The growth of the South Korean warehousing market is impelled by the expansion of e-commerce, globalization of supply chains, and growing demand for third-party logistics services. At the center of the Asia-Pacific region, South Korea is strategically positioned equivalent in distance to major economies such as China and Japan, with world-class ports at Busan and Incheon, making it relevantly crucial in today's global trade and logistics.
The overall market reflects the growing demand for effective and technologically advanced warehousing solutions. Automation and Intelligent
warehouse systems are picking up a fast pace, wherein companies like CJ Logistics and Lotte Global Logistics integrate robotics, AI, and IoT technologies to further facilitate operational efficiency and provide value enhancement in inventory management while cutting costs.
This becomes particularly critical in the context of the fast growth of e-commerce, wherein fast delivery times and efficiency in logistics operations are keys to continuing the edge in the marketplace. Another factor that has contributed to this development in the warehouse market of South Korea is the demand for Cold Chain logistics impelled by the pharmaceutical, food, and
biotechnology sectors. This demand for temperature-controlled warehousing solutions has mobilized the key players in developing relevant infrastructure capacity to meet this emerging demand segment.
Private warehousing has been the most flexible and, because of a general move in-house for control of supply chains, increasingly preferred. General warehousing types remain the most prevalent and include added-value services such as cross-docking, inventory management, and order picking, catering for different industry verticals.
The market is likely to record significant growth over the forecast period due to technological advancements, growth of
e-commerce, and an increased demand for effective warehouse management and logistics services across industries.
South Korea Warehousing Market Key Takeaways
- Market Value: The South Korea Warehousing Market size is estimated to have a value of USD 47.9 billion in 2024 and is expected to reach USD 86.3 billion by the end of 2033.
- By Warehousing Technology Segment Analysis: Semi-automated warehouses are projected to dominate this segment as they holds 49.9% of the market share in this market in 2024.
- By Ownership Segment Analysis: Private Warehouses are projected to dominate this market in the ownership segment they hold the highest market share in 2024.
- By Industry Vertical Segment Analysis: E-commerce is anticipated in this segment as it will hold 27.1% of the market share by the end of 2024.
- Key Players: Some of the major key players in the South Korean warehousing Market are CJ Logistics Corporation, Pantos Logistics, DSV, Kuehne + Nagel, Toll Holdings Limited, Hyundai Glovis, LS Networks, DB Schenker, and many others.
- Growth Rate: The market is growing at a CAGR of 6.8 percent over the forecasted period.
South Korea Warehousing Market Use Cases
- E-commerce Fulfillment Centers: Coupang's warehouses ensure swift and appropriate order processing, inventory management, and last-mile delivery for e-commerce sites all over South Korea.
- Cold Chain Logistics: Temperature-controlled warehouses store perishable consignments of pharmaceuticals and fresh produce, before distribution in industries such as healthcare and food.
- Third-Party Logistics (3PL): Business firms outsource their logistics functions to companies like CJ Logistics for warehousing and distribution services at low costs in their supply chains across manifold industries.
- Cross-border Trade: The warehouses at the ports, for example, in Incheon, participate in the importation, and warehousing of merchandise for a short period, and clearing customs for further efficient distribution within South Korea and other neighboring countries.
- Supply Chain Automotive: Warehouses of automotive spare parts help manufacturers like Hyundai function on time due to the appropriate delivery of their components to the assembly lines. This helps in smooth operations and reduces factory downtimes.
South Korea Warehousing Market Dynamic
Trends
Shift Toward Automation and AI Integrationone of the key emerging trends in the South Korean warehousing market is greater integration of automation and/or AI into warehouse operations. With the emergence of smart warehouses, logistics companies like CJ Logistics and Lotte Global Logistics are adopting automated guided vehicle technologies, robotic arms, and AI-enabled inventory management systems to derive greater efficiency and operational cost reduction.
This is in tune with South Korea's broader push towards the digital transformation of industries, driven both by government incentives and by market competition.
Growth of Cross-border E-commerce
While the e-commerce sector in South Korea grows, the need for cross-border logistics solutions keeps growing. E-commerce giants such as Coupang and Amazon increasingly look at South Korea as a central hub for Asia-Pacific operations. Increased cross-border e-commerce gave an upward SPIP to developments dealing in warehousing services for international goods, guaranteeing smooth customs clearance and efficient delivery.
