Market Overview
The Global Medical Plastics Extrusion Market is projected to reach USD 921.7 million in 2025 and grow at a compound annual growth rate of 5.2% from there until 2034 to reach a value of USD 1,453.9 million.
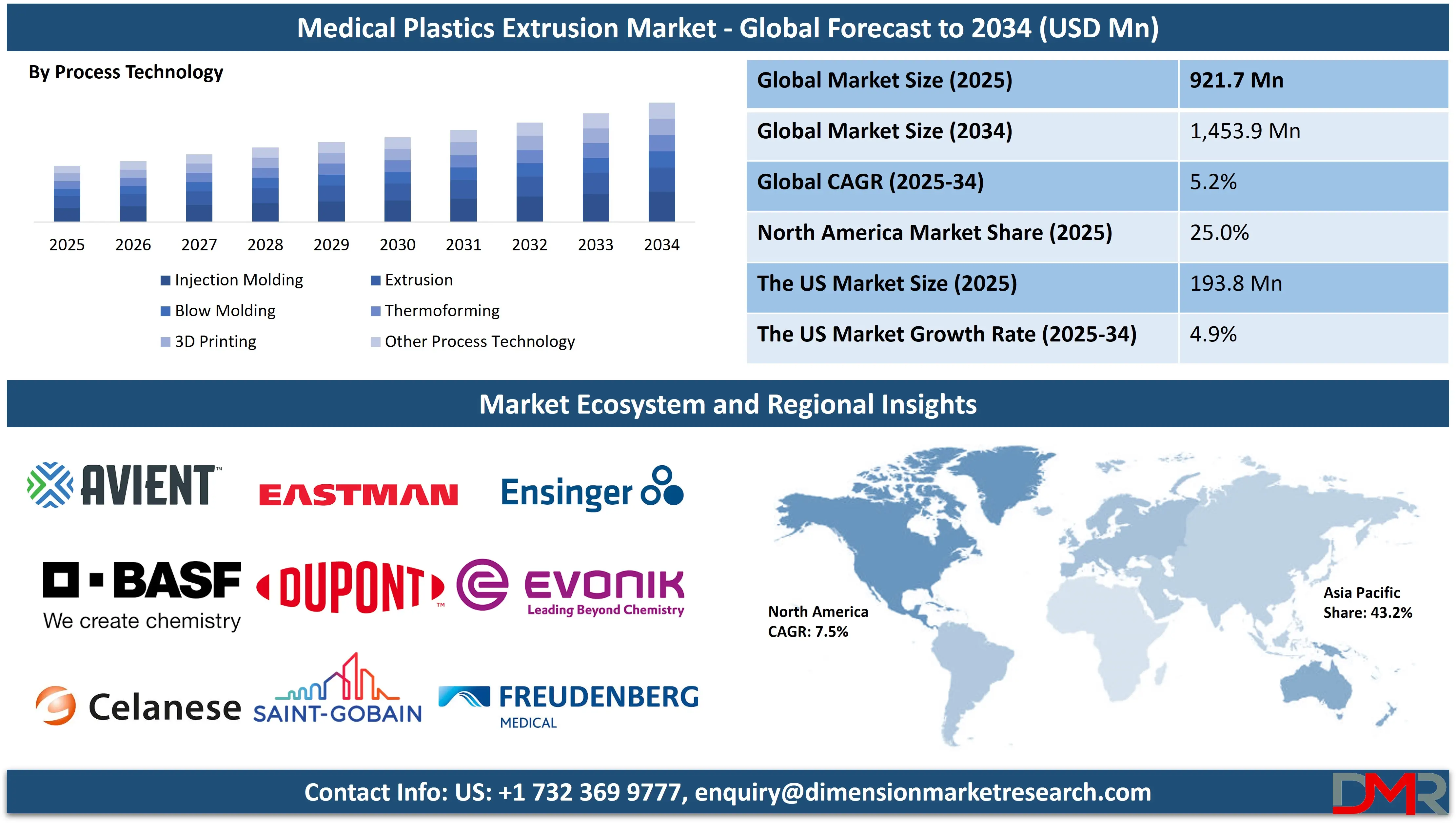
This market is witnessing significant momentum due to the surge in demand for lightweight, biocompatible, and sterilizable medical components, particularly in applications like catheter-based interventions, intravenous tubing, and diagnostic packaging. A key trend shaping this industry is the shift toward high-performance polymers, including polyetherimide (PEI), polyphenylsulfone (PPSU), and liquid crystal polymers (LCP), which offer exceptional heat resistance, chemical inertness, and strength for long-term implantable and single-use devices alike. At the same time, sustainability considerations are influencing both material selection and manufacturing techniques. Companies are increasingly adopting recyclable and PVC-free alternatives, alongside closed-loop extrusion systems to minimize medical plastic waste.
An expanding opportunity in this market lies in the adoption of extrusion technologies for minimally invasive and wearable healthcare devices. With healthcare increasingly shifting toward ambulatory and home-based care, there is a rising demand for flexible, kink-resistant extruded tubing, antimicrobial catheter sheaths, and disposable respiratory components. However, the market is not without challenges. Volatility in raw material pricing, especially for medical-grade polymers, and complex regulatory approvals across major markets such as the U.S., EU, and Japan pose barriers to smaller manufacturers.
