochemical Co. Ltd. This partnership aims to secure a stable supply of NBR for Bridgestone's diverse product lines, including automotive components and industrial goods.
- May 2023: Sinopec's subsidiary, Hainan Baling Chemical New Material Co., Ltd., commenced operations at its new synthetic rubber plant in Hainan, China. The facility, a joint venture between Baling New Material and Sinopec’s subsidiary Hainan Refining & Chemical Co., has an annual production capacity of 170,000 tons.
- January 2023: Kumho Petrochemical Co. Ltd. announced plans to expand its NBR production capacity in South Korea. This move is part of the company's strategy to meet the increasing global demand for NBR across various industries.
Report Details
Report Characteristics |
Market Size (2025) |
USD 2.8 Bn |
Forecast Value (2034) |
USD 4.8 Bn |
CAGR (2025-2034) |
6.3% |
Historical Data |
2019 – 2024 |
The US Market Size (2025) |
USD 0.7 Bn |
Forecast Data |
2025 – 2033 |
Base Year |
2024 |
Estimate Year |
2025 |
Report Coverage |
Market Revenue Estimation, Market Dynamics, Competitive Landscape, Growth Factors and etc. |
Segments Covered |
By Product (Seals & O-rings, Belts, Rubber Compounds, Molded & Extruded Products, Adhesive & Sealants, Hoses, and Others), and By Application (Automotive, Mechanical Engineering, Oil & Gas, Medical, Construction, Metallurgy & Mining, and Others) |
Regional Coverage |
North America – The US and Canada; Europe – Germany, The UK, France, Russia, Spain, Italy, Benelux, Nordic, & Rest of Europe; Asia- Pacific– China, Japan, South Korea, India, ANZ, ASEAN, Rest of APAC; Latin America – Brazil, Mexico, Argentina, Colombia, Rest of Latin America; Middle East & Africa – Saudi Arabia, UAE, South Africa, Turkey, Egypt, Israel, & Rest of MEA
|
Prominent Players |
Arlanxeo, Zeon Chemicals L.P., Nitriflex, Sibur, PetroChina Company Limited, Dynasol Group, and Other Key Players |
Purchase Options |
We have three licenses to opt for: Single User License (Limited to 1 user), Multi-User License (Up to 5 Users) and Corporate Use License (Unlimited User) along with free report customization equivalent to 0 analyst working days, 3 analysts working days and 5 analysts working days respectively. |
Frequently Asked Questions
The global nitrile butadiene rubber market size is estimated to have a value of USD 2.8 billion in 2025 and is expected to reach USD 4.8 billion by the end of 2034.
The US nitrile butadiene rubber market is projected to be valued at USD 0.7 billion in 2025. It is expected to witness subsequent growth in the upcoming period as it holds USD 1.2 billion in 2034 at a CAGR of 5.9%.
Asia Pacific is expected to have the largest market share in the global nitrile butadiene rubber market with a share of about 35.8% in 2025.
Some of the major key players in the global nitrile butadiene rubber market are Arlanxeo, Zeon Chemicals L.P., Nitriflex, Sibur, PetroChina Company Limited, Dynasol Group, and many others.
The market is growing at a CAGR of 6.3 percent over the forecasted period.