The global vertical roller mill market is witnessing growth due to increased demand, particularly from the construction mining, and industrial sectors. Vertical roller mills find widespread applications in the grinding operation process in cement production, power generation, and mining, where efficiency, energy savings, and reduction of carbon emissions become vital. Thus, with industries striving toward low environmental impact and higher efficiency in operations, Vertical roller mills have emerged as one of the mainstays in the market.
The growth drivers of the VRM market involve the construction industry in general and emerging economies in particular. Due to rapid urbanization and the development of infrastructure, the cement requirement is growing in developing countries such as India, China, and Brazil. Consequently, the demand for Vertical roller mills has also grown directly.
This can also be related to the mining industry, as the processing of ores and minerals requires Vertical roller mills. As a result, this helps increase efficiency and cost-effectiveness throughout the entire mining operation.
The trend towards digitalization with the support of automation is rapidly gaining momentum in the market. Equipped with smart grinding technologies and automated process control systems, Vertical roller mills demonstrate improved performances and optimized cost of operation.
Besides this, many manufacturers are shrinking the size and weight of Vertical roller mills to give an added impetus to the mobility and installation features. However, despite the encouraging scenario, high procurement costs and skilled operators are some of the major impeding factors for the market growth. Moreover, fluctuating raw material prices and stringent environmental regulatory policies will further hinder the growth of the market.
North America is an established market for VRM due to rapid industrialization and the pacing of infrastructure projects. Asia Pacific and Europe also rank high in the market, due to modernization of existing infrastructures and technologies of energy efficiency. To summarize, the VRM market is of excellent prospects, with its steady market growth reliant on increasing demand for sustainable and efficient industrial processes.
The Vertical Roller Mill (VRM) market has seen substantial growth, with the global VRM installations surpassing 10,000 units in the past decade. In 2023, the cement industry accounted for over 60% of total VRM usage, while mining and power generation sectors followed closely behind with a combined share of approximately 30%. VRM manufacturers now operate across more than 80 countries worldwide.
The US Vertical Roller Mill Market
The US Vertical Roller Mill Market is projected to be valued at USD 185.3 million in 2024. It is expected to witness subsequent growth in the upcoming period as it holds USD 305.9 million in 2033 at a CAGR of 5.7%.
The demand for advanced and energy-efficient grinding technologies has always been very high in the United States vertical roller mill market. Presently, as energy consumption is being reduced on a large scale, and with infrastructural development steadily catching pace, VRM adoption has seen a significant surge in the last few years.
Another major driver in the U.S. market is the growth of the cement industry. The country is planning to undertake various large-scale construction and infrastructure projects. So any process that can give value addition and expedite cement production has become highly crucial. More Vertical roller mills are thus preferred over conventional mills because of their low power consumption and lower expenses on upkeep.
In addition, environmental regulations for reduced carbon emissions push industries toward cleaner technologies, further driving the vertical roller mill market. Major players in the U.S. market innovate and find ways to make Vertical roller mills more effective for themselves so that they remain within the shifting parameters of regulation.
Entrenched opportunities aside, there are challenges to be found in the U.S. vertical roller mill market, including high initial installation costs and substitution threats from other grinding technologies. However, the market is expected to grow, driven by the country's focus on sustainability and energy efficiency.
Key Takeaways
- Global Value: The global vertical roller mill market size is estimated to have a value of USD 608.5 million in 2024 which is expected to reach USD 1,041.2 million by the end of 2033.
- The US Market Size: The US vertical roller mill market is projected to be valued at USD 305.9 million in 2033 from a base value of USD 185.3 million in 2024 at a CAGR of 5.7%.
- By Product Segment Analysis: Spring-type vertical roller mills are projected to dominate this segment with 63.1% of the total market share by the end of 2024.
- By Application Segment Analysis: The coal industry is anticipated to dominate this segment as it command 39.1% of market share in 2024.
- Regional Analysis: North America is expected to have the largest market share in the Global Vertical Roller Mill Market with a share of about 36.2% in 2024.
- Global Growth Rate: The market is growing at a CAGR of 6.1 percent over the forecasted period.
Use Cases
- Cement Industry: Vertical roller mills play an integral part in the functionally economic production of cement, saving up to 30% energy compared to traditional ball mills.