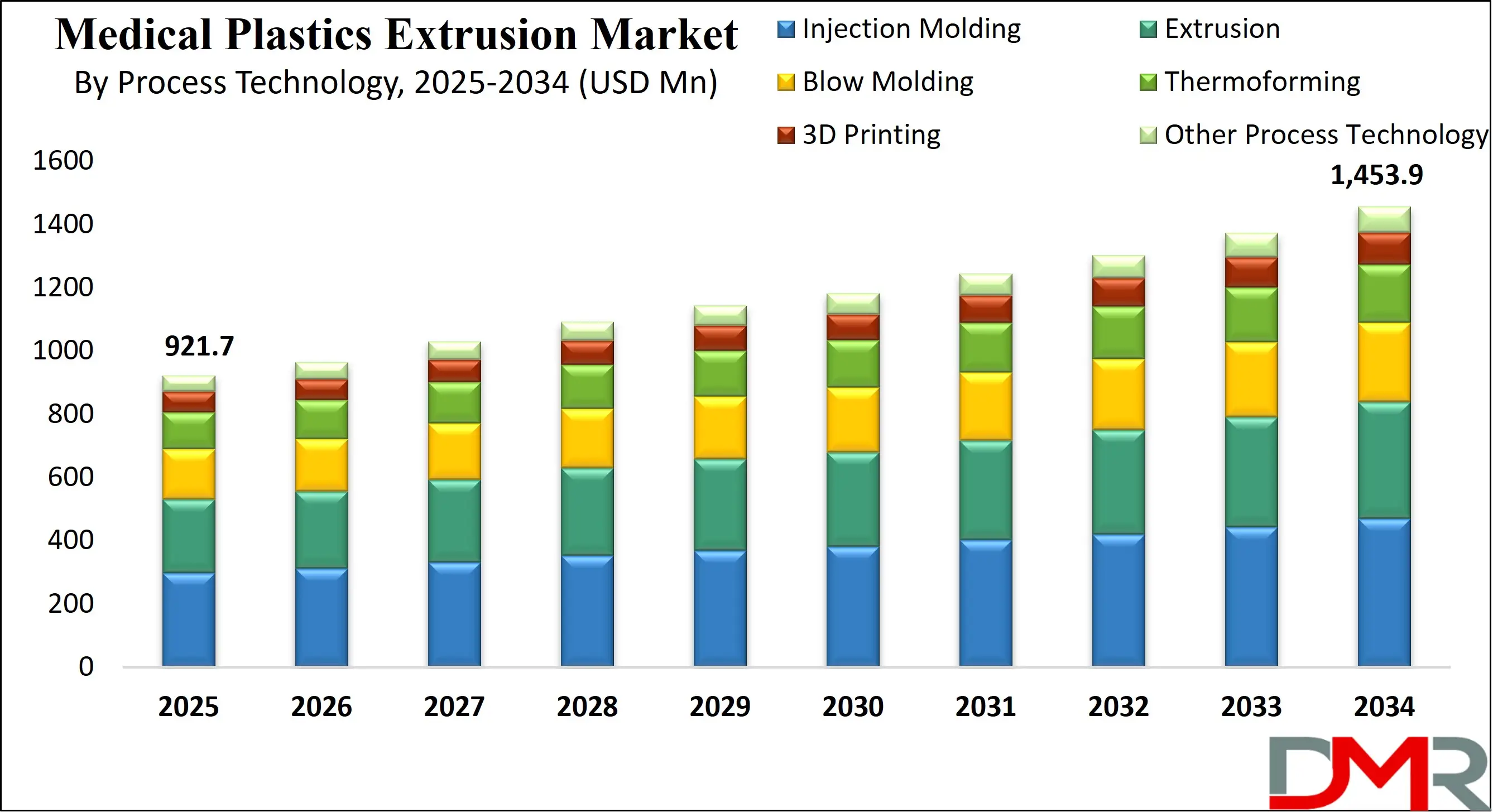
Nevertheless, with aging populations, the growing prevalence of chronic diseases, and the rise of home healthcare and telemedicine solutions, the medical plastics extrusion market holds substantial long-term growth potential across developed and emerging regions.
The US Medical Plastics Extrusion Market
The US Medical Plastics Extrusion Market is projected to reach USD 193.8 million in 2025 at a compound annual growth rate of 4.9% over its forecast period.
The market is underpinned by several strong demographic and structural advantages. According to the U.S. Census Bureau, more than 56 million Americans are aged 65 and older, a figure expected to grow rapidly by 2030. This aging population fuels demand for chronic care devices, including catheter systems, infusion tubing, respiratory aids, and orthopedic components, all of which depend on high-precision plastic extrusion.
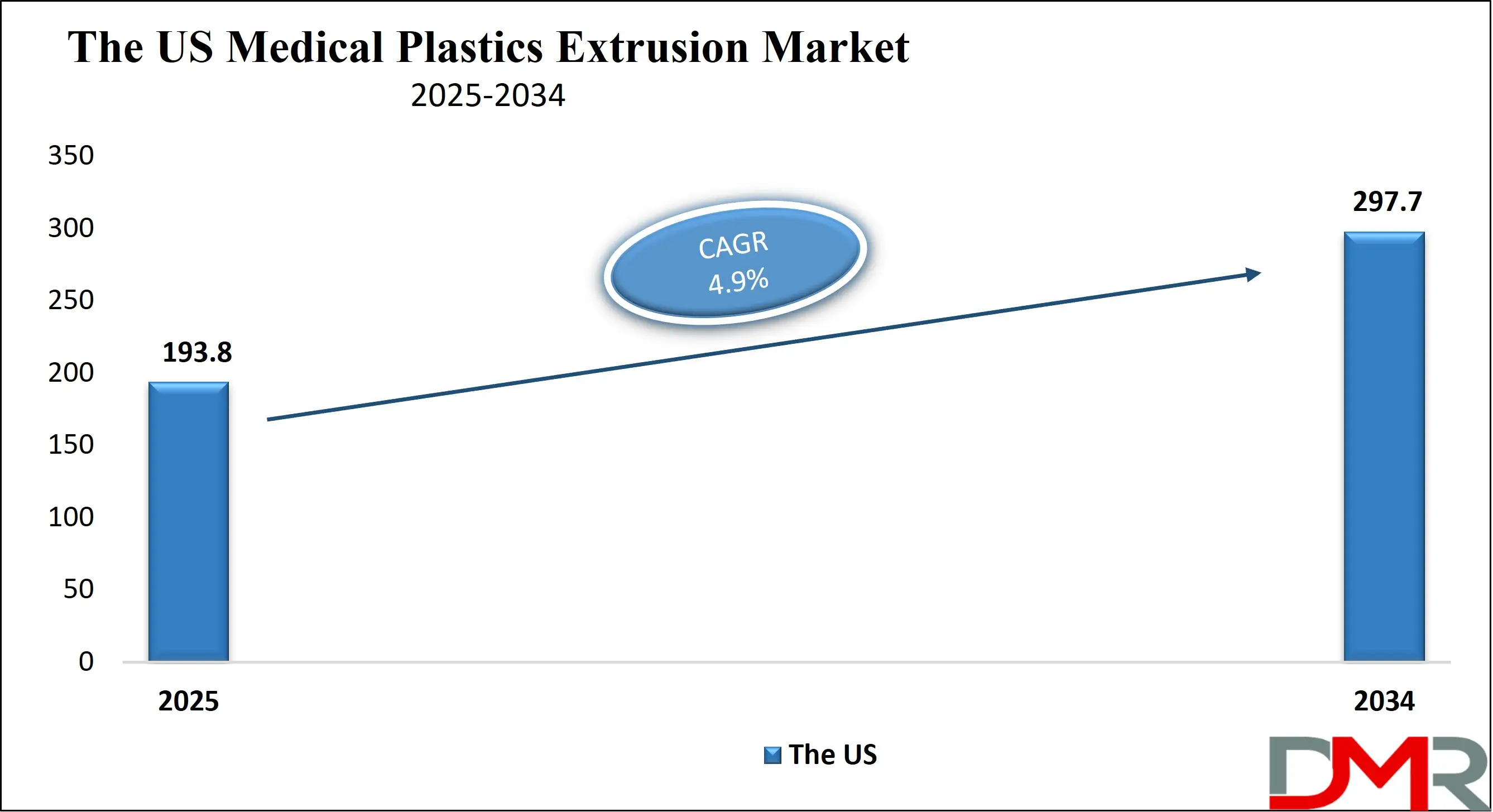
The U.S. healthcare ecosystem promotes a wide adoption of advanced medical technologies, supported by more than $30 billion in NIH funding annually and a high rate of device innovation. Medical extruders in the country benefit from proximity to major OEM hubs in states like Minnesota, California, and Massachusetts, along with a favorable environment for FDA-regulated contract manufacturing. The U.S. Food and Drug Administration (FDA) enforces strict guidance on biocompatibility and sterilization processes under its 21 CFR framework, ensuring that extruded materials meet rigorous standards.