It is thus encouraging demand for bonded and specialized e-commerce fulfillment facilities in key logistics hubs such as Busan and Incheon.
Growth Drivers
Boom in E-commerce and Consumer Preferences
The spiraling growth of e-commerce in South Korea has been one of the key drivers in the warehousing market. Online platforms such as 11Street, Gmarket, and Coupang are meeting increasing consumer demand for quicker delivery times, wider product choices, and ease of return. This change in consumer behavior forced e-commerce companies to invest heavily in warehousing solutions that supported order fulfillment, inventory management, and last-mile delivery.
South Korea’s Strategic Geographic Location
South Korea is positioned so strategically that it has gained a leading position as a hub of logistics in the region of the Asia-Pacific, thereby developing into a forthcoming market with international trade. All this puts it near major markets in China, Japan, and Southeast Asia, with world-class ports in both Busan and Incheon-developing an important node in global supply chains.
The geographical advantage imbued by this fact significantly drives international trade and the growing demand for large-scale warehousing facilities capable of handling domestic distribution and international shipment. Hyundai Glovis and Hanjin Transportation Company are listed firms that have managed to gain from this growth.
Growth Opportunities
Cold Chain Warehousing Expansion
The increasing demand for temperature-controlled storage provides a very good avenue of growth in the warehousing market of South Korea. Sectors such as pharmaceuticals, biotechnology, and food products demand highly specialized cold storage facilities.
Companies like CJ Logistics are making considerable investments in cold chain infrastructure to support the emerging demand for perishable products in the food and vaccine sectors. The cold chain market also proliferates with an expansion in industries like healthcare and biotech, presenting new opportunities for logistics providers as well.
Growth of Third-Party Logistics (3PL) Providers
Logistics services are increasingly outsourced to third-party logistics providers, offering a great avenue for growth. Companies manufacturing electronics, automotive, and consumer goods, among others, increasingly use 3PL services to streamline their supply chain for reduced operational costs and a focus on core business activities.
Major companies such as CJ Logistics and Lotte Global Logistics have expanded their services in 3PL, warehousing, distribution, and end-to-end supply chain management. This would further boost the market during the forecast period.
Restraints
Rising Logistics Costs
The growing cost of logistics is one of the key challenges faced by the warehousing market in South Korea. This is attributed to skyrocketing real estate prices in major metropolis areas such as Seoul and Busan. In addition, labor costs keep on growing, and investment in new automation technologies contributes substantially to the overall spending for logistics companies. These developing expenses are a huge obstacle for smaller-sized and middle-sized companies that wish to expand their warehousing.
Limited Availability of Land in Urban Areas
It is constrained by the market because of the limited available land in urban areas for warehousing. The city of Seoul has rapidly urbanized, and the space for warehousing has become very limited. This raises the cost of leasing or buying warehouse property, especially those that are considered primary locations near last-mile operations. Thus, companies can invest only in either smaller but efficient warehouse designs or look out for opportunities in less central areas. It does tend to have consequences on their overall operating efficiency.
South Korea Warehousing Market Research Scope and Analysis
By Warehousing Type
General warehousing is projected to lead the segment of warehousing type in the South Korean market due to its adaptability to a broad range of industries. In contrast to the specialized warehouses serving such niches as cold storage or bonded goods, the general warehouses have been built to serve several product types, from consumer goods to electronics and industrial components.
This warehousing diversity makes general warehousing attractive to retail, manufacturing, and e-commerce companies that have wide-ranging inventory needs and call for flexible means. Among the reasons that place general warehousing at the top is the ability to take care of fluctuating levels concerning stocks of goods.
Indeed, many businesses, especially those dealing with e-commerce and retail, experience seasonal peaks in demand, and general warehouses offer flexibility to scale up or down depending on the business cycle. Companies like CJ Logistics and Lotte Global Logistics remain at the forefront of general warehousing services within South Korea, leveraging their ability to craft customizable solutions that meet dynamic client needs.