- Coal Industry: Vertical roller mills find a wide application in power plants for coal grinding with the intention of uniformly sized particles for better combustion efficiency.
- Mining Industry: In mining, Vertical roller mills help reduce the ore to the desired fineness and do so by optimizing this process for the subsequent extraction with lower operational costs.
- Chemical Industry: These vertical roller mills are used to grind raw material mixtures for chemicals with high precision, and energy savings.
Market Dynamic
Trends
Shift Toward Energy-Efficient SolutionsConsidering the present global emphasis on sustainability and conservation of the environment, industries have taken to seeking such technologies that consume less energy, resulting in reduced carbon footprints. Vertical roller mills have been one focal point for this shift naturally, considering they might reduce energy usage by up to 30% compared to traditional ball mills.
This trend is highly evident in the cement industry, in which energy costs represent a substantial portion of production costs. Vertical roller mills foster lower operation costs and enable companies to comply with strict environmental policies that regulate and limit greenhouse gas emissions. Companies using Vertical roller mills are not only saving by taking this course of action but also enhancing their corporate social responsibility profiles, and hence becoming part of the global sustainability effort.
Technological Advancements in Mill Design
Continuously over the years, the development of VRM technology has seen great enhancements in mill performance, durability, and automation. Developments like wear-resistant materials extend the life expectancy of these critical components, reducing shutdown and maintenance costs. Advanced hydraulic systems can achieve high grinding pressure with very smooth operation, resulting in the quality of its final product.
Furthermore, the integration of automation and control systems enables real-time monitoring and adjustments, much for the optimization of the mill's performance. These newly developed technological aspects make Vertical roller mills more reliable and efficient, thus even more attractive in industries needing high-performance grinding solutions.
Customization and Flexibility in Applications
Manufacturers are now increasingly offering Vertical roller mills tailored to the particular needs of individual industries. This has opened up the accessibility of Vertical roller mills to applications that range from cement and mining to the processing of chemicals.
Other customizing features include variations in the mill size, capacity, and configuration made for the different types of raw material handling the ground. This art of customizing Vertical roller mills to suit particular operational needs further extends their charm and bridges their market, as the company can easily install these mills into already running production lines.
Growth Drivers
Rising Cement Demand in Emerging Economies
Emerging economies, especially in the Asia-Pacific, Africa, and Latin America, have been facing rapid urbanization and infrastructure development, hence creating a very firm demand for cement. Heavy investment in building construction includes residential and commercial buildings with transportation infrastructure in countries like China and India.
Such growth encourages the need for effective ways of producing cement; hence, Vertical roller mills have become an integral part of high-efficiency and good-quality grinding of cement with lower energy consumption. The growing demand for cement in these developing markets is directly driving the use of Vertical roller mills.
Stringent Environmental Regulations and Sustainability Goals
Due to the current threat of climate change, much stricter environmental regulations are being abided by and eventually passed into law around the world. High-energy and high-emission industries, like cement and mining, are constantly under pressure to switch to cleaner technologies. Vertical roller mills are seen as very environmentally friendly, with decreased energy consumption and subsequent lower emissions.
Companies can appeal to these regulations with the use of Vertical roller mills and still stay productive. In sum, this will prevent businesses from being faced with penalties caused by not adhering to these regulations and boost their reputation as responsible companies concerning environmental concerns. Technological investments and governmental support.
Technological Investments and Government Support
Most countries have government programs directed toward upgrading industrial equipment to stimulate growth and technical advancement. Governments offer grants, subsidies, and supportive policies to encourage companies to invest in top-of-the-range technologies like Vertical roller mills.
These indeed help reduce the cost of investment variably either by way of reducing the cost of equipment or engineering thus infirming the feasibility on an overall strategic basis. This would be very appropriate in developing countries where industrial development is a priority and modernization can bring about global competitiveness.
Growth Opportunities
Expansion in Emerging Markets and Untapped Regions
With industrialization and infrastructure development in full swing, there are considerable opportunities for VRM manufacturers in emerging markets. On the whole, Southeast Asia, Africa, and a part of Eastern Europe are experiencing overall growth in those industries that use Vertical roller mills, such as cement and mining. Companies can use this to their advantage by creating local partnerships, understanding regional needs, and offering solutions based on those requirements. This could create a significant increase in sales and market share in these markets.