Home healthcare is also accelerating market demand. As Medicare and Medicaid expand coverage for at-home treatments, the need for single-use IV lines, wound-care dressings, and assistive tubing is growing. In addition, U.S. manufacturing is supported by cleanroom infrastructure, MedAccred certifications, and vertically integrated supply chains that optimize consistency and traceability. This combination of demographic momentum, public health infrastructure, and innovation capacity secures the U.S. position as a global leader in the medical plastics extrusion industry.
The Europe Medical Plastics Extrusion Market
The Europe Medical Plastics Extrusion Market is estimated to be valued at USD 138.2 million in 2025 and is further anticipated to reach USD 198.0 million by 2034 at a CAGR of 4.0%.
The region's market is deeply influenced by demographic trends and a regulatory climate that supports quality and sustainability. According to Eurostat, over 21% of the EU population is aged 65 or older, creating a structural demand for chronic care solutions, mobility aids, wound dressings, and implantable medical components, all commonly produced via extrusion.
The European Union Medical Device Regulation (EU MDR) and ISO 13485 standards require manufacturers to demonstrate extensive validation of extrusion processes and polymer selection. This promotes the use of durable, sterilizable polymers such as PPSU, PC, and PEI in products ranging from catheters and drainage tubes to orthopedic packaging. Germany, France, and the Netherlands lead in medical device output, with strong infrastructure for precision extrusion and thermoforming.
EU sustainability policy is another key market driver. The European Commission’s Green Deal and Circular Economy Action Plan incentivize medical plastics recycling, while initiatives like the Single-Use Plastics Directive are pushing OEMs and extruders to switch from traditional PVC to eco-friendlier options like TPE and recyclable PETG. Healthcare systems across Europe also maintain a focus on universal access and in-home patient care, especially in Scandinavian countries.
This regulatory rigor, combined with mature public health systems, skilled technical labor, and an aging population, places Europe at the forefront of innovation in sustainable and high-quality medical plastics extrusion.
The Japan Medical Plastics Extrusion Market
The Japan Medical Plastics Extrusion Market is projected to be valued at USD 55.3 million in 2025. It is further expected to witness subsequent growth in the upcoming period, holding USD 80.7 million in 2034 at a CAGR of 4.3%.
The country’s rapidly aging population is a central growth factor. According to the Ministry of Internal Affairs and Communications, more than 28.9% of Japan’s population was aged 65 or older in 2024, the highest proportion globally. This demographic shift is intensifying demand for catheter-based procedures, home-use medical supplies, and wound care, all of which heavily rely on extruded polymer components.
Japan’s medical manufacturing ecosystem is built on precision, regulation, and material science leadership. The Pharmaceuticals and Medical Devices Agency (PMDA) maintains rigorous pre-market approval processes that emphasize material safety, sterilizability, and traceability. Japanese companies are known for their mastery of micro-extrusion, multi-lumen tubing, and polymer blends, enabling the production of high-precision products for cardiology, neurology, and nephrology.
Elder care infrastructure is also expanding, supported by government initiatives such as the “Community-based Integrated Care System,” which boosts demand for disposable respiratory masks, tubing for oxygen delivery, and other assistive technologies using extruded plastics. Japan’s Ministry of the Environment is concurrently pushing medical manufacturers to adopt circular design practices and explore the recycling of medical-grade plastics.
Combined with high health expenditure, a dense network of medical device manufacturers, and leading-edge R&D institutions, Japan’s market for medical plastics extrusion offers resilient and sophisticated growth, particularly in the segments of minimally invasive surgery, diagnostic equipment, and at-home healthcare delivery.
Global Medical Plastics Extrusion Market: Key Takeaways
- Global Market Size Insights: The Global Medical Plastics Extrusion Market size is estimated to have a value of USD 921.7 million in 2025 and is expected to reach USD 1,453.9 million by the end of 2034.
- The US Market Size Insights: The US Medical Plastics Extrusion Market is projected to be valued at USD 193.8 million in 2025. It is expected to witness subsequent growth in the upcoming period as it holds USD 297.7 million in 2034 at a CAGR of 4.9%.
- Regional Insights: Asia Pacific is expected to have the largest market share in the Global Medical Plastics Extrusion Market with a share of about 43.2% in 2025.
- Key Players: Some of the major key players in the Global Medical Plastics Extrusion Market are Avient Corporation, BASF SE, Celanese Corporation, DuPont de Nemours, Inc., Eastman Chemical Company, Ensinger GmbH, Evonik Industries AG, and many others.
- The Global Market Growth Rate: The market is growing at a CAGR of 5.2 percent over the forecasted period of 2025.
Global Medical Plastics Extrusion Market: Use Cases
- Catheters: Catheters represent one of the most critical and high-demand applications of medical plastics extrusion. Using advanced polymers like polyetherimide (PEI) and polyphenylsulfone (PPSU), manufacturers produce multi-lumen and micro-bore tubes essential in cardiovascular, urological, and neurological procedures. These catheters require ultra-thin walls for flexibility, kink resistance, and precision control during navigation inside the body.
- IV Sets and Tubing: Intravenous (IV) sets and associated tubing are fundamental to global healthcare delivery systems. Made predominantly from extruded polyethylene (PE) and polypropylene (PP), these tubes are used for the infusion of fluids, medications, and nutrients. The extrusion process enables the creation of consistent inner lumens to ensure uninterrupted flow, and surface-modification techniques improve biocompatibility and minimize the risk of clotting or infection.
- Surgical Trays: Surgical trays and instrument organizers are commonly made from thermoformed sheets of polycarbonate (PC) and polymethyl methacrylate (PMMA), both of which are extruded into large, clear, rigid panels before being molded into shape. These trays are essential for organizing surgical tools in sterile fields, providing visibility and protection during autoclaving, transport, and usage. PC offers impact resistance and heat tolerance, while PMMA contributes optical clarity.
- Orthopedic Implant Packaging: Medical packaging for orthopedic implants demands exceptional durability, barrier protection, and compliance with global sterilization standards. Multi-layer extrusion of high-performance plastics like polyphenylsulfone (PPSU) and polyethersulfone (PES) provides puncture resistance, thermal stability, and clarity for visual inspection. These films are often converted into pouches or rigid blisters for hip, knee, and spinal implants.
- Assistive Medical Devices: Assistive medical devices, particularly those used in long-term care and home health settings, frequently incorporate extruded components made from acrylonitrile butadiene styrene (ABS) and thermoplastic elastomers (TPE). These include parts for walkers, oxygen masks, grips, handles, and ventilator tubing. Extrusion provides precise dimensional control and ergonomic shaping for improved patient comfort and ease of use.
Global Medical Plastics Extrusion Market: Stats & Facts
Centers for Disease Control and Prevention (CDC)
The CDC, through its National Healthcare Safety Network (NHSN), gathers extensive data on healthcare-associated infections and medical device usage in the U.S.
- Over 38,000 hospitals, long-term care centers, and other healthcare facilities in the United States report device-associated infection data to the CDC via the NHSN.
- Catheter-associated urinary tract infections (CAUTIs) in adult inpatient units averaged 0.754 infections per 1,000 catheter-days in 2020, highlighting the importance of infection-resistant extruded catheter materials.
- In intensive care units (ICUs), CAUTI rates ranged from 1.2 to 4.5 per 1,000 catheter-days, while pediatric ICUs experienced CAUTI rates between 1.4 and 3.1 in the same metric.