Apart from that, general warehouses usually serve as the backbone for the operation of third-party logistics. The 3PL service providers, such as Hyundai Glovis, utilize these houses to manage several clients' supply chains because they act like a central hub in storing, managing inventories, and distribution. Cost-effectiveness and operational flexibility make general warehousing dominant in the choice of logistics industries in South Korea because logistics support both domestic and international supply chains.
By Warehousing Technology
Semi-automated warehouses are projected to be dominant in the South Korean warehousing market as they hold 49.9% of the market share in 2024. Semi-automated warehouses are dominant in the market of South Korea because they deliver an optimal balance between cost and efficiency of operations.
Full automation of warehousing operations requires immense investments in advanced robotics and infrastructure, which might be unaffordable for most business types. Nevertheless, semiautomatic systems, like automated guided vehicles (AGVs), conveyor belts, and automated storage and retrieval systems (AS/RS), are much more affordable yet highly efficient solutions that reduce manual labor. Companies like CJ Logistics and Lotte Global Logistics have adopted semiautomatic technologies with productivity gains while sacrificing little in flexibility in handling goods.
These systems can be leveraged by warehouses to improve throughput and make better use of space without necessarily changing operational infrastructure. For example, semi-automated solutions provide speedier order picking and packing processes, which are so crucial in e-commerce, where swift turnarounds are a must.
Another important reason for this dominance deals with adaptability. Whereas a fully automated system may be designed for specific types of products or operations, semi-automated systems can easily integrate with the existing warehousing environment and handle a range of products. The reason is, that this makes them extremely useful for companies involved in various product portfolios-such as Samsung or LG that need flexibility in storage and inventory management.
Their ability to continue competing in the rapidly developing logistics environment will require that they be converted to semi-automated systems.
By Ownership Type
Private Warehouses are projected to dominate the South Korean warehousing market in terms of ownership type as they hold the highest market share in 2024. Companies owning private warehouses can tailor the space to meet their specific needs, whether that involves specialized equipment for the handling of goods, dedicated temperature control for sensitive products, or secure storage for high-value inventory.
This will be especially useful for large companies like Samsung and Hyundai, whose supply chains are complex and require logistic processes to be aligned with the overall business strategy. Private warehouses also provide companies with flexibility in the location optimization of their facilities. Many companies have private warehouses strategically located near the manufacturing plants or, in the case of Seoul, other major urban conglomerates to cut down on transport costs and help raise delivery times.
Hyundai Glovis currently operates several private warehouses located opportunistically close to key production facilities to ensure smooth supply chain management for the automotive giant.
Private warehouses can give a company an avenue to improve data security and control over inventory management systems.
Private warehouses would provide a security environment for industries-for example, electronic, automotive, and pharmaceuticals-that cannot be provided by either public or third-party warehouses, for which security in terms of protection of intellectual property and sensitive information is highly crucial. This will consequently allow the companies to have full ownership and install proprietary systems that will track, manage, and distribute the goods efficiently in terms of operational efficiency and security along the value chain.
By Industry Vertical
E-commerce is anticipated to emerge as the dominant industry vertical in South Korea’s warehousing market as it will hold 27.1% of the market share by the end of 2024. E-commerce became the leading industry vertical in the warehousing market of South Korea with the unprecedented growth of online retail. Major companies in this market such as Coupang, eBay Korea, and 11Street catalyzed the demand for large-area and efficient warehousing infrastructure to manage huge volumes of inventory.
The shift in consumer preference for online shopping has, therefore, accelerated demand for warehousing solutions that could accommodate fast-moving goods and make the product delivery process quick after the COVID-19 pandemic. E-commerce warehouses need to be very different from the traditional models of warehousing, as there is a greater need for enhanced systems with regard to order processing, tracking inventory, and managing last-mile delivery.
Large companies such as CJ Logistics and Lotte Global Logistics have constructed special e-commerce fulfillment centers, each with automated sorting and packing systems that can handle hundreds of thousands of orders each day. Such fulfillment centers are in a position to play a critical role in catering to growing consumer demand for same-day and next-day delivery services. Besides, the geographical compactness of urban areas in South Korea, especially in cities such as Seoul, has also increased this demand for strategically located e-commerce warehouses.
The reason behind locating warehouses near major urban hubs is that it helps to cut down on delivery times and bring down costs of logistics, therefore providing e-commerce companies with the edge that they require in such highly competitive markets. This significant growth of the e-commerce sector is likely to keep the demand for warehousing services high during the forecast period and hence be the largest vertical in the logistics industry of South Korea.