Integration of Automation, AI, and Industry 4.0The adoption of Industry 4.0 principles essentially made manufacturing a highly automated and data-exchanging segment. The incorporation of
AI and
machine learning into Vertical roller mills further facilitated operational efficiency regarding predictive maintenance, optimization of the grinding process, and reduction of human error.
Smart Vertical roller mills can automatically adjust parameters using sensor data input in real-time toward better product quality and lower energy consumption. Offering innovative, automated Vertical roller mills automatically puts manufacturers at the front in terms of technology, hence attracting progressive companies seeking to implement modernization into their works.
Development of Vertical roller mills for New Applications
Other industries and applications can result in significant market growth for Vertical roller mills. For example, the development of Vertical roller mills for other alternative materials processing industries, such as industrial minerals, recycled materials, or even agricultural products, will create new market opportunities. Continuous research and development regarding diversification of the VRM capabilities even further can generate new products to meet the changing needs of different industries. In this way, reliance on traditional markets can be minimized and growth maintained.
Restraints
High Initial Investment Costs and Financing Challenges
Other industries and applications can result in significant market growth for Vertical roller mills. For example, the development of Vertical roller mills for other alternative materials processing industries, such as industrial minerals, recycled materials, or even agricultural products, will create new market opportunities.
Continuous research and development regarding diversification of the VRM capabilities even further can generate new products to meet the changing needs of different industries. In this way, reliance on traditional markets can be minimized and growth maintained.
Competition from Alternative Grinding Technologies
The adoption of VRMs requires heavy capital investment, which may be unaffordable for SMEs. This includes the cost required to purchase the equipment, retrofit facilities, and train personnel. The risk of economic uncertainty or lack of credit access in some regions contributes to strain when trying to acquire funds. For this reason, such financial limitations may discourage firms from investing in VRMs despite the long-term operational advantages.
Operational Complexity and Skill Requirements
Operating VRMs is an involved process fully dependent on technical know-how and expertise from the persons involved. Improper operation, due to the complexity of the technology, may lead to inefficiencies or damage to equipment. This poses a serious problem in areas where the shortage of skilled labor is a major constraint. Either way, one would be forced to invest in training programs or seek out external experts, therefore increasing operational costs and probably having issues with production delays.
Research Scope and Analysis
By Product Type
Spring-type vertical rollers are projected to dominate this segment as they hold 63.1% of the market share in 2024. The major share in this segment can be primarily attributed to offering constant grinding pressure with uniform particle size and a high degree of efficiency.
It finds wide application in the grinding of cement and mining, both of which demand ultimate precision in grinding. Moreover, spring-type mills are rugged in construction and can grind hard and abrasive materials without much wear and tear on the machine components, which further enhances the operating life of the mill.
Another dominating reason for the dominance of spring-type Vertical roller mills is the ability to process variable raw material feeds without compromising performance. In industries like cement production, where feed material quality usually varies, the spring system maintains a stable grinding pressure for the same output. That makes spring-type mills ideal for big industrial operations where downtime and the cost of maintenance are key concerns. Due to their high durability and efficiency in performance, the spring-loaded type of vertical roller mills is widely adopted by many industries.
Besides, compared with hydraulic systems, they need relatively low maintenance, thus allowing long-term cost efficiency. Probably, such demand would continue to be at high levels because industries are still interested in energy efficiency and operational stability.
By Type
In the market, the range of 200-400t/h is projected to dominate this segment due to its versatility and suitability for a wide range of industrial applications, especially in cement production and mining. This capacity range effectively balances the ideal relation of operational efficiency with flexibility, hence being the choice for most medium- to large-scale operations. With cement production, the largest end-user of VRMs, highly efficient mills lie in the range of 200-400 t/h. Most cement plants worldwide operate at capacities falling within this range.
These mills are, therefore, quite befitting the needs of the sector. The capacity range of 200-400 t/h allows adequate capacity to meet the requirements of medium and large-scale projects with energy-efficient grinding. This capacity is also compatible with the processing of high-class homogeneous cement production without overloading the equipment; hence, it is ideal.