- Midline catheters were linked to bloodstream infections at a rate of 0.8 per 1,000 catheter-days, underscoring the risk even in temporary use settings.
- Annually, approximately 1 million cases of CAUTIs occur in U.S. healthcare facilities, making these among the most prevalent hospital-acquired infections.
- The risk of bacteriuria during catheterization rises daily, with a 3% to 7% chance per catheter-day, depending on patient and facility conditions.
- In long-term care facilities, the CAUTI incidence rate averages around 3.2 infections per 1,000 catheter-days, further driving demand for safe, antimicrobial extruded products.
- Catheter-associated infections are responsible for up to 80% of all complicated urinary tract infections in the U.S., reinforcing the need for high-quality extruded catheter tubes.
CDC – Device Utilization and Infection Control
- The CDC’s NHSN also monitors the Standardized Utilization Ratio (SUR), a benchmarking metric comparing real-time central line, urinary catheter, and ventilator use to national historical baselines. This is used by hospitals to assess medical device usage patterns and optimize infection prevention strategies.
- Central-line associated bloodstream infections (CLABSIs), which are linked to prolonged catheter and tubing use, result in thousands of deaths annually in the U.S. and cost the healthcare system billions of dollars, underscoring the critical need for cleanroom-grade extruded tubing and packaging in device assembly.
Association of Medical Device Reprocessors (AMDR)
- The AMDR and affiliated public data sources reveal the growing impact of single-use device (SUD) reprocessing in reducing plastic medical waste and supporting circular economy practices in healthcare.
- Only around 2% of all single-use medical devices on the U.S. market are eligible for reprocessing by certified vendors, reflecting untapped potential for more sustainable material cycles.
- Reprocessing of SUDs in U.S. hospitals saved over USD 468 million in 2021 while diverting more than 20 million pounds of regulated medical waste from landfills.
- Globally, over 10,500 hospitals and surgical centers across North America, Europe, and Asia, including Japan, the UK, and Germany, actively use reprocessed medical devices, many of which originally involve plastic extrusion.
- A single hospital that reprocesses SUDs can eliminate 8,000 to 50,000 pounds of regulated medical waste every year, dramatically cutting disposal costs and landfill contributions.
- In 2021, more than 33 million medical devices were successfully reprocessed and reused, demonstrating the scalability of reuse protocols and the growing demand for polymer formulations that can withstand multiple sterilization cycles.
Environmental Impact and Plastic Recycling – Global and EU Data
- The healthcare sector accounts for approximately 5% of total global greenhouse gas emissions, a significant portion of which is linked to the use of plastics in disposable tubing, trays, packaging, and assistive devices. Extrusion processes that reduce scrap and enable recycling can play a pivotal role in improving this figure.
- Electrophysiology catheter remanufacturing, dependent on medical-grade extruded plastic components, can cut ozone-depleting emissions by as much as 90%, reduce overall climate-related emissions by over 50%, and decrease per-device lifecycle emissions by up to 48% when compared to new devices.
European Union Statistics – Eurostat & European Parliament
- Plastic packaging recycling rates in the European Union climbed to 40.7% in 2022, a marked improvement from 25.2% in 2005, indicating success in EU-wide efforts to shift toward circular packaging practices.
- In 2022, EU member states generated a combined total of 16.16 million metric tons of plastic packaging waste, equating to an average of 36.1 kilograms per person.
- The EU’s total waste generation per person in 2022 was about 186.5 kilograms, with plastics accounting for roughly 40% of all packaging waste.
- Marine litter analysis shows that around 50% of floating debris in EU coastal zones consists of plastic packaging, prompting reforms in medical product packaging design and materials.
- New EU waste regulations require that all packaging placed on the EU market must be recyclable by 2030, presenting both a challenge and a catalyst for innovation in recyclable extrusion-grade polymers.
- The European Parliament has mandated a 15% reduction in overall packaging waste by 2040, relative to 2018 levels. This is expected to drive demand for lightweight, low-impact extruded plastic materials.
- The average EU citizen now generates about 190 kilograms of packaging waste annually, reinforcing the urgency of waste reduction across sectors, including medical devices.
European Commission – Medical Device Regulation (MDR)
- Regulation (EU) 2017/745 on medical devices, which came fully into effect in May 2021, imposes stricter clinical evaluation and biocompatibility rules for all device components, including those made from extruded plastic. This regulation applies uniformly across all EU member states and is prompting a reevaluation of material selection and manufacturing practices.
Impact of Artificial Intelligence on the Global Medical Plastics Extrusion Market
- Enhanced Quality Control: AI-powered vision systems ensure real-time detection of defects during extrusion, minimizing human error. This results in consistently high-quality tubing and components essential for critical medical applications such as catheters and IV sets.
- Predictive Maintenance: AI enables predictive maintenance of extrusion equipment by analyzing sensor data to forecast potential failures. This reduces downtime, prolongs equipment lifespan, and ensures uninterrupted manufacturing of medical-grade plastic products.
- Process Optimization: Machine learning algorithms analyze production parameters to optimize extrusion speed, temperature, and pressure. This enhances material efficiency, reduces scrap, and ensures adherence to stringent medical-grade tolerance requirements.
- Customized Production: AI facilitates mass customization by adjusting extrusion parameters in real-time based on design inputs. This enables precise production of tailored medical devices like stents and surgical tubing with varying diameters and wall thicknesses.
- Supply Chain Forecasting: AI improves supply chain efficiency by accurately predicting demand, raw material needs, and delivery timelines. This reduces stockouts, improves responsiveness, and stabilizes production cycles for medical plastics extrusion companies.
- Regulatory Compliance Automation: AI tools streamline compliance by automatically documenting and analyzing production data for regulatory audits. This ensures adherence to global healthcare standards such as ISO 13485 and FDA regulations with minimal manual intervention.
Global Medical Plastics Extrusion Market: Market Dynamic
Driving Factors in the Global Medical Plastics Extrusion Market
Rising Geriatric Population and Chronic Disease Burden
The global rise in the geriatric population and associated chronic diseases is a significant driver of growth in the medical plastics extrusion market. According to the World Health Organization, the number of people aged 60 and older is expected to double by 2050, reaching over 2.1 billion. This demographic shift is closely tied to increased prevalence of chronic conditions such as cardiovascular disease, diabetes, and respiratory disorders, which require ongoing clinical intervention and frequent use of medical devices.
Products like intravenous (IV) lines, peripherally inserted central catheters (PICCs), drainage tubing, and respiratory circuits, largely made using precision plastic extrusion, are in constant demand across hospitals, home care, and ambulatory settings. Aging populations also lead to higher rates of surgeries, orthopedic implants, and rehabilitative services, all of which rely heavily on durable and sterilizable extruded plastic components.
Furthermore, long-term care and eldercare facilities are expanding globally, increasing the need for single-use, patient-friendly devices that reduce infection risks and improve treatment compliance. As healthcare systems shift toward value-based care, disposable extruded devices offer both economic and clinical advantages, including shorter hospital stays and reduced contamination. This convergence of demographic and health factors is steadily fueling demand for high-quality, precision-extruded tubing and profiles, positioning the segment for sustained long-term growth across developed and emerging markets alike.