The South Korea Warehousing Market Report is segmented on the basis of the following
By Warehousing Type
- General Warehousing
- Cold Storage Warehousing
- Automated Warehousing
- Bonded Warehousing
- Distribution Centers
By Warehousing Technology
- Manual Warehouses
- Semi-Automated Warehouses
- Fully Automated Warehouses
By Ownership Type
- Private Warehouses
- Public Warehouses
- Contract Warehouses
By Industry Vertical
- E-commerce
- Retail
- Food & Beverage
- Pharmaceuticals
- Automotive
- Electronics
How Does Artificial Intelligence Contribute To Improve South Korea Warehousing Market ?
- Warehouse Automation and Robotics: AI-driven robots are used for automated picking, sorting, packing, and palletizing, reducing manual labor costs and increasing operational speed. Automated Guided Vehicles (AGVs) and Autonomous Mobile Robots (AMRs) powered by AI streamline inventory movement within warehouses.
- Inventory Optimization: AI enables real-time inventory tracking and predictive analytics, allowing companies to forecast demand accurately, minimize stockouts or overstocking, and optimize storage space. Machine learning algorithms analyze past data trends to manage stock levels efficiently.
- Supply Chain Forecasting: AI helps predict supply chain disruptions and demand fluctuations, allowing for proactive decision-making. In South Korea’s tech-driven logistics environment, this ensures just-in-time delivery and cost efficiency, vital for industries like electronics and e-commerce.
- Labor Management: AI tools optimize workforce scheduling and productivity, ensuring tasks are allocated efficiently based on skill and availability, especially during peak periods.
- Enhanced Security and Monitoring: AI-powered surveillance systems enhance security and loss prevention, using facial recognition, anomaly detection, and real-time alerts to mitigate risks.
- Sustainability and Energy Efficiency: AI systems manage energy consumption and reduce waste, contributing to sustainable warehousing solutions in line with South Korea’s environmental goals.
South Korea Warehousing Market Competitive Landscape
The South Korean warehousing market is highly competitive, with both domestic and international players vying for market share. CJ Logistics, Lotte Global Logistics, and Hyundai Glovis have each attained significant dominance within the logistics and warehousing markets.
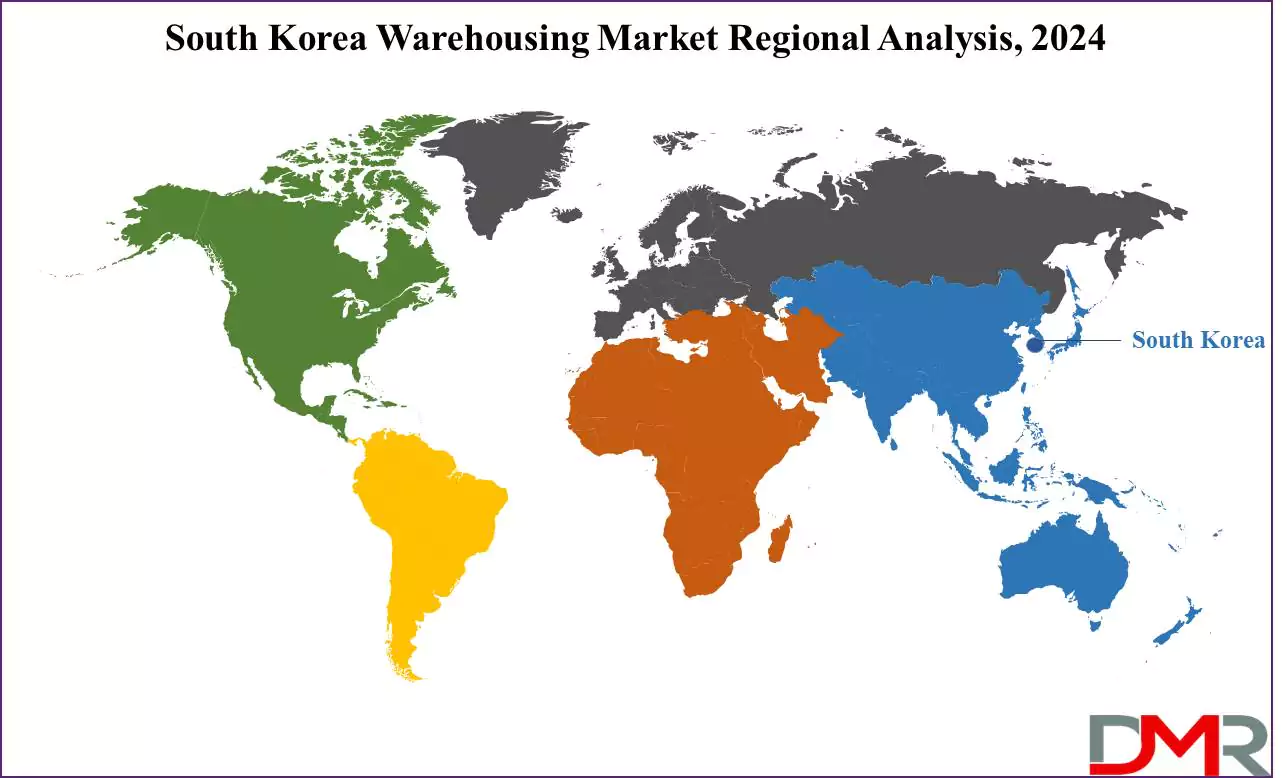
CJ Logistics stands as a market leader, capable of adapting its services across various areas such as warehousing, distribution, and value-added third-party logistics solutions. Furthermore, significant investments were made into automation technologies designed to increase operational efficiencies within areas like e-commerce fulfillment and cold chain logistics. Lotte Global Logistics stood out as another significant participant, specializing in both e-commerce fulfillment and cold chain logistics.