With this range, scalability is afforded for those operations that are likely to grow in production with time. Yet, this range also attends to the most commonly treated materials in cement plants and other heavy industries at the mining, raw materials, and slag.
Flexibility in choosing raw materials and processes efficiently allows companies to meet market demand without changing the mill. Within this average segment of the mill, about capacity, flexibility, and energy efficiency, the segment between 200-400t/h is the dominant force in the VRM market.
By Operation Mode
Semi-automatic operations are projected to dominate the vertical roller mill market as they offer a balance between manual and completely automated systems with cost-effectiveness and operating efficiency. Semi-automatic mills require minimum human interference, with operators still being able to handle the main parameters related to the grinding process. This flexibility is quite valuable in certain industries, such as cement and mining, where quality input materials may vary and manual adjustments could still be vital.
One of the key advantages of semi-automatic vertical roller mills is their ability to maintain consistent performance under varying operating conditions. They are equipped with sensors and control systems that can optimize the grinding process, reducing energy consumption and improving mill efficiency. However, operators can still make adjustments based on real-time data, ensuring better control over the final product quality.
Besides, semi-automatic systems are usually easier and less costly to install than those of a fully automated mill. Lower complication and investment contribute to their popularity for medium-size enterprises in developing countries. In turn, this promotes the possibility of combining advanced technology with human control allowing semi-automatic VRMs to provide efficient performance at a reasonable operation cost level. Semi-automatic grinding will still dominate the market because this provides flexibility and efficiency in industries that face continuous demands for grinding.
By Application
The coal industry is projected to dominate the application segment as it will hold 39.1% of the market share in 2024. Coal remains one of the principal uses of vertical roller mills, with cogeneration in power generation and industrial processes requiring the grinding provided by the mill.
Vertical roller mills are especially suited for coal grinds because they also dry the coal without using heat or natural gas and produce a uniform particle size essential for efficient combustion in coal-fired generating plants. The consistency and precision provided by Vertical roller mills ensure optimal fuel utilization, reducing emissions while improving overall energy efficiency.
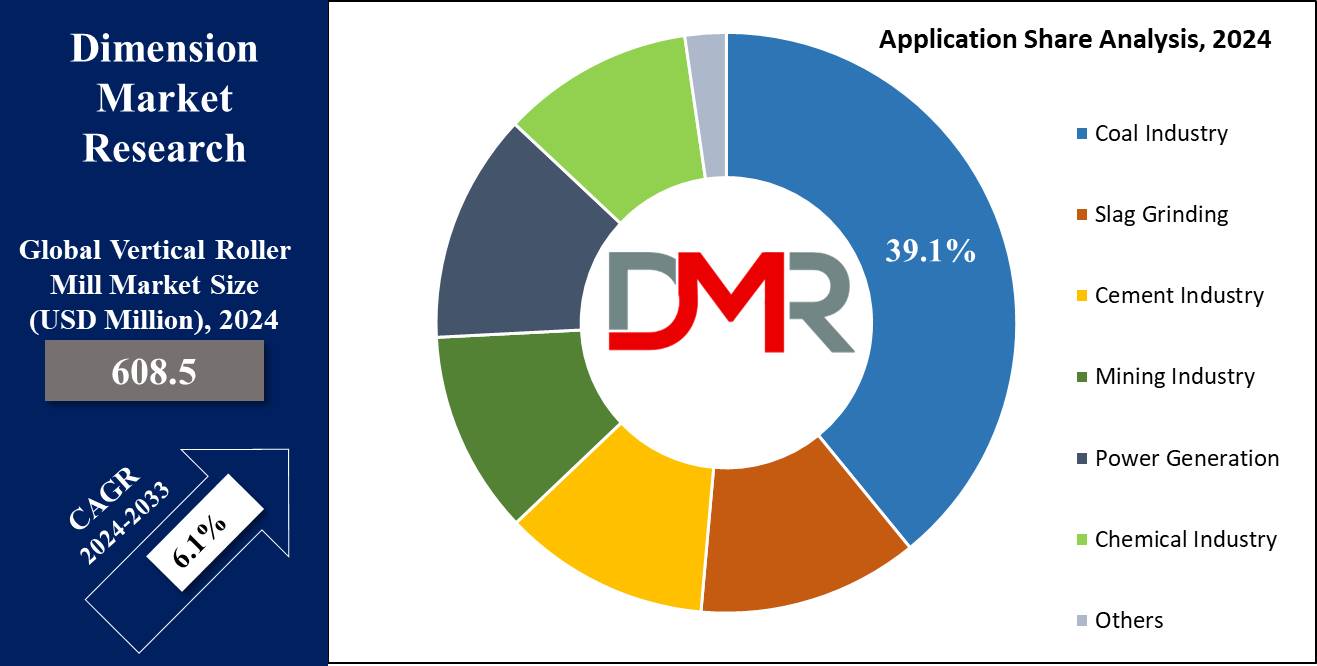
The coal industry grinding system faces the abrasive nature of coal, which can quickly and seriously wear down conventional mills. The design of the vertical roller mill is carried out to handle tough conditions with high-pressure spring grinding mechanisms and durable wear-resistant construction, hence minimizing maintenance costs and extending operating life.