Expansion of Home Healthcare and Wearable Medical Devices
The acceleration of home-based healthcare delivery and the rapid growth of wearable medical technologies are driving robust demand for extruded medical plastics. With healthcare systems aiming to reduce hospital overcrowding and costs, there has been a marked shift toward delivering treatment and monitoring outside traditional clinical settings. Extruded plastic tubing, connectors, and housing components are essential for home-use devices such as insulin pumps, oxygen concentrators, enteral feeding kits, and CPAP machines. These components must offer lightweight construction, flexibility, biocompatibility, and high dimensional precision to ensure safe and effective patient use. Concurrently, wearable medical devices such as biosensors, drug delivery patches, and flexible ECG monitors are integrating micro-extruded plastic channels and fluidic paths that support continuous diagnostics and drug transport.
Manufacturers are responding by developing ultra-small diameter extrusion lines capable of producing tubing with tight tolerances and multi-layer structures. These advances cater to the growing preference for minimally invasive, compact devices that improve patient mobility and adherence. Reimbursement models are also evolving to favor at-home treatments, especially in the U.S., Europe, and parts of Asia-Pacific, further accelerating demand. As telehealth expands and digital therapeutics become more prevalent, extrusion technology will play a central role in developing user-centric devices that combine functionality, comfort, and reliability for long-term, unsupervised use in home environments.
Restraints in the Global Medical Plastics Extrusion Market
Stringent Regulatory Compliance and Material Qualification
The highly regulated nature of the medical device industry presents a significant restraint on the growth of the plastics extrusion market. Medical-grade plastic components, especially those used in implantable or invasive devices, must undergo rigorous testing for biocompatibility, cytotoxicity, extractables/leachables, and sterilization compatibility under ISO 10993 and U.S. FDA 21 CFR Part 820 standards. These regulatory frameworks are continually evolving, and non-compliance can result in product recalls, import bans, or loss of certification. For extrusion companies, qualifying new materials such as novel blends of thermoplastics or recycled content polymers can take months or even years of clinical validation and shelf-life testing.
Additionally, the European Union’s MDR and IVDR regulations now require expanded technical documentation and post-market surveillance, increasing the compliance burden for suppliers. Smaller extrusion firms often lack the resources to maintain regulatory teams, navigate international quality systems, or conduct batch traceability for raw materials. Furthermore, cross-border regulations differ significantly between markets like the U.S., EU, Japan, and China, adding further complexity. As global scrutiny on device safety intensifies, especially post-pandemic, manufacturers face mounting pressure to deliver proven, auditable, and consistent extrusion outputs. While regulation protects patient safety, it also raises entry barriers for innovation and slows the commercialization of new extruded medical products.
Volatility in Raw Material Pricing and Supply Chain Disruptions
The medical plastics extrusion market is increasingly vulnerable to raw material price volatility and global supply chain instability, which constrain production planning and margin optimization. Key polymers used in extrusion, such as PE, PP, TPE, PEI, PPSU, and PC, are derived from petrochemicals, making them susceptible to fluctuations in crude oil prices, geopolitical disruptions, and refinery shutdowns. In recent years, global events such as the COVID-19 pandemic, the Russia-Ukraine conflict, and trade tensions have exacerbated supply shortages and led to erratic pricing in resin markets. In many cases, lead times for critical medical-grade compounds extended to 8–16 weeks, forcing manufacturers to delay production or resort to alternative materials, which then require regulatory requalification.
Additionally, transportation bottlenecks, port congestion, and labor shortages have further impacted the timely procurement of resins, additives, and packaging materials. Medical extrusion operations that rely on just-in-time (JIT) inventory models are especially affected by such uncertainties. Price hikes not only affect profitability but also complicate long-term pricing agreements with OEM clients, leading to potential contract losses or order deferrals. While large multinationals may mitigate risk through hedging or multiple sourcing, smaller firms face severe operational stress. The need for supply chain diversification, local sourcing, and raw material resilience has thus become a critical operational imperative for stakeholders in the medical plastics extrusion industry.
Opportunities in the Global Medical Plastics Extrusion Market
Emerging Markets and Healthcare Infrastructure Modernization
One of the most promising growth opportunities for the medical plastics extrusion market lies in the modernization of healthcare infrastructure across emerging markets. Countries in Asia-Pacific, Latin America, the Middle East, and parts of Africa are experiencing significant investments in healthcare access, equipment, and medical technology. Government-backed universal health coverage programs in nations such as India, Indonesia, and Brazil are expanding the availability of diagnostics, surgical procedures, and chronic disease management services, all of which require reliable and cost-effective medical disposables manufactured using plastic extrusion. The rise of public-private partnerships in these regions is further spurring local production capabilities and medical device manufacturing clusters.
In addition, foreign direct investment (FDI) incentives and relaxed import-export norms are enabling global medical device OEMs to set up manufacturing bases closer to demand hubs. Extruded products such as blood tubing, catheter systems, suction lines, and wound care strips are in high demand, particularly in rural and underserved areas. The adoption of locally extruded plastic components also reduces supply chain dependency and import costs. Companies that offer affordable, sterilizable, and high-quality extruded solutions tailored for regional regulatory requirements stand to capture significant market share. As these regions continue to urbanize and improve healthcare delivery, the demand for domestically manufactured medical plastics will offer sustained expansion opportunities through the next decade.
Customization and Miniaturization in Extrusion Technology
The rising trend toward personalized medicine and miniaturized medical devices is unlocking new opportunities for innovation in plastic extrusion technology. Healthcare systems increasingly demand patient-specific solutions such as tailored catheter lengths, unique geometries, and specialized flow-control components that improve procedural efficiency and clinical outcomes. Custom extrusion capabilities, including multi-lumen, tri-extrusion, and variable durometer profiles, are gaining prominence as OEMs seek to differentiate their offerings in niche clinical applications. At the same time, the demand for micro-extrusion producing tubing with outer diameters as small as 0.1 mm is surging in fields like neurovascular surgery, interventional cardiology, and ophthalmology. This level of precision is only possible with advanced tooling, real-time laser monitoring, and tight process control within Class 7 and 8 cleanroom environments.
Moreover, additive elements like antimicrobial agents and contrast-enhancing fillers can now be integrated directly into the extrusion process, providing value-added functionality and regulatory compliance. With the global shift toward minimally invasive procedures and wearable health monitoring devices, manufacturers who invest in sophisticated extrusion lines and engineering services will be well-positioned to capitalize on high-margin, specialty medical applications. Customization not only improves clinical relevance but also strengthens OEM partnerships and long-term supply agreements, making it a compelling growth frontier for extrusion suppliers seeking to move beyond commoditized offerings.
Trends in the Global Medical Plastics Extrusion Market
Integration of High-Performance Polymers in Medical Extrusion
A major trend transforming the medical plastics extrusion market is the growing integration of high-performance polymers such as polyphenylsulfone (PPSU), polyetherimide (PEI), and liquid crystal polymers (LCP). These advanced materials offer superior thermal resistance, chemical stability, and dimensional accuracy, making them ideal for minimally invasive devices and long-term implantable components.
The transition from conventional materials like PVC and polyethylene to these robust alternatives is driven by the demand for reliability in critical-care environments and the need to comply with stricter regulatory standards. Additionally, their compatibility with multiple sterilization techniques such as autoclaving, gamma irradiation, and ethylene oxide enhances their utility in modern healthcare. High-performance polymers are especially prevalent in neurovascular catheters, endoscopic tubing, and respiratory equipment that require precision micro-extrusion.
As surgical procedures shift toward smaller, more intricate devices, this trend is expected to intensify, promoting R&D in polymer blends, nanocomposites, and bioresorbable extrudates. Global healthcare providers, particularly in developed economies, increasingly prefer products with long-term stability and biocompatibility, further fueling demand for extrusion-grade specialty resins. Medical OEMs are partnering with polymer scientists and extrusion specialists to engineer new formulations tailored for use in cardiac, orthopedic, and diagnostic segments. This transition supports not only device functionality but also enhances global market competitiveness by ensuring superior patient outcomes, reduced infection risks, and improved material lifecycle performance.
Shift Toward PVC-Free and Sustainable Extrusion Materials
Environmental responsibility is emerging as a defining trend in the medical plastics extrusion market, with increasing emphasis on eliminating PVC and adopting sustainable material alternatives. Historically, PVC has been widely used for extruded medical products due to its flexibility and cost-effectiveness. However, concerns regarding phthalate plasticizers, dioxin emissions during incineration, and long-term toxicity have triggered regulatory action across major markets, particularly in Europe and North America.
The European Union's REACH regulation and the U.S. FDA's updated guidance on DEHP-free products have catalyzed a paradigm shift in materials selection for medical extrusions. Manufacturers are transitioning toward thermoplastic elastomers (TPEs), polyethylene terephthalate glycol (PETG), and bio-based polymers that offer similar mechanical properties with lower environmental and health risks.
This shift is influencing the entire extrusion ecosystem from compounders and toolmakers to device OEMs, leading to redesigns of existing products and accelerated innovation in recyclable materials.
In parallel, closed-loop production models and post-industrial recycling initiatives are gaining traction in the medical extrusion supply chain. Companies are investing in advanced screw designs, low-shear extruders, and precision dies to process sustainable resins efficiently while preserving material integrity.
As regulatory agencies, hospitals, and consumers advocate for low-carbon, toxin-free healthcare environments, the demand for PVC-free extrusion solutions will continue to gain momentum, ultimately reshaping procurement and production standards in the global medical device industry.
Global Medical Plastics Extrusion Market: Research Scope and Analysis
By Product Analysis
Polyethylene (PE) is projected to dominate the medical plastics extrusion market due to its exceptional versatility, cost-effectiveness, and biocompatibility, making it a preferred material for various disposable and long-term use medical devices. High-density polyethylene (HDPE) and low-density polyethylene (LDPE) variants offer unique advantages such as chemical resistance, high tensile strength, and good processability, allowing manufacturers to produce a wide range of extruded medical products, including tubing, catheters, IV lines, and fluid management components. PE’s flexibility and softness make it ideal for patient-contact applications, minimizing the risk of tissue irritation or injury. It is also widely accepted by regulatory bodies such as the U.S. FDA and conforms to USP Class VI biocompatibility standards, further facilitating its use in sterile and sensitive environments.
Additionally, PE’s ease of sterilization using methods such as ethylene oxide (EtO) and gamma radiation adds to its dominance, as most extruded medical components require stringent sterilization before patient use. The global drive for cost-efficient, high-volume production has also favored PE, which supports consistent extrusion at high throughput rates with minimal defects. Its recyclability and relatively lower environmental impact compared to PVC have increased its adoption in markets focused on sustainability.
Furthermore, its compatibility with multi-layer extrusion enables tailored barrier properties for advanced tubing systems. With wide application across medical device packaging, fluid transfer, and assistive care products, polyethylene remains the material of choice for both OEMs and contract manufacturers, maintaining its leadership in the product segment.
By Process Technology Analysis
Injection molding is anticipated to dominate the process technology segment in the medical plastics extrusion market due to its unmatched ability to mass-produce complex, high-precision plastic components with tight tolerances and excellent repeatability. Although extrusion is essential for producing continuous profiles like tubing and films, injection molding is the backbone of medical device production for discrete parts such as connectors, syringe plungers, catheter hubs, infusion ports, surgical handles, and housing components. It offers unparalleled design flexibility, enabling the creation of intricate geometries, undercuts, and integrated features that are difficult or impossible to achieve with other fabrication methods.
Another major advantage of injection molding is its scalability and cost efficiency in large production runs, which is critical in the medical sector where millions of parts are required for single-use and disposable applications. The ability to use a wide range of thermoplastics such as PE, PP, ABS, and advanced resins like PEI and PPSU further enhances its appeal. Modern injection molding machines offer Class 7 or Class 8 cleanroom compatibility, which is essential for contamination-sensitive applications. With advancements in multi-shot and micro-injection molding, the technology is also increasingly used to produce hybrid components that integrate soft-touch elastomers and rigid substrates in one mold.
Moreover, the precision, automation, and repeatability offered by injection molding reduce labor costs and human error, while ensuring regulatory compliance with ISO 13485 and FDA standards. These factors collectively position injection molding as the most dominant process technology, especially in the production of high-precision, functional medical device components.
By Application Analysis
Medical device packaging is expected to dominate the application segment of the medical plastics extrusion market due to the critical role it plays in ensuring product sterility, safety, compliance, and shelf-life stability. As healthcare facilities increasingly adopt single-use and pre-sterilized medical products, the demand for reliable, high-barrier, and contamination-resistant packaging has surged. Extruded plastic films and sheets, including multi-layer laminates made from materials like polyethylene (PE), polypropylene (PP), and polyesters, are integral to packaging solutions such as thermoformed trays, pouches, blister packs, and tubing wraps. These materials offer a strong balance of flexibility, puncture resistance, and clarity, making them ideal for storing and transporting surgical instruments, catheters, implants, and diagnostic tools.