Their warehousing solution meets the expanding requirements of industries like pharmaceuticals and food by offering value-added inventory management with temperature-controlled storage capabilities.
Hanjin Transportation plays an active role in the South Korean warehousing market through its expertise in international trade.
Logistics companies boast both bonded and general warehousing facilities to serve both international and domestic supply chains, competing to take advantage of an ever-increasing demand for third-party logistics services and e-commerce fulfillment, constantly offering differentiated packages of differentiation based on cutting-edge integrations of technology, service quality standards, and geographic reach.
Some of the prominent players in the South Korea Warehousing Market are
- CJ Logistics Corporation
- Pantos Logistics
- DSV
- Kuehne + Nagel
- Toll Holdings Limited
- Hyundai Glovis
- LS Networks
- DB Schenker
- Samsung SDS
- Ryder System
- Nippon Express
- Seah Logistics
- Other Key Players
South Korea Warehousing Market Recent Developments
- October 2024: CJ Logistics announced the expansion of its automated warehousing network, particularly in the Seoul Metropolitan Area, to enhance its e-commerce fulfillment capacity. This move is aimed at reducing delivery times and meeting the growing demand from online retailers.
- August 2024: Lotte Global Logistics launched a state-of-the-art cold chain warehouse near Busan. This facility is expected to cater to the increasing demand for temperature-controlled logistics, particularly in the pharmaceutical and perishable goods sectors.
- July 2024: Hanjin Transportation unveiled an AI-powered warehouse management system at its main logistics center in Incheon, aimed at improving inventory tracking, order processing speed, and overall operational efficiency.
- May 2024: Amazon partnered with a local logistics provider to establish a new e-commerce fulfillment center in South Korea. The center, located near Seoul, is expected to serve as a regional hub for fast deliveries across the Asia-Pacific region.
- March 2024: The South Korean government introduced new incentives to promote investment in green warehousing technologies. These incentives are designed to encourage logistics companies to adopt environmentally friendly practices, such as solar-powered warehouses and energy-efficient systems.
- February 2024: Hyundai Glovis inaugurated a new bonded warehousing facility in Incheon, aimed at supporting the growing volume of international trade, particularly in the electronics and automotive sectors.
- December 2023: CJ Logistics introduced robotic systems in its major e-commerce fulfillment center in Seoul, enhancing its capacity to handle high volumes of orders during peak shopping seasons.
- October 2023: Lotte Global Logistics expanded its warehousing footprint in Gwangju, adding new facilities to support the rising demand for domestic retail and e-commerce logistics.