The application of coal in power generation has been continuously urged by the demand for energy, especially in the development of emerging economies. This demand has kept coal as a significant fuel and feedstock in various countries' energy mix despite the ongoing shift toward renewable energy. Therefore, there is continued strong demand for effective coal grinding solutions, such as vertical roller mills. With vertical roller mills allowing both economic and ecological advantages, they have become the most preferred choice for coal applications.
The Global Vertical Roller Mill Market Report is segmented on the basis of the following
By Product Type
- Spring Type
- Hydraulic Type
By Type
- Less Than 200t/h
- 200-400t/h
- More Than 400t/h
By Operation Mode
- Manual Operation
- Semi-Automatic Operation
- Fully Automatic Operation
By Application
- Coal Industry
- Slag Grinding
- Cement Industry
- Mining Industry
- Power Generation
- Chemical Industry
- Others
Regional Analysis
North America is projected to dominate the global vertical roller mill market as it
holds 36.2% of the total market revenue in 2024. North America holds the major share of the global vertical roller mill market, given the presence of a well-established industrial base, advanced infrastructure, and key market participants.
This demand has taken importance mainly in the mature manufacturing industry in this region, particularly that of the vertical roller mill, as industries from sectors such as cement, mining, and chemicals strive for efficient production and energy consumption.
In this respect, one of the main drivers toward North America's dominance appears to lie in the focus of the region on sustainability and ensuring energy efficiency. Both the United States and Canada have stern environmental policies that need to reduce carbon emissions from industrial processes.
Thus, vertical roller mills, which are famous for their energy-efficient grinding capabilities, come out to be an essential part of this transition. This necessity, especially for the cement and power generation industry, has accelerated the shift from using traditional ball mills to Vertical roller mills.
Moreover, North America has an excellent infrastructure and transport network that makes distribution and installation of vertical roller mills very easy in most industries of the region. The focus on technological innovation within the region has further resulted in more advanced VRM solutions, rounding out its leadership within the global landscape.
Besides this, massive infrastructure development investments across the U.S. have sustained demand for cement, a development that further accelerated the adoption of vertical roller mills in the region. With North America still keen on sustainable industrial growth, dominance in the vertical roller mill market is likely to prevail during the projection period.
By Region
North America
Europe
- Germany
- The U.K.
- France
- Italy
- Russia
- Spain
- Benelux
- Nordic
- Rest of Europe
Asia-Pacific
- China
- Japan
- South Korea
- India
- ANZ
- ASEAN
- Rest of Asia-Pacific
Latin America
- Brazil
- Mexico
- Argentina
- Colombia
- Rest of Latin America
Middle East & Africa
- Saudi Arabia
- UAE
- South Africa
- Israel
- Egypt
- Rest of MEA
Competitive Landscape
The competitive landscape of the global vertical roller mill market features key players competing for a greater share by practicing innovation as well as forging strategic alliances. Key companies dominating the market for vertical roller mills include Loesche, FLSmidth, Gebr. Pfeiffer, and Sinoma International Engineering, among others, have been offering a wide array of vertical roller mill solutions adapted by different industries. Companies are focused on the enhancement of efficiency in mill technology with a view to reducing energy consumption while extending its operational life.
While established players continue to dominate the market, a number of regional manufacturers are making their presence felt through the provision of cost-effective solutions and addressing the needs of local markets. Growing demand for customized Vertical Roller Mill solutions to suit specific industry applications such as cement, mining, and chemicals is further pushing up the competition.
Common strategies that leading companies adopt to increase their market share include mergers and acquisitions, partnerships, and joint ventures. Companies are, consequently, investing heavily in R&D to develop more energy-efficient and environmentally friendly vertical roller mills, befitting the global trend for green sustainability. A mix of new entrants and prevailing innovations by companies promises to keep the competition dynamic in the future.
Some of the prominent players in the Global Vertical Roller Mill Market are
- Loesche GmbH
- Gebr. Pfeiffer SE
- FLSmidth & Co. A/S
- ThyssenKrupp AG
- Metso Outotec
- Ecutec Barcelona S.L.
- Ube Machinery Corporation
- Fujian Longyi Powder Equipment Manufacturing Co. Ltd.
- Sinoma International Engineering Co. Ltd.
- Shibang Industry & Technology Group (SBM)
- CHAENG (Xinxiang Great Wall Machinery Corporation)
- NHI Group
- AMCL Machinery Limited
- Other Key Players
Recent Developments
- September 2023: FLSmidth unveiled its latest generation of the OK™ Mill, incorporating advanced technologies aimed at enhancing energy efficiency and reducing emissions. The new design features improved grinding mechanisms and an integrated digital control system that optimizes performance in real-time.
- July 2023: Gebr. Pfeiffer successfully commissioned an MVR vertical roller mill at a major cement plant in the Middle East. The mill is designed to handle high throughput rates and produce various cement types with minimal energy consumption.
- May 2023: Loesche announced the completion of VRM installations at a large coal-fired power plant in Asia. The mills are utilized for coal grinding, contributing to improved combustion efficiency and reduced emissions.
- March 2023: Sinoma International Engineering Co. secured a significant contract to supply multiple Vertical roller mills for a new cement production line in Africa. The project includes the provision of Vertical roller mills for raw materials, clinker, and coal grinding.
Report Details
Report Characteristics |
Market Size (2024) |
USD 608.5 Mn |
Forecast Value (2033) |
USD 1,041.2 Mn |
CAGR (2024-2033) |
6.1% |
Historical Data |
2018 – 2023 |
The US Market Size (2024) |
USD 185.3 Mn |
Forecast Data |
2025 – 2033 |
Base Year |
2023 |
Estimate Year |
2024 |
Report Coverage |
Market Revenue Estimation, Market Dynamics, Competitive Landscape, Growth Factors and etc. |
Segments Covered |
By Product Type (Spring Type, and Hydraulic Type
By Type (Less Than 200t/h, 200-400t/h, More Than 400t/h), By Operation Mode (Manual Operation, Semi-Automatic Operation, and Fully Automatic Operation), By Application (Coal Industry, Slag Grinding, Cement Industry, Mining Industry, Power Generation, Chemical Industry, and Others)
|
Regional Coverage |
North America – The US and Canada; Europe – Germany, The UK, France, Russia, Spain, Italy, Benelux, Nordic, & Rest of Europe; Asia- Pacific– China, Japan, South Korea, India, ANZ, ASEAN, Rest of APAC; Latin America – Brazil, Mexico, Argentina, Colombia, Rest of Latin America; Middle East & Africa – Saudi Arabia, UAE, South Africa, Turkey, Egypt, Israel, & Rest of MEA
|
Prominent Players |
Loesche GmbH, Gebr. Pfeiffer SE, FLSmidth & Co. A/S, ThyssenKrupp AG, Metso Outotec, Ecutec Barcelona S.L., Ube Machinery Corporation, Fujian Longyi Powder Equipment Manufacturing Co. Ltd., Sinoma International Engineering Co. Ltd., Shibang Industry & Technology Group (SBM), CHAENG (Xinxiang Great Wall Machinery Corporation), NHI Group, AMCL Machinery Limited, and Other Key Players |
Purchase Options |
We have three licenses to opt for: Single User License (Limited to 1 user), Multi-User License (Up to 5 Users) and Corporate Use License (Unlimited User) along with free report customization equivalent to 0 analyst working days, 3 analysts working days and 5 analysts working days respectively. |