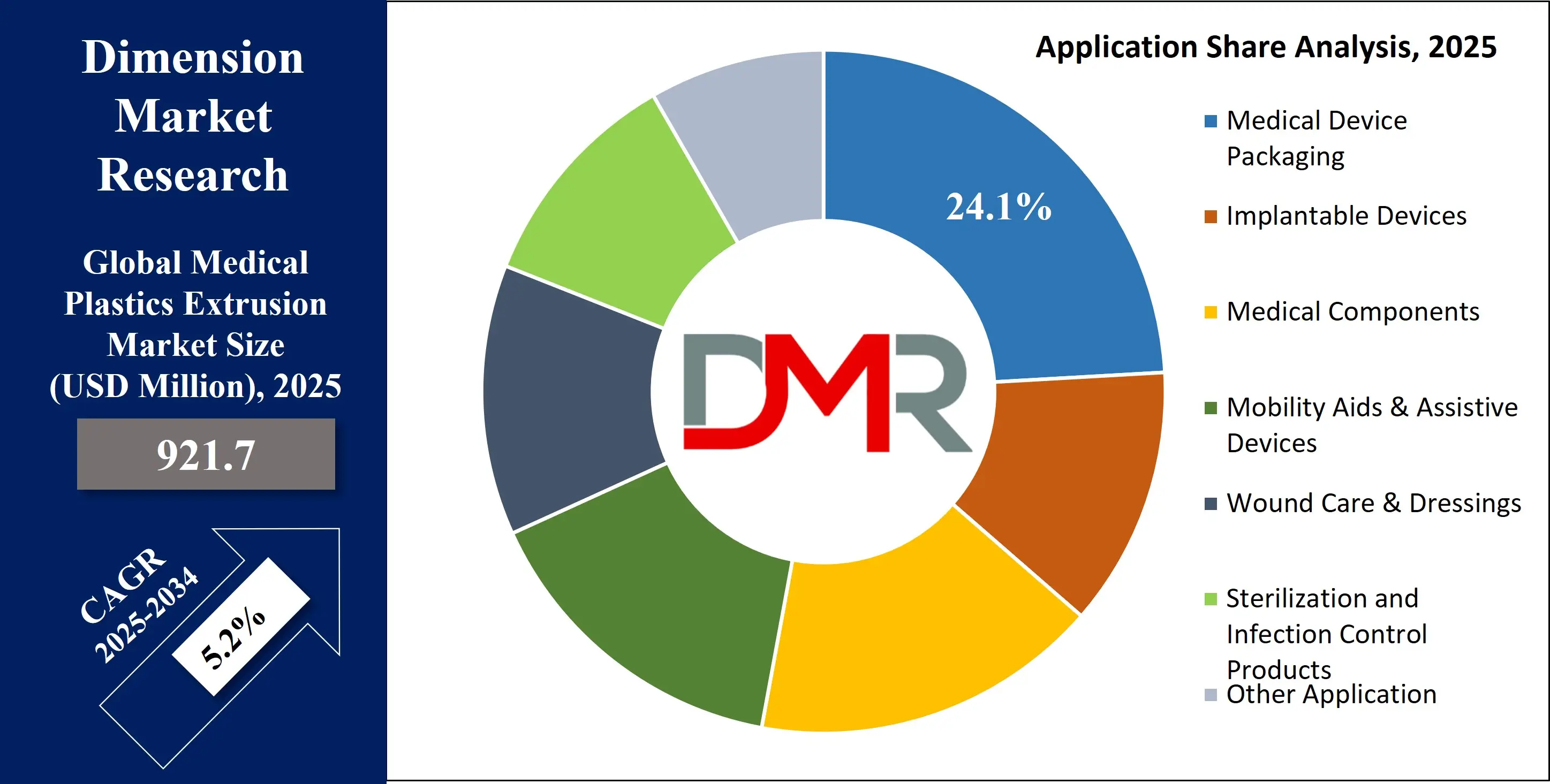
The dominance of this segment is further driven by stringent global regulations such as ISO 11607 and U.S. FDA Title 21 CFR that mandate sterility assurance and performance validation in medical packaging. Extrusion technology allows manufacturers to tailor barrier properties by adjusting layer thickness and integrating additives for antimicrobial or moisture resistance. Additionally, medical device packaging must endure multiple sterilization methods like gamma irradiation, EtO, or steam, and extruded materials offer the thermal and chemical resilience to meet these requirements.
With the rise of minimally invasive surgeries, aging populations, and an expanding outpatient sector, the volume and variety of packaged medical devices are increasing. Extrusion’s scalability, combined with growing demand for tamper-evident and tamper-proof packaging, ensures medical device packaging remains the dominant application area in this evolving and safety-centric market.
The Global Medical Plastics Extrusion Market Report is segmented on the basis of the following
By Product
- Polyethylene (PE)
- Polypropylene (PP)
- Polycarbonate (PC)
- Polyetherimide (PEI)
- Polymethyl Methacrylate (PMMA)
- Polyphenylsulfone (PPSU)
- Polyethersulfone (PES)
- Liquid Crystal Polymer (LCP)
- Acrylonitrile Butadiene Styrene (ABS)
- Others
By Process Technology
- Injection Molding
- Extrusion
- Blow Molding
- Thermoforming
- 3D Printing
- Other Process Technology
By Application
- Medical Device Packaging
- Implantable Devices
- Tooth Implants
- Denture Base Material
- Orthopedic Implants
- Medical Components
- Mobility Aids & Assistive Devices
- Wound Care & Dressings
- Sterilization and Infection Control Products
- Other Application
Global Medical Plastics Extrusion Market: Regional Analysis
Region with the Largest Revenue Share
Asia-Pacific is projected to hold the dominant share in the global medical plastics extrusion market as it commands over 43.2% of the total revenue by the end of 2025, due to its vast manufacturing capacity, cost-effective production base, and rising healthcare infrastructure. Countries such as China, India, Japan, and South Korea have become global hubs for medical device manufacturing, supported by government incentives, rising FDI, and a skilled labor force. China’s “Made in China 2025” initiative and India’s “Make in India” scheme have accelerated investments in medical device parks and polymer extrusion technologies.

In addition, the growing middle-class population, rapid urbanization, and increasing public health expenditure have created strong domestic demand for affordable, high-quality medical consumables such as IV tubing, catheters, and wound dressings, many of which are produced using plastic extrusion. Japan’s advanced regulatory standards and innovation in minimally invasive surgical tools have further bolstered the region’s technological capabilities in extrusion-grade materials. Moreover, the region’s raw material availability and proximity to petrochemical suppliers offer cost advantages in resin procurement. The abundance of OEMs, local contract manufacturers, and expanding export-oriented facilities has enabled Asia-Pacific to outpace other regions in both volume and technological advancement in the medical plastics extrusion landscape.
Region with the Highest CAGR
North America is expected to register the highest CAGR in the medical plastics extrusion market owing to rising innovation in advanced medical devices, increased adoption of home healthcare technologies, and regulatory reforms favoring localized production. The U.S. leads in R&D investments for specialized medical tubing, micro-extrusion, and high-performance polymers, particularly for neurovascular, cardiovascular, and minimally invasive procedures. The growing geriatric population and high incidence of chronic diseases are driving demand for single-use and patient-centric medical devices that rely heavily on precision-extruded components.
In addition, the region is witnessing a shift toward PVC-free and sustainable materials, pushing manufacturers to invest in next-gen extrusion lines and recyclable polymers. The U.S. FDA’s push for enhanced sterilization and material traceability also contributes to the regional growth momentum. Furthermore, reshoring trends, supply chain diversification, and government-backed incentives under the Inflation Reduction Act are encouraging local production, making North America a fast-growing region despite its relatively mature market base.
By Region
North America
Europe
- Germany
- The U.K.
- France
- Italy
- Russia
- Spain
- Benelux
- Nordic
- Rest of Europe
Asia-Pacific
- China
- Japan
- South Korea
- India
- ANZ
- ASEAN
- Rest of Asia-Pacific
Latin America
- Brazil
- Mexico
- Argentina
- Colombia
- Rest of Latin America
Middle East & Africa
- Saudi Arabia
- UAE
- South Africa
- Israel
- Egypt
- Rest of MEA
Global Medical Plastics Extrusion Market: Competitive Landscape
The global medical plastics extrusion market is highly competitive, characterized by a mix of multinational corporations, regional manufacturers, and specialized extrusion firms focusing on cleanroom-grade production. Leading companies such as Tekni-Plex, Spectrum Plastics Group (a DuPont Business), and Freudenberg Medical dominate through their vertically integrated operations, proprietary polymer formulations, and expertise in complex multi-lumen and micro-extrusion. These firms are heavily invested in Class 7 and Class 8 cleanroom facilities and offer full-service solutions from polymer compounding to finished components.
Smaller yet agile players such as Putnam Plastics, Zeus Industrial Products, and Microspec Corporation specialize in high-precision, low-volume custom extrusions for niche applications like neurovascular catheters and implantable devices. Strategic acquisitions, such as DuPont’s acquisition of Spectrum or Nordson Corporation’s past acquisitions, indicate increasing consolidation in the market. Innovation in antimicrobial additives, bioresorbable materials, and hybrid extrusion technologies is driving competitive differentiation.
Moreover, players are aligning with environmental goals by offering PVC-free alternatives and recyclable extrudates. Competitive advantages are defined by regulatory compliance, material science innovation, cleanroom manufacturing capabilities, and global distribution reach, enabling companies to serve OEMs across high-demand segments such as diagnostics, surgery, and chronic disease management.
Some of the prominent players in the Global Medical Plastics Extrusion Market are
- Avient Corporation
- BASF SE
- Celanese Corporation
- DuPont de Nemours, Inc.
- Eastman Chemical Company
- Ensinger GmbH
- Evonik Industries AG
- Freudenberg Medical
- GW Plastics (Now part of Nolato Group)
- Lubrizol Life Science Health (LLS Health)
- Medtronic plc
- Nordson Corporation
- Pexco LLC (Spectrum Plastics Group)
- Raumedic AG
- Saint-Gobain Performance Plastics
- SABIC
- Solvay S.A.
- TE Connectivity
- Teleflex Incorporated
- Zeus Industrial Products, Inc.
- Other Key Players
Recent Developments in the Global Medical Plastics Extrusion Market
- June 2025: The Middle East Compound & Extrusion Expo (MCEE) 2025 took place in Sharjah, UAE, drawing global attention to the evolution of extrusion and compounding technologies relevant to the medical sector. The event focused on sustainable extrusion, polymer purity, and automation in Class 8 cleanroom extrusion lines. Key themes included the integration of antimicrobial polymers and the shift away from PVC in medical tubing. Stakeholders from Saudi Arabia, the UAE, and India explored collaborations for localizing medical polymer supply chains in the Gulf region.
- May 2025: Two major events shaped the market: the Compounding World Expo and Plastics Recycling World Expo – India Edition, launched in Mumbai, emphasized innovations in polymer sustainability and extrusion tailored for high-volume, precision medical applications. Exhibitors showcased next-gen single-screw and twin-screw extruders with enhanced process control for thermoplastics like PE, PP, and PEI. Meanwhile, the Med-Tech Innovation Expo 2025 in Birmingham, UK, saw leading medical plastics players exhibit new extruded products for IV systems, catheters, and surgical packaging.
- May 2025: Plastasia 2025, hosted in Bangalore, India, attracted attention from regional and global companies involved in extrusion equipment and medical polymer production. Supported by India’s Ministry of Chemicals & Petrochemicals, the event served as a platform to announce investments in new medical extrusion facilities. Local manufacturers revealed joint ventures with European firms to transfer high-speed extrusion line technology to India.
- April 2025: At CHINAPLAS 2025 in Shenzhen, China, the medical plastics segment witnessed a major spotlight under the Extrusion Machinery Zone. The event showcased real-time controlled micro-extrusion lines capable of producing ultra-thin, multi-lumen tubing for neurovascular and cardiovascular applications. Chinese OEMs and international players from Japan and Germany presented joint research in bioresorbable extrusion and solvent-free coating techniques for implantable extruded parts.
- March 2024: AMI International, a recognized leader in industry events and intelligence, announced the launch of Compounding World Expo and Plastics Recycling Expo India 2025, reinforcing the region’s growing strategic role in global extrusion. The announcement underlined the Indian subcontinent's surge in extrusion-related investment, particularly for medical applications such as fluid delivery systems and sterilization-grade packaging films.
Report Details
Report Characteristics |
Market Size (2025) |
USD 921.7 Mn |
Forecast Value (2034) |
USD 1,453.9 Mn |
CAGR (2025–2034) |
5.2% |
Historical Data |
2019 – 2024 |
The US Market Size (2025) |
USD 193.8 Mn |
Forecast Data |
2025 – 2033 |
Base Year |
2024 |
Estimate Year |
2025 |
Report Coverage |
Market Revenue Estimation, Market Dynamics, Competitive Landscape, Growth Factors, etc. |
Segments Covered |
By Product (Polyethylene (PE), Polypropylene (PP), Polycarbonate (PC), Polyetherimide (PEI), Polymethyl Methacrylate (PMMA), Polyphenylsulfone (PPSU), Polyethersulfone (PES), Liquid Crystal Polymer (LCP), Acrylonitrile Butadiene Styrene (ABS), Others), By Process Technology (Injection Molding, Extrusion, Blow Molding, Thermoforming, 3D Printing, Other Process Technology), By Application (Medical Device Packaging, Implantable Devices, Medical Components, Mobility Aids & Assistive Devices, Wound Care & Dressings, Sterilization and Infection Control Products, Other Application) |
Regional Coverage |
North America – US, Canada;
Europe – Germany, UK, France, Russia, Spain, Italy, Benelux, Nordic, Rest of Europe;
Asia-Pacific – China, Japan, South Korea, India, ANZ, ASEAN, Rest of APAC;
Latin America – Brazil, Mexico, Argentina, Colombia, Rest of Latin America;
Middle East & Africa – Saudi Arabia, UAE, South Africa, Turkey, Egypt, Israel, Rest of MEA
|
Prominent Players |
Avient Corporation, BASF SE, Celanese Corporation, DuPont de Nemours, Inc., Eastman Chemical Company, Ensinger GmbH, Evonik Industries AG, Freudenberg Medical LLC, GW Plastics Inc., Lubrizol Life Science Health,Medtronic plc, Nordson Corporation, Pexco LLC, Raumedic AG, Saint-Gobain Performance Plastics Corporation, Saudi Basic Industries Corporation (SABIC), Solvay S.A., TE Connectivity Ltd., Teleflex Incorporated, and Zeus Industrial Products, Inc., and Other Key Players |
Purchase Options |
We have three licenses to opt for: Single User License (Limited to 1 user),
Multi-User License (Up to 5 Users), and
Corporate Use License (Unlimited User) along with free report customization equivalent to
0 analyst working days, 3 analysts working days, and 5 analysts working days respectively.
|
Frequently Asked Questions
The Global Medical Plastics Extrusion Market size is estimated to have a value of USD 921.7 million in
2025 and is expected to reach USD 1,453.9 million by the end of 2034.
Asia Pacific has the largest market share for the Global Medical Plastics Extrusion Market with a share of
about 41.4% in 2023.
Some of the major key players in the Global Medical Plastics Extrusion Market are GSH Industries,
Nenplas Ltd, Saint Gobain, and many others.
The market is growing at a CAGR of 4.5 percent over the forecasted